Understanding Potting Compound in Electronics
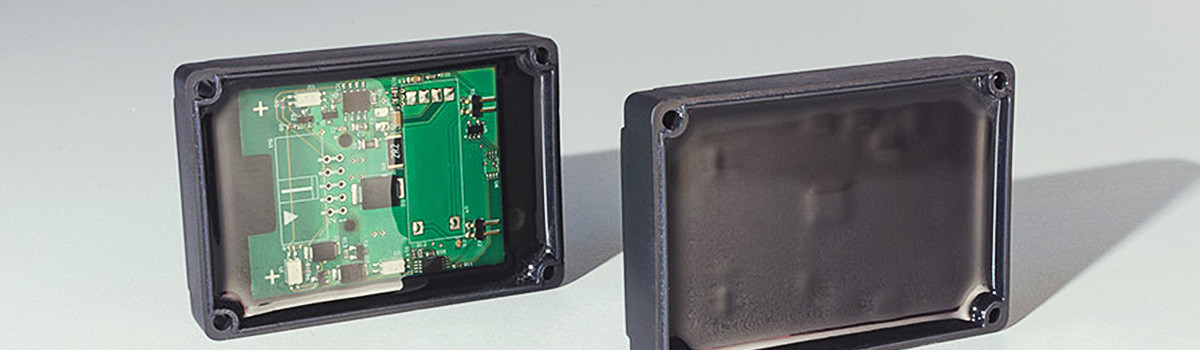
Potting compound plays a crucial role in electronics by providing protection, insulation, and stabilization to sensitive electronic components. This specialized material is widely used in various industries to safeguard electronic devices from environmental factors such as moisture, vibration, and thermal stress. Understanding the significance and applications of potting compounds is essential for engineers, technicians, and enthusiasts working in electronics.
Table of Contents
ToggleFundamental Concepts You Ought to Understand:
What is a potting compound in electronics?
Potting compound, or potting material or encapsulant, is used in electronics to protect delicate components and circuitry from environmental factors such as moisture, dust, chemicals, vibration, and physical impact. It’s a crucial aspect of electronic manufacturing, especially for devices exposed to harsh conditions or needing to maintain reliability over extended periods.
The primary purpose of potting compounds is to encapsulate electronic assemblies, effectively sealing them from external elements. This encapsulation process involves pouring or injecting the compound around the electronic components, ensuring they are surrounded and insulated. Once cured, the compound forms a solid protective layer that adheres to the components and the housing, creating a barrier against moisture, contaminants, and mechanical stress.
Potting compounds come in various formulations to suit different application requirements. Common types include epoxy, silicone, polyurethane, and acrylic compounds. Each type offers distinct properties such as flexibility, thermal conductivity, chemical resistance, and adhesion strength.
Epoxy potting compounds are widely used for their excellent adhesion and mechanical properties. They provide strong protection against moisture and chemicals, making them suitable for harsh environments. Silicone potting compounds offer high flexibility and thermal stability, making them ideal for extreme temperatures or thermal cycling applications. Polyurethane and acrylic compounds provide a balance of properties, including good adhesion, flexibility, and resistance to yellowing under UV exposure.
Choosing the suitable potting compound depends on factors such as the operating environment, desired level of protection, thermal management requirements, and compatibility with other materials in the assembly.
In addition to protection, potting compounds can enhance electronic assemblies’ structural integrity by providing mechanical support and damping vibrations. However, proper selection or application of potting materials can lead to adequate protection, thermal management problems, or difficulties in repair and rework.
Overall, potting compound plays a crucial role in ensuring the reliability and longevity of electronic devices by safeguarding them against environmental hazards and mechanical stresses. Its use is essential in various industries, including automotive, aerospace, telecommunications, and industrial electronics.
How does potting compound differ from other types of electronic coatings?
Potting compounds and other electronic coatings protect electronic components from environmental factors such as moisture, dust, chemicals, and mechanical stress. While they share this common objective, they differ in their application methods, material compositions, and the level of protection they offer.
