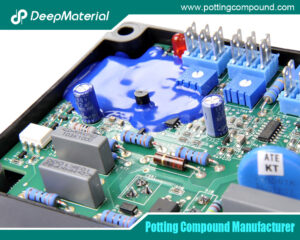
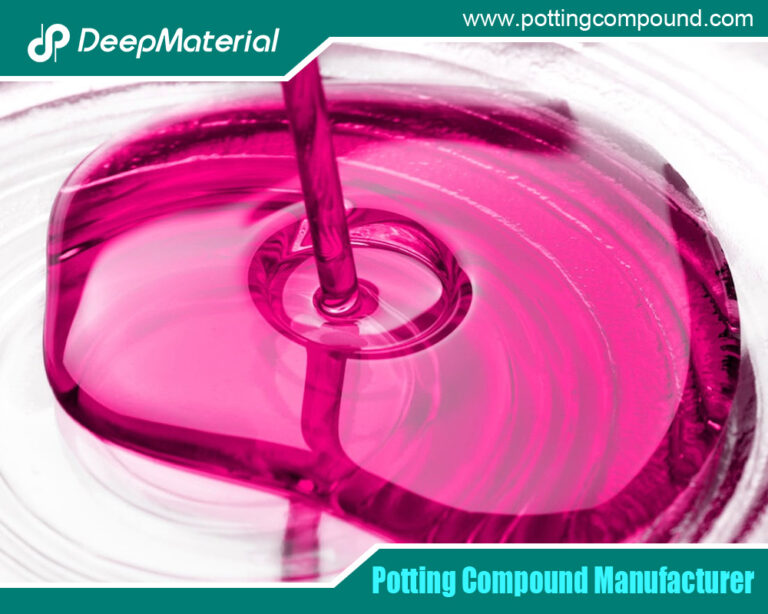
The Vital Role of Industrial Silicone Adhesive Manufacturers in Modern Industry
- Electronic Potting Material Manufacturer
- October 16, 2024
- Acrylic Conformal Coating, circuit board potting, circuit board potting compound, conformal coating electronics, conformal coating for pcb, conformal coating in electronics market, conformal coating material, Connector Potting Compound, custom automated electronics potting, Electrically Conductive Adhesive, Electronic Conformal Coating, electronic potting compound, epoxy conformal coating, epoxy potting compound, Flexible Potting Compound, Hot Melt Adhesive, Industrial Conformal Coating, industrial silicone adhesive, industrial silicone adhesive glue, industrial silicone adhesive manufacturers, LED Potting Compound, One Part Epoxy Adhesive, pcb conformal coating, polyurethane potting compound, Pressure Sensitive Adhesive, silicone adhesive manufacturers, Silicone Potting Compound, Structural Bonding Adhesive, Urethane Conformal Coating, UV Cure Conformal Coating, Waterproof Conformal Coating, waterproof potting compound
The Vital Role of Industrial Silicone Adhesive Manufacturers in Modern Industry
In today’s fast-paced industrial landscape, the demand for reliable and durable adhesives is more significant than ever. Among the various types of adhesives available, silicone adhesives stand out for their exceptional performance in multiple applications. Industrial silicone adhesives are known for their versatility, temperature resistance, and strong bonding capabilities, making them a preferred choice across diverse sectors, including automotive, aerospace, electronics, construction, and healthcare. The manufacturers of these adhesives play a crucial role in ensuring that industries have access to high-quality products that meet their specific needs. This blog post delves into the importance of industrial silicone adhesive manufacturers, the types of silicone adhesives they produce, their applications, and the future of this dynamic industry.
Understanding Industrial Silicone Adhesives
Silicone adhesives are synthetic compounds made from silicone polymers, which consist of silicon-oxygen chains. These adhesives offer unique properties that distinguish them from traditional adhesives, making them suitable for various demanding applications.
Critical Properties of Industrial Silicone Adhesives:
- High-Temperature Resistance:Silicone adhesives can withstand extreme temperatures, typically ranging from -60°C to 250°C (-76°F to 482°F), without losing their adhesive properties.
