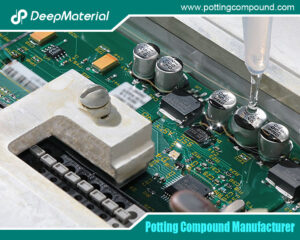
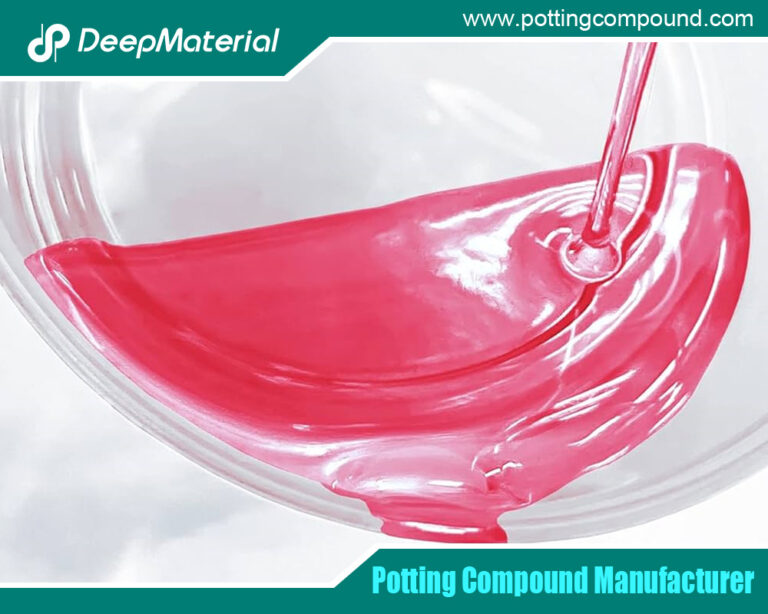
Understanding BGA Underfill Epoxy Adhesive
- Electronic Potting Material Manufacturer
- August 9, 2024
- adhesive glue manufacturer, BGA underfill epoxy adhesive, BGA underfill epoxy adhesive glue, conformal coating for pcb standards, conformal coating waterproof, deepmaterial epoxy adhesive glue, deepmaterial PCB Potting, deepmaterial potting compound, electronic board level underfill and encapsulation material market, electronic epoxy encapsulant potting compounds, electronics encapsulation epoxy adhesive, electronics encapsulation epoxy adhesive glue, electronics epoxy adhesive, encapsulation epoxy adhesive, epoxy adhesive, epoxy encapsulation electronic components, epoxy potting compound, epoxy resin encapsulation, industrial adhesive suppliers, One Part Epoxy Adhesive, pcb encapsulation epoxy, pcb encapsulation epoxy adhesive glue, potting compound for electronics, potting compound vs epoxy, silicone epoxy adhesive glue, underfill epoxy adhesive, underfill epoxy adhesive glue, UV curing potting compound
Understanding BGA Underfill Epoxy Adhesive
Ball Grid Array (BGA) underfill epoxy adhesive is a specialised material used in the electronics industry to enhance the reliability and performance of BGA packages. These adhesives fill the space between a BGA chip and the substrate, providing mechanical reinforcement, thermal stability, and protection against environmental stressors. This article delves into the specifics of BGA underfill epoxy adhesive, its importance, application process, and benefits.
Introduction to BGA Underfill Epoxy Adhesive
What is BGA Underfill?
Ball Grid Array (BGA) is a type of surface-mount packaging used for integrated circuits. Unlike traditional packages with pins around the edges, BGA uses an array of solder balls underneath the package to connect to the PCB (Printed Circuit Board). This design allows for more connections, better heat dissipation, and electrical efficiency performance. However, the solder joints in BGAs can be vulnerable to mechanical stresses, such as thermal cycling and physical impacts.