A potting compound is an encapsulation material surrounding electronic components, forming a solid protective barrier. It is typically a two-part epoxy resin mixed and poured over the component, then allowed to cure, creating a hardened enclosure. Due to its solid, durable nature, potting provides excellent protection against moisture, dust, vibration, and mechanical shock. It also offers good thermal insulation, which can benefit specific electronic applications.
On the other hand, electronic coatings, such as conformal coatings, are applied as thin layers over the surface of electronic assemblies. These coatings can be sprayed, brushed, or dipped onto the components, forming a protective film. Conformal coatings are usually made from acrylics, silicones, urethanes, or epoxies. They provide a protective barrier against moisture, dust, and chemical contaminants, allowing flexibility and breathability. Conformal coatings are advantageous for applications where flexibility or reworkability is required, as they can be removed and reapplied relatively easily.
One key difference between potting compounds and conformal coatings is their level of coverage and protection. Potting compound completely encases the electronic component, providing maximum protection but making rework or repair complex. Conversely, conformal coatings offer a lighter, more flexible layer of protection that allows more accessible access to the components for maintenance or repair.
Additionally, the choice between potting compound and conformal coatings may depend on the specific requirements of the application, such as environmental conditions, desired level of protection, thermal management needs, and ease of application. Both types of materials play essential roles in safeguarding electronic devices and assemblies, with their suitability determined by the unique demands of each application.
What are the primary functions of potting compounds?
Potting compound, or potting resin or encapsulant, serves several primary functions across various industries, primarily in electronics and manufacturing. Here are the critical tasks of potting compounds:
- Environmental Protection: Potting compounds create a protective barrier around electronic components, shielding them from environmental factors such as moisture, dust, chemicals, and vibrations. This protection is crucial for extending the lifespan and reliability of sensitive electronic devices, particularly those exposed to harsh conditions like outdoor environments or industrial settings.
- Insulation: Potting compounds act as insulators, preventing electrical conductivity between components and reducing the risk of short circuits or electrical malfunctions. By encapsulating electronic assemblies, potting compounds help maintain the integrity of circuitry and prevent damage caused by electrical interference or arcing.
- Mechanical Support: Potting compounds provide structural support to delicate components, preventing mechanical stresses, shock, or physical damage. This support is essential for maintaining the alignment and positioning of components within an assembly, particularly in applications subject to mechanical impact or handling.
- Thermal Management: Some potting compounds are formulated with thermal properties to dissipate heat generated by electronic components. By efficiently transferring heat from sensitive components, these compounds help prevent overheating and ensure optimal performance and reliability, especially in high-power applications or confined spaces with limited airflow.
- Chemical Resistance: Potting compounds resist various chemicals, including solvents, fuels, and acids, which helps protect electronic assemblies from corrosion or degradation when exposed to harsh chemical environments. This resistance is critical for applications such as automotive, aerospace, and industrial equipment, where exposure to chemicals is everyday.
- Enhanced Electrical Performance: Certain potting compounds are designed to improve electrical performance by reducing signal interference, minimizing capacitance, or enhancing dielectric properties. These compounds contribute to electronic systems’ overall efficiency and functionality, particularly in high-frequency applications or where precise electrical characteristics are required.
- Ease of Manufacturing: Potting compounds facilitate efficient manufacturing processes by simplifying assembly procedures, reducing the need for additional components (such as housing or protective enclosures), and enabling automated dispensing or molding techniques. This streamlining of manufacturing operations can lead to cost savings and improved productivity for manufacturers.
Potting compounds play a crucial role in protecting, insulating, supporting, and enhancing the performance of electronic assemblies across various industries, ensuring reliability, durability, and functionality in demanding applications.
What materials are commonly used in potting compounds?
Potting compounds are essential materials used in electronics and electrical engineering to encapsulate and protect delicate components from environmental factors such as moisture, vibration, and thermal cycling. These compounds typically comprise a resin system and various additives to achieve desired properties. Several materials find everyday use in potting compounds:
- Epoxy Resins: Epoxy resins are among the most widely used materials in potting compounds due to their excellent adhesion, chemical resistance, and mechanical properties. They provide strong insulation and protection against environmental stress.
- Polyurethane Resins: Polyurethane resins offer flexibility and good resistance to moisture and chemicals. They are often chosen for applications requiring a softer, more resilient encapsulant.