- Flexibility:They maintain flexibility even at low temperatures, allowing for movement and expansion without cracking or breaking the bond.
- Water and Chemical Resistance:Silicone adhesives are highly resistant to moisture and various chemicals, making them ideal for outdoor and industrial applications.
- Electrical Insulation:Many silicone adhesives exhibit excellent electrical insulating properties, making them suitable for electronic applications.
- UV Resistance:They provide reasonable protection against ultraviolet (UV) radiation, ensuring longevity in outdoor settings.
Types of Industrial Silicone Adhesives
Industrial silicone adhesive manufacturers produce a variety of silicone adhesives tailored to meet specific application requirements. Some of the most common types include:
Industrial silicone adhesives come in various formulations, each designed to meet specific application requirements.
One-Part Silicone Adhesives
One-part silicone adhesives are ready-to-use formulations that cure upon exposure to moisture in the air. Thanks to their ease of use and effective adhesion, they are widely utilized in the construction, automotive, and electronics industries for bonding and sealing applications.
Two-Part Silicone Adhesives
Two-part silicone adhesives consist of a base component and a curing agent that must be mixed before application. These adhesives are preferred for applications requiring a strong bond, such as aerospace and heavy machinery, where performance and durability are crucial.
Silicone Sealants
Silicone sealants are specialized silicone adhesives designed primarily for sealing gaps and joints. Commonly used in construction and automotive applications, they provide excellent flexibility and water resistance, making them ideal for outdoor environments.
Silicone Coatings
Silicone coatings are protective layers over surfaces, often used with silicone adhesives. They are widely utilized in electronics to provide insulation and protection against moisture and chemicals, enhancing the longevity of devices.
Thermal Silicone Adhesives
These adhesives are engineered for applications requiring superior thermal conductivity, making them suitable for electronic devices where heat dissipation is essential. By efficiently managing heat, they help maintain optimal performance in high-power applications.
The Manufacturing Process of Industrial Silicone Adhesives
The production of industrial silicone adhesives involves several stages, each critical to ensuring the final product meets the necessary quality and performance standards. Here’s an overview of the manufacturing process:
Raw Material Selection
- Silicone Polymers:Silicone polymers, sourced from high-quality suppliers, are the primary ingredient in silicone adhesives.
- Additives:Various additives, such as curing agents, fillers, and stabilizers, enhance specific properties.
Mixing
- Formulation:The selected raw materials are precisely measured and mixed in controlled environments to create a uniform adhesive formulation.
- Quality Control:Continuous quality checks are conducted to ensure consistency in the formulation.
Curing
- Curing Process:The adhesive is subjected to specific conditions, which may involve heat or moisture, depending on whether it is a one-part or two-part adhesive.
- Time Management:Manufacturers closely monitor the curing time to achieve the desired properties.
Packaging
- Quality Assurance:After curing, the adhesives undergo rigorous quality testing to meet industry standards.
- Final Packaging:The adhesives are packaged in appropriate containers for distribution.
Applications of Industrial Silicone Adhesives
Industrial silicone adhesives find applications in various sectors due to their unique properties. Here are some key areas where they are commonly used:
Automotive Industry
- Bonding and Sealing:Used for bonding windshields, sealing headlights, and securing various automotive components.
- Thermal Management:Employed in applications requiring thermal insulation and management.
Aerospace Industry
- Component Assembly:Due to their lightweight and robust bonding capabilities, silicone adhesives assemble critical components, such as panels and avionics.
- Sealing: Employed for sealing fuel tanks and ensuring airtight compartments.
Electronics Industry
- Encapsulation:Silicone adhesives are widely used to encapsulate electronic components and protect them from moisture, chemicals, and mechanical stress.
- Electrical Insulation:Their excellent insulating properties make them suitable for use in circuit boards and connectors.
Construction Industry
- Joint Sealing:This material seals joints and gaps in buildings to improve energy efficiency and prevent moisture infiltration.