The Role of Underfill Epoxy Adhesive
Underfill epoxy adhesive is crucial in enhancing the durability and longevity of BGA packages. This adhesive is applied to the gap between the BGA chip and the PCB after the soldering process. Once cured, it forms a strong bond that distributes mechanical stress, protects against environmental factors, and improves the assembly’s thermal performance.
Types of BGA Underfill Epoxy Adhesive
Several underfill epoxy adhesives are available, each with specific properties tailored to different applications. The main types include:
Capillary Flow Underfill
Capillary flow underfill adhesives are designed to flow into the narrow spaces between the BGA and the PCB through capillary action. These adhesives typically have low viscosity and are applied after the soldering process. They provide excellent stress distribution and are commonly used in consumer electronics.
No-Flow Underfill
No-flow underfill adhesives are applied before the reflow soldering process. These adhesives are designed to remain in place during soldering and cure during reflow. No-flow underfills offer advantages in terms of process simplification and are often used in high-volume manufacturing.
Molded Underfill
Molded underfill adhesives are applied using a molding process. This method allows for precise control over the underfill material and is suitable for high-reliability applications where consistent performance is critical. Molded underfill is often used in advanced electronics, such as aerospace and automotive applications.
Application Process of BGA Underfill Epoxy Adhesive
Applying BGA underfill epoxy adhesive is a critical step in the assembly process. The following steps outline the general process:
Surface Preparation
Before applying the underfill adhesive, it is essential to ensure that the surfaces of the BGA and PCB are clean and free of contaminants. Proper cleaning ensures good adhesion and prevents defects.
Adhesive Application
For capillary flow underfill, the adhesive is dispensed around the edges of the BGA package. The adhesive flows into the gap through capillary action, filling the space between the chip and the PCB. For no-flow underfill, the adhesive is dispensed before placing the BGA on the PCB, and for moulded underfill, the adhesive is applied using a moulding process.
Curing Process
The curing process involves heating the assembly to a specific temperature for a defined period. This step ensures the underfill adhesive fully cures and forms a strong bond. The curing profile depends on the type of adhesive used and the manufacturer’s specifications.
Benefits of Using BGA Underfill Epoxy Adhesive
The use of BGA underfill epoxy adhesive offers several benefits that enhance the performance and reliability of electronic assemblies:
Improved Mechanical Strength
Underfill adhesive significantly improves the mechanical strength of BGA packages. By filling the gap between the chip and the PCB, the adhesive distributes mechanical stresses, such as those caused by thermal cycling, vibrations, and physical impacts. This reduces the likelihood of solder joint failure and enhances the overall durability of the assembly.
Enhanced Thermal Performance
BGA underfill epoxy adhesive improves thermal performance by providing a conductive path for heat dissipation. This is particularly important in high-power applications where efficient heat management is critical. The adhesive helps to dissipate heat away from the chip, reducing the risk of thermal damage and improving the reliability of the assembly.
Environmental Protection
Underfill adhesive protects against environmental stressors like moisture, dust, and chemicals. This protection is crucial in harsh environments where electronic assemblies are exposed to extreme conditions. The adhesive helps to prevent corrosion and contamination, ensuring long-term reliability.
Reduced Risk of Solder Joint Failure
The primary purpose of underfill adhesive is to reduce the risk of solder joint failure. By distributing mechanical stresses and providing additional support, the adhesive minimises the likelihood of cracks and fractures in the solder joints. This is especially important in applications where the assembly is subjected to repeated thermal cycling and mechanical stress.
Critical Considerations for Selecting BGA Underfill Epoxy Adhesive
When selecting a BGA underfill epoxy adhesive, several factors must be considered to ensure optimal performance and reliability:
Viscosity
The viscosity of the underfill adhesive affects its flow characteristics and ability to fill narrow gaps. Low-viscosity adhesives are suitable for capillary flow applications, while higher-viscosity adhesives are used in no-flow and molded underfill processes.
Curing Profile
The curing profile, including the temperature and time required, is a critical consideration. The adhesive must be compatible with the assembly process and should not cause thermal damage to the components.