- Silicone Resins: Silicone resins exhibit exceptional thermal stability, moisture resistance, and flexibility over a wide temperature range. They are frequently utilized in high-temperature applications or where extreme environmental conditions are expected.
- Acrylic Resins: Acrylic resins offer fast curing times and good adhesion properties. They are commonly used in applications requiring rapid processing and high throughput.
- Fillers and Reinforcements: Various fillers such as silica, glass fibers, or mineral fillers are added to potting compounds to enhance properties like thermal conductivity, mechanical strength, and flame resistance.
- Curing Agents and Catalysts: Chemical additives like hardeners or catalysts are essential in potting compounds to initiate and control the curing process. They determine the final properties of the encapsulant.
- Modifiers: Modifiers such as plasticizers or flame retardants may be incorporated to tailor specific properties like flexibility, flame resistance, or electrical conductivity to meet application requirements.
- Solvents and Diluents: Solvents or diluents are sometimes used to adjust the viscosity of the potting compound for ease of application or to facilitate penetration into intricate components.
- Colorants and UV Stabilizers: Colorants are added for aesthetic purposes or to differentiate between different formulations. UV stabilizers may also be included to prevent degradation from exposure to ultraviolet radiation.
- Adhesion Promoters: Adhesion promoters improve bonding between the potting compound and substrate materials, ensuring robust encapsulation.
By carefully selecting and combining these materials, engineers can tailor potting compounds to meet the specific requirements of various electronic and electrical applications, ensuring optimal performance and reliability of encapsulated components.
How does a potting compound protect electronic components from moisture?
A potting compound, also known as encapsulant or potting material, serves as a protective barrier for electronic components against various environmental factors, particularly moisture. This compound is typically a two-part epoxy resin that, when mixed and cured, forms a solid and chemically inert material. Here’s how potting compound safeguards electronic components from moisture in 300 words:
- Physical Barrier: A potting compound creates a physical barrier around electronic components, effectively encapsulating them within a protective shell. This barrier prevents moisture from reaching sensitive electronic parts, including printed circuit boards (PCBs), integrated circuits (ICs), and connectors.
- Sealing Effect: The potting compound fills gaps, crevices, and voids around electronic components, providing a complete seal against moisture ingress. Even minute openings that could allow moisture infiltration are effectively sealed, enhancing the overall protection of the electronics.
- Chemical Inertness: Potting compounds are chemically inert materials, meaning they do not react with moisture or other environmental elements that may cause corrosion or degradation of electronic components. This inertness ensures the long-term integrity of the protective barrier against moisture-related damage.
- Water Repellency: Many potting compounds exhibit hydrophobic properties, repelling water and preventing it from penetrating the encapsulated electronic components. This characteristic further enhances the moisture resistance of the protective barrier, especially in applications where exposure to water or humidity is a concern.
- Thermal Stability: Potting compounds often possess excellent thermal stability, maintaining their protective properties even under fluctuating temperature conditions. This stability ensures that the encapsulated electronic components remain safeguarded from moisture regardless of thermal variations in their operating environment.
- Adhesion: Potting compounds adhere firmly to the surfaces of electronic components and enclosures, creating a strong and durable protective layer. This adhesion prevents moisture from infiltrating through gaps between the encapsulant and the components, ensuring reliable long-term protection.
- Mechanical Protection: In addition to moisture resistance, potting compounds offer mechanical protection against vibrations, shocks, and other physical stresses that electronic components may encounter during operation or handling. This further enhances the overall durability and reliability of the encapsulated electronics.
Potting compounds shield electronic components from moisture by forming a robust physical and chemical barrier, sealing against water ingress, repelling moisture, and providing long-lasting protection even under challenging environmental conditions. Its ability to encapsulate, seal, and protect makes it an essential element in ensuring the reliability and longevity of electronic devices in various applications.
Can potting compounds withstand extreme temperatures?
Potting compounds are specially formulated materials that encapsulate electronic components, protecting them from environmental factors such as moisture, chemicals, mechanical shock, and temperature extremes. The ability of potting compounds to withstand extreme temperatures depends on several factors, including the specific formulation of the compound, the curing process, and the intended application.
