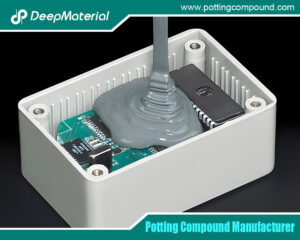
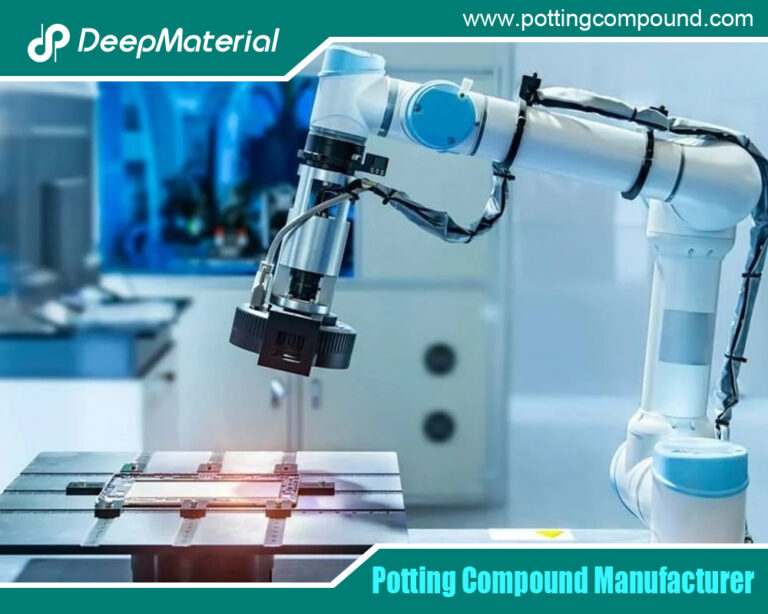
Understanding Electric Motor Potting Compounds: A Comprehensive Guide
- Electronic Potting Material Manufacturer
- November 29, 2024
- Acrylic Conformal Coating, Connector Potting Compound, electric motor potting compound, electric motor potting compound china hotsale, electric motor potting compound china OEM, electric motor potting compound china wholesale, electric motor potting compound factory hotsale, electric motor potting compound factory OEM, electric motor potting compound factory wholesale, electric motor potting compound manufacturer, electric motor potting compound supplier, Electronic Conformal Coating, electronic potting compound, Flexible Potting Compound, Industrial Conformal Coating, LED Potting Compound, pcb conformal coating, PCB Potting Compound, polyurethane potting compound, Silicone Potting Compound, UV Cure Potting Compound, Waterproof Conformal Coating, waterproof potting compound
Understanding Electric Motor Potting Compounds: A Comprehensive Guide
Electric motor potting compounds play a crucial role in the longevity and efficiency of electric motors. These compounds are used to encapsulate electrical components, providing insulation, protection against environmental factors, and enhancing the mechanical stability of the motor. As electric motors continue to be integral in various industries, understanding the properties and applications of potting compounds is essential for engineers, manufacturers, and maintenance professionals. This article delves into the significance of electric motor potting compounds, their types, benefits, application processes, and considerations for choosing a suitable compound.
What Are Electric Motor Potting Compounds?
Electric motor potting compounds are viscous materials applied to encapsulate electrical components in motors. Potting protects sensitive components from moisture, dust, chemicals, and physical damage.
Key Characteristics
- Insulation:Provides electrical insulation to prevent short circuits.
- Thermal Management:Helps dissipate heat generated during operation.
- Environmental Protection: Shields components from moisture, corrosion, and contaminants.
- Mechanical Stability:Reduces vibration and mechanical stress on components.
Types of Potting Compounds
Potting compounds come in various formulations, each with unique properties suited for different applications. The most common types include:
1. Epoxy-Based Compounds
- Properties:High strength, excellent adhesion, and resistance to moisture and chemicals.
- Applications: Widely used in high-performance motors where durability is essential.
2. Silicone-Based Compounds
- Properties:Flexible, temperature resistant, and excellent for high-vibration environments.
- Applications:Ideal for applications involving extreme temperatures and movements.
3. Polyurethane Compounds
- Properties:Good flexibility, impact resistance, and moderate thermal stability.
- Applications: Commonly used in consumer electronics and automotive motors.