Thermal Conductivity
Thermal conductivity is an essential factor in applications requiring efficient heat dissipation. High—thermal—conductivity adhesives help manage heat effectively and prevent thermal damage to components.
Adhesion Strength
Adhesion strength ensures a strong bond between the BGA package and the PCB. The adhesive should provide sufficient adhesion to withstand mechanical stresses and environmental conditions.
Compatibility with Materials
The underfill adhesive must be compatible with the materials used in the BGA package and the PCB, including the solder mask, substrate, and other assembly components.
Challenges and Solutions in Using BGA Underfill Epoxy Adhesive
Voiding
Voiding can occur during the underfill process if air bubbles are trapped in the adhesive. This can lead to reduced mechanical strength and thermal performance. To minimise voiding, it is essential to use proper dispensing techniques and ensure that the adhesive flows smoothly into the gap.
Delamination
Delamination occurs when the underfill adhesive separates from the surfaces of the BGA package or the PCB. This can result from poor adhesion, contamination, or thermal cycling. Proper surface preparation and selection of compatible adhesives are crucial to preventing delamination.
Thermal Mismatch
A thermal mismatch between the underfill adhesive and the components can cause stress and deformation during temperature changes. Selecting adhesives with coefficients similar to the components’ thermal expansion (CTE) can help mitigate thermal mismatch issues.
Process Control
Maintaining precise process control is essential to ensure consistent and reliable underfill application. This includes controlling dispensing parameters, curing profiles, and environmental conditions during assembly.
Future Trends in BGA Underfill Epoxy Adhesive
The electronics industry is constantly evolving, and advancements in BGA underfill epoxy adhesive technology continue to drive improvements in performance and reliability. Some of the future trends in this field include:
Advanced Materials
The development of advanced materials with enhanced properties, such as higher thermal conductivity, improved adhesion strength, and better environmental resistance, will continue to enhance the performance of BGA underfill adhesives.
Nano-Enhanced Adhesives
Nano-enhanced adhesives, incorporating nanoparticles to improve thermal and mechanical properties, are gaining traction. These adhesives offer superior performance in terms of heat dissipation and stress distribution.
Automated Dispensing Systems
Advancements in automated dispensing systems enable precise and consistent application of underfill adhesives. These systems improve process control, reduce variability, and enhance the overall reliability of the assembly.
Environmentally Friendly Formulations
The demand for environmentally friendly formulations is increasing. Manufacturers are developing underfill adhesives with reduced volatile organic compounds (VOCs) and other environmentally harmful substances to meet regulatory requirements and sustainability goals.
Conclusion
BGA underfill epoxy adhesive is a critical component in the electronics industry, providing mechanical reinforcement, thermal stability, and environmental protection to BGA packages. The selection and application of the appropriate underfill adhesive are essential to ensure the reliability and performance of electronic assemblies. With ongoing advancements in materials and technology, the future of BGA underfill epoxy adhesives looks promising, offering enhanced performance and sustainability for next-generation electronic devices.
For more about understanding BGA underfill epoxy adhesive, you can pay a visit to DeepMaterial at https://www.pottingcompound.com/ for more info.
Recent Posts
- Silicone Potting Compound for Electronics
- Potting Compound vs. Epoxy: A Comprehensive Comparison
- Potting Compound for PCB
- In – depth Analysis of the Curing Characteristics of Electronic Potting Compounds
- A Comprehensive Analysis of the Environmental Performance of Encapsulating Materials: From Regulations to Practices
- A Comprehensive Analysis of PCB Encapsulation Quality Inspection: Innovative Application of Non-Destructive Testing Technologies
- Analysis of the Improvement of the Seismic and Impact Resistance Performance of PCB by Encapsulation
- A Comprehensive Guide to Evaluating the Reliability of Encapsulation Materials for Encapsulated PCBs
- In-depth Analysis of the Reparability of Encapsulation Materials
- A Comprehensive Analysis of Post-Potting PCB Issues and the Repair and Rework of Potting Materials