Many potting compounds are designed to withstand a wide range of temperatures, from extremely low to very high, making them suitable for use in diverse environments. These compounds typically utilize thermosetting resins such as epoxy, silicone, polyurethane, or a combination thereof. Each resin type offers unique properties contributing to the compound’s ability to withstand extreme temperatures.
Epoxy-based potting compounds are known for their excellent thermal stability and resistance to high temperatures. Depending on the specific formulation, they can often withstand continuous operating temperatures ranging from -40°C to 150°C or even higher. Silicone potting compounds, on the other hand, exhibit exceptional flexibility and can maintain their properties across a broader temperature range, from as low as -50°C to over 200°C.
Polyurethane potting compounds balance thermal stability and flexibility, making them suitable for applications where a degree of mechanical stress is expected alongside temperature variations. These compounds typically have operating temperature ranges similar to or slightly narrower than epoxy-based formulations.
In addition to the base resin, additives such as fillers, plasticizers, and flame retardants can be incorporated into potting compound formulations to enhance their thermal properties further. For instance, adding ceramic fillers can improve thermal conductivity, allowing for better heat dissipation and enhancing the compound’s ability to withstand high temperatures.
The curing process also plays a crucial role in determining the temperature resistance of potting compounds. Proper curing ensures the formation of a durable and stable matrix that can maintain its integrity under temperature fluctuations.
While potting compounds can withstand extreme temperatures, the specific temperature range and performance characteristics depend on the composition, curing process, and application requirements of the compound in question.
What role does potting compound play in vibration dampening?
Potting compounds, often used in electronic and mechanical applications, play a crucial role in vibration dampening due to their unique properties and application methods. Vibration dampening is essential in various industries to reduce the detrimental effects of mechanical oscillations, such as equipment malfunction, noise generation, and structural fatigue.
One of the primary functions of potting compound in vibration dampening is its ability to encapsulate sensitive components within a rigid or semi-rigid material. The potting compound acts as a barrier by completely surrounding the components, effectively isolating them from external vibrations. This isolation prevents the transfer of mechanical energy from the surrounding environment to the components, thus reducing the amplitude of vibrations they experience.
Moreover, potting compounds exhibit viscoelastic behavior, which has viscous and elastic characteristics. This property lets them dissipate vibrational energy by converting it into heat through internal friction. As the compound deforms in response to vibrations, the power is absorbed and dissipated within the material, attenuating the vibration amplitude and mitigating its effects on enclosed components.
The choice of potting compound formulation is critical in achieving optimal vibration-dampening performance. Factors such as material stiffness, damping capacity, and adhesion properties influence the effectiveness of vibration isolation. Manufacturers often select potting compounds with specific viscoelastic properties tailored to the application’s requirements, considering factors like the frequency and magnitude of vibrations expected in the operating environment.
Additionally, potting compounds offer protection against environmental factors such as moisture, dust, and chemicals, which can potentially exacerbate vibration-induced damage to sensitive components. Potting compounds enhance their longevity and reliability by sealing the elements within an impermeable enclosure, reducing the risk of failure due to vibrational stress.
Potting compound plays a multifaceted role in vibration dampening by providing mechanical isolation, energy dissipation, and environmental protection to sensitive components. Its use contributes to the overall performance, reliability, and longevity of various electronic and mechanical systems subjected to vibrational challenges.
How does potting compound enhance the mechanical stability of electronic assemblies?
A potting compound, or encapsulant, is commonly used in electronic assemblies to enhance mechanical stability. This compound, typically made of epoxy or silicone, safeguards electronic components.
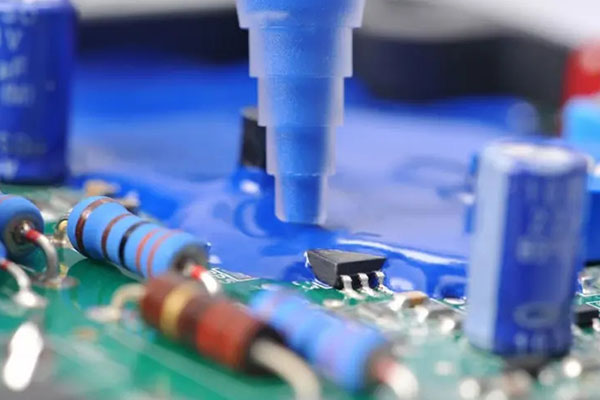
Firstly, the potting compound acts as a protective barrier, encapsulating delicate electronic components within a sturdy casing. This encapsulation shields the components from environmental factors such as moisture, dust, and chemical exposure, which can degrade performance and lead to premature failure. By forming a barrier around the components, potting compound ensures their longevity and reliability in various operating conditions.