4. Acrylic Compounds
- Properties:Fast curing, UV resistance, and sound clarity.
- Applications:Used in applications where visibility of components is crucial.
Benefits of Using Potting Compounds in Electric Motors
The application of electric motor potting compounds offers numerous advantages:
Enhanced Durability
- Protective Barrier: This creates a solid barrier against environmental factors.
- Extended Lifespan:Reduces the risk of component failure, leading to longer operational life.
Improved Performance
- Thermal Efficiency:Helps with heat management and maintaining optimal operating temperatures.
- Vibration Dampening: Minimizes vibration-induced wear and tear.
Cost-Effectiveness
- Reduced Maintenance:Less frequent repairs and replacements due to enhanced protection.
- Operational Efficiency:Improves overall motor efficiency, leading to lower energy costs.
Application Process of Potting Compounds
Step 1: Preparation
- Surface Cleaning:Ensure all surfaces are free of dust, grease, and contaminants.
- Component Inspection:Check for any damage or defects before potting.
Step 2: Mixing the Compound
- Follow Manufacturer Instructions: Mix components as per guidelines to achieve desired properties.
- Vacuum Degassing:Remove air bubbles to ensure even distribution.
Step 3: Application
- Pouring: Carefully pour the compound over the components to ensure complete encapsulation.
- Curing:For optimal results, allow the compound to heal at the specified time and temperature.
Step 4: Final Inspection
- Quality Check:Inspect for any voids or imperfections after curing.
- Testing: Conduct electrical and thermal tests to ensure functionality.
Considerations for Choosing the Right Potting Compound
Selecting the appropriate electric motor potting compound requires careful consideration of several factors:
1. Operating Environment
- Temperature Range:Consider compounds that can withstand the specific temperature ranges of your application.
- Moisture Exposure:Choose moisture-resistant compounds for outdoor or humid environments.
2. Mechanical Requirements
- Vibration Resistance: Opt for flexible compounds in high-vibration applications.
- Strength Needs: Assess the mechanical strength requirements based on the motor’s operating conditions.
3. Electrical Properties
- Dielectric Strength: Ensure the compound has suitable electrical insulation properties.
- Thermal Conductivity:Consider compounds that offer efficient heat dissipation.
4. Cure TimeTime
- Production Efficiency: Select compounds with suitable curing times to optimize production schedules.
5. Cost and Availability
- Budget Constraints:Evaluate compounds within budget while meeting all requirements.
- Supplier Reliability:Choose suppliers with a proven quality and service track record.
Common Applications of Electric Motor Potting Compounds
Electric motor potting compounds find use in various industries and applications:
1. Automotive Industry
- Electric Vehicles: Protect electric motors and battery management systems from environmental damage.
- High-Performance Engines:Enhance durability and efficiency in high-stress environments.
2. Consumer Electronics
- Home Appliances: Protect motors in devices such as washing machines and vacuum cleaners.
- Computers:Encapsulate motors in cooling fans and drives.
3. Aerospace and Defense
- Reliability in Extreme Conditions: Protect critical components in aircraft and military applications.
- Long-Term Stability:Ensure functionality in varying atmospheric conditions.
4. Industrial Machinery
- Heavy Equipment: Shield motors from dust and contaminants in manufacturing and construction.
- Robotics: Enhance reliability in automated systems.
Challenges and Limitations of Potting Compounds
Despite their benefits, there are challenges associated with electric motor potting compounds:
Potting Removal
- Difficulties in Maintenance:Removing cured potting compounds can be labor-intensive and may damage components.
- Rework Complexity: Rework of potted components can be more complicated than non-potted designs.
Curing Issues
- Incomplete Curing:Improper curing can lead to performance issues, including reduced insulation properties.
- Temperature Sensitivity: Some compounds require specific temperature conditions for proper curing.
Chemical Compatibility
- Adverse Reactions:Ensure compatibility with encapsulated materials to avoid reactions that can degrade performance.
- Long-Term Stability:Consider the long-term effects of environmental exposure on the potting material.
Innovations in Electric Motor Potting Compounds
The field of electric motor potting compounds is continually evolving, driven by advancements in materials science and the growing demands of various industries. Innovations in this area aim to improve performance, enhance durability, and address specific challenges manufacturers and engineers face.