- Bonding:This adhesive is employed to bond various materials, including glass, metal, and plastics, in construction applications.
Healthcare
- Medical Devices:Silicone adhesives manufacture medical devices, providing reliable bonding and flexibility.
- Skin Adhesives: Employed in surgical applications and wound dressings due to their biocompatibility.
The Role of Industrial Silicone Adhesive Manufacturers
Manufacturers of industrial silicone adhesives are essential to the supply chain, providing products that meet industry-specific needs. Their roles can be broken down into several key areas:
Research and Development
- Innovative Formulations:Manufacturers invest in R&D to develop new silicone adhesive formulations that improve performance, reduce curing times, and enhance application versatility.
- Adapting to Market Needs:Ongoing research allows manufacturers to stay ahead of market trends and adjust their products to meet emerging industry demands.
Quality Assurance
- Rigorous Testing:Manufacturers implement strict quality control measures, testing their adhesives for performance, durability, and compliance with industry standards.
- Certifications:Many manufacturers obtain certifications to demonstrate their products’ safety and effectiveness, enhancing their credibility in the Market.
Customer Support and Training
- Technical Assistance:Manufacturers provide technical support to help customers select the suitable adhesives for their applications and ensure proper usage.
- Training Programs:Some manufacturers offer training programs to educate customers on the best practices for using silicone adhesives effectively.
Sustainability Initiatives
- Eco-Friendly Products:Many manufacturers are committed to developing eco-friendly silicone adhesives with lower environmental impact and reduced VOC emissions.
- Sustainable Manufacturing Practices:Manufacturers adopt sustainable practices in their production processes, focusing on waste reduction and energy efficiency.
Challenges Facing Industrial Silicone Adhesive Manufacturers
While the Market for industrial silicone adhesives is growing, manufacturers face several challenges:
Raw Material Costs
- Price Fluctuations:The prices of raw materials used in silicone adhesive production can fluctuate significantly, impacting manufacturing costs and pricing strategies.
Regulatory Compliance
- Evolving Regulations:Manufacturers must stay updated on changing regulations regarding chemical safety, environmental impact, and product performance.
Market Competition
- Intense Competition:The adhesive Market is becoming increasingly competitive, requiring manufacturers to innovate and differentiate their products continuously.
Conclusion
Industrial silicone adhesive manufacturers play a critical role in supplying high-quality adhesives that meet the diverse needs of modern industries. With their unique properties, silicone adhesives are vital in various applications, providing durability, flexibility, and resistance to environmental factors. As manufacturers continue to innovate and adapt to market demands, the future of industrial silicone adhesives looks promising. By addressing challenges and embracing trends such as sustainability and technological advancements, manufacturers will be well-positioned to thrive in an increasingly competitive landscape. The importance of these manufacturers cannot be overstated, as their products are essential for the reliability and performance of a wide range of industrial applications.
For more about choosing the vital role of industrial silicone adhesive manufacturers in modern industry, you can pay a visit to DeepMaterial at https://www.pottingcompound.com/ for more info.
Recent Posts
- Influence of Encapsulation Thickness on the Heat Dissipation Performance and Electrical Insulation Performance of PCB
- Causes and Avoidance Methods of Bubble Generation in the Potting Process
- Technical Details on Controlling Parameters such as Temperature, Pressure, and Speed in the Potting Process to Ensure Potting Quality
- A Comprehensive Analysis of PCB Pretreatment Before Potting Process: A Crucial Link to Ensure the Performance and Reliability of Electronic Devices
- A Comprehensive Analysis of the Performance Differences of Epoxy Resin, Silicone Rubber and Polyurethane Encapsulation Materials
- How to Select Suitable Potting Materials for PCB According to the Working Environment
- What is PCB Potting
- The Evolution of Smart Watch Assembly Adhesive: A Key Component in Modern Wearable Technology
- Laptop Tablet Assembly Adhesive: The Key to Durable and Reliable Device Construction
- Power Bank Assembly Adhesive: The Essential Component for Building Durable Power Banks