Secondly, the potting compound provides structural reinforcement to the electronic assembly. Electronic components are often mounted on circuit boards, which may be subjected to mechanical stress during handling, transportation, or operation. Vibrations, shocks, and thermal expansion can damage solder joints or dislodge components, compromising the assembly’s integrity. However, by encasing the components in a solid, rigid material, the potting compound distributes mechanical loads evenly, reducing the risk of damage from external forces. This reinforcement improves the assembly’s durability and robustness, making it suitable for demanding applications in automotive, aerospace, and industrial automation industries.
Moreover, the potting compound offers excellent adhesion properties, ensuring a secure bond between the encapsulated components and the substrate. This adhesion prevents components from shifting or becoming loose over time, maintaining electrical connectivity and stability. Additionally, potting compounds can have thermal conductivity properties, helping dissipate heat generated by the components during operation. By efficiently transferring heat away from sensitive electronic parts, potting compound contributes to thermal management, preventing overheating and thermal-induced failures.
Potting compounds enhance the mechanical stability of electronic assemblies by providing protective encapsulation, structural reinforcement, secure adhesion, and thermal management. By mitigating environmental hazards and mechanical stresses, they ensure the reliability and longevity of electronic devices in diverse applications. Their versatile properties make them an indispensable component in modern electronics manufacturing, supporting the advancement of technology across various industries.
What are the different types of potting compounds available?
Potting compounds are materials used to encapsulate electronic components, protecting them from environmental factors such as moisture, chemicals, shock, and vibration. There are several types of potting compounds available, each with unique properties suited for specific applications:
- Epoxy Resins: Epoxy-based potting compounds offer excellent adhesion, mechanical strength, and chemical resistance. They are commonly used in applications where high performance under harsh conditions is required, such as in aerospace and automotive electronics.
- Polyurethane Resins: Polyurethane potting compounds provide flexibility, good electrical insulation properties, and resistance to thermal shock. They are often chosen for applications where components may undergo frequent thermal cycling or mechanical stress.
- Silicone Resins: Silicone potting compounds offer superior flexibility, wide temperature stability, and excellent resistance to moisture and chemicals. They are commonly used in applications where extreme temperature variations or exposure to harsh environmental conditions are expected, such as outdoor electronics or LED lighting.
- Polyester Resins: Polyester-based potting compounds are cost-effective and provide good electrical insulation properties. They are often used in less demanding applications where moderate environmental protection is sufficient.
- Acrylic Resins: Acrylic potting compounds offer fast cure times, good adhesion, and moderate chemical resistance. They are suitable for applications requiring rapid processing or where a balance between cost and performance is needed.
- Hybrid Resins: Some potting compounds combine properties of multiple resin types, offering a tailored solution for specific application requirements. For example, epoxy-silicone hybrids provide a balance between the rigidity of epoxy and the flexibility of silicone.
- Thermal Conductive Compounds: These potting materials are designed to not only protect electronic components but also to dissipate heat efficiently. They often contain fillers such as ceramics or metal oxides to enhance thermal conductivity, making them ideal for high-power electronic devices.
Choosing the right potting compound depends on factors such as the operating environment, required performance characteristics, processing requirements, and cost considerations. Conducting thorough testing and evaluation is essential to ensure the selected potting compound meets the specific needs of the application.
How is potting compound applied in electronic manufacturing processes?
Potting compound, or encapsulant, is a vital material used in electronic manufacturing to protect sensitive components from environmental factors such as moisture, vibration, shock, and corrosion. It is typically applied in a process called potting or encapsulation.
The potting process begins with selecting an appropriate potting compound based on the application’s specific requirements, including thermal conductivity, flexibility, hardness, and chemical resistance. Once the compound is chosen, the electronic components to be encapsulated are placed in a mold or fixture that holds them in the desired position.
Next, the potting compound is mixed according to the manufacturer’s instructions to achieve the proper viscosity and curing properties. This mixture is poured or dispensed into the mold, completely covering the components. Care must be taken to ensure that no air bubbles are trapped within the compound, as these can compromise the integrity of the encapsulation.
After applying the potting compound, it undergoes a curing process to harden and form a protective barrier around the electronic components. The curing time and temperature depend on the specific compound used and are critical to achieving the desired properties of the encapsulation, such as strength and durability.
Once cured, the encapsulated assembly is removed from the mold, trimmed if necessary, and inspected for defects or imperfections. Quality control measures may include visual inspection, dimensional checks, and testing for electrical performance.
Potting compounds are available in various formulations to suit different application requirements. For example, silicone-based compounds offer excellent flexibility and thermal stability, making them ideal for applications subject to wide temperature fluctuations. Conversely, epoxy-based compounds provide superior adhesion and mechanical strength, making them suitable for high-stress environments.
Potting compound plays a crucial role in electronic manufacturing by providing protection and insulation to sensitive components. The potting process involves:
- Selecting the appropriate compound.
- Encapsulating the components.
- Curing the compound.
- Conducting quality control checks to ensure a reliable and durable encapsulation.
What considerations should be made when selecting a potting compound?
Selecting the suitable potting compound for electronic manufacturing involves carefully considering various factors to ensure optimal performance and reliability. Some key considerations include:
- Environmental Conditions: Understand the operating environment in which the electronic device will be used. Consider factors such as temperature extremes, humidity levels, chemical exposure, and potential mechanical stresses. Choose a potting compound with properties that can withstand these conditions without degrading or compromising performance.
- Electrical Properties: Evaluate the electrical requirements of the application, including insulation resistance, dielectric strength, and thermal conductivity. Select a potting compound with appropriate electrical characteristics to ensure proper insulation and heat dissipation while maintaining signal integrity.
- Compatibility: Ensure compatibility between the potting compound and the materials used in the electronic assembly, including circuit boards, components, and housing materials. Incompatible materials can lead to adhesion issues, chemical reactions, or dimensional changes that affect the reliability and performance of the encapsulation.
- Curing Mechanism: Consider the curing mechanism of the potting compound, whether it is heat-cured, room-temperature-cured, or UV-curable. Choose a curing method that aligns with the manufacturing process and production requirements while achieving the desired properties of the encapsulation.
- Mechanical Properties: Assess the mechanical properties of the potting compound, such as flexibility, hardness, and impact resistance. These properties determine the ability of the encapsulation to withstand physical stresses, vibrations, and shocks encountered during operation or transportation.
- Application Method: Consider the application method for dispensing or pouring the potting compound, such as manual dispensing, automated dispensing, or casting. Select a compound compatible with the chosen application method, ensuring uniform coverage and minimal voids or air bubbles.
- Regulatory Compliance: Ensure the selected potting compound complies with relevant industry standards, safety regulations, and environmental requirements. Certifications such as UL recognition, RoHS compliance, and REACH compliance may be necessary depending on the application and market regulations.
By carefully evaluating these considerations, manufacturers can choose the most suitable potting compound to protect electronic components effectively and ensure long-term reliability in various operating environments.
Can potting compounds affect the electrical performance of electronic components?
Potting compounds, used to encapsulate electronic components, impact their electrical performance in various ways. They protect components from environmental factors such as moisture, shock, vibration, and corrosion. However, their properties can inadvertently affect the electrical characteristics of the enclosed elements.
One significant factor is the dielectric constant of the potting material. Dielectric constant measures a material’s ability to store electrical energy when subjected to an electric field. If the potting compound has a high dielectric constant, it can affect capacitance within the circuit, leading to changes in impedance, signal propagation delays, and distortion. This can be particularly critical in high-frequency applications where precise signal timing is essential.
Moreover, potting compounds may exhibit piezoelectric properties, generating an electric charge in response to mechanical stress. This piezoelectric