1. Bio-Based Potting Compounds
With an increasing focus on sustainability, the development of bio-based potting compounds has gained traction. These compounds are derived from renewable resources and aim to reduce environmental impact.
- Eco-Friendly Alternatives:Bio-based compounds can offer similar protective properties to traditional options while minimizing carbon footprints.
- Market Demand:The push for greener technologies drives demand for eco-friendly materials, making bio-based options viable for manufacturers.
2. Advanced Thermal Management Solutions
Effective thermal management is critical in electric motor applications, mainly as motors operate at higher efficiencies and power levels.
- Enhanced Conductivity:New formulations are being developed with improved thermal conductivity, which allows for better heat dissipation and maintains optimal operating temperatures.
- Phase Change Materials:Incorporating phase change materials into potting compounds can help manage heat by absorbing and releasing thermal energy, ensuring stable operating conditions.
3. Smart Potting Compounds
Integrating intelligent technologies into potting compounds is a game-changer for the electric motor industry.
- Sensors and Monitoring:Smart potting compounds can include embedded sensors that monitor temperature, humidity, and even electrical performance, providing real-time data for predictive maintenance.
- Self-Healing Properties:Research into self-healing materials is underway, allowing potting compounds to repair minor damage autonomously, thereby extending the lifespan of electrical components.
4. Custom Formulations
As industries become more specialized, the demand for customized potting compounds is rising.
- Tailored Solutions:Manufacturers can create specific formulations that cater to unique environmental conditions or performance requirements, such as increased flexibility or enhanced chemical resistance.
- Collaboration with Engineers: Collaborating closely with engineers and designers ensures that the potting compounds meet the precise needs of the application, improving performance and reliability.
Regulatory and Compliance Considerations
Depending on the application and industry, using electric motor potting compounds is subject to various regulations and standards.
1. Material Safety Data Sheets (MSDS)
Manufacturers must provide Material Safety Data Sheets for their potting compounds, detailing the materials’ properties, handling precautions, and health effects.
- Safety Compliance:Understanding and complying with safety regulations is essential for ensuring the well-being of workers and users.
- Proper Handling:MSDS documents also guide appropriate handling and storage to prevent accidents.
2. Environmental Regulations
With heightened awareness of environmental issues, potting compound manufacturers must comply with chemical emissions and waste disposal regulations.
- REACH Compliance:In Europe, for example, the Registration, Evaluation, Authorisation, and Restriction of Chemicals (REACH) regulation ensures that product chemicals do not harm human health or the Environment.
- Sustainability Goals:Companies increasingly strive to align with sustainability goals by selecting compliant and environmentally friendly materials.
Conclusion
Electric motor potting compounds are essential for ensuring the reliability and efficiency of electric motors across various industries. By understanding the types, benefits, and application processes of these compounds, professionals can make informed decisions that enhance the performance and lifespan of their electric motors. As technology advances and demands for electric motors increase, the importance of effective potting solutions will only grow, making it imperative for stakeholders to stay updated on the latest developments and best practices in potting compounds. Investing in a suitable electric motor potting compound protects your equipment and contributes to overall operational efficiency and cost savings.
For more about understanding electric motor potting compounds: a comprehensive guide, you can pay a visit to DeepMaterial at https://www.pottingcompound.com/ for more info.
Recent Posts
- Causes and Avoidance Methods of Bubble Generation in the Potting Process
- Technical Details on Controlling Parameters such as Temperature, Pressure, and Speed in the Potting Process to Ensure Potting Quality
- A Comprehensive Analysis of PCB Pretreatment Before Potting Process: A Crucial Link to Ensure the Performance and Reliability of Electronic Devices
- A Comprehensive Analysis of the Performance Differences of Epoxy Resin, Silicone Rubber and Polyurethane Encapsulation Materials
- How to Select Suitable Potting Materials for PCB According to the Working Environment
- What is PCB Potting
- The Evolution of Smart Watch Assembly Adhesive: A Key Component in Modern Wearable Technology
- Laptop Tablet Assembly Adhesive: The Key to Durable and Reliable Device Construction
- Power Bank Assembly Adhesive: The Essential Component for Building Durable Power Banks
- Smartphone Assembly Adhesive: Enhancing Durability and Precision in Modern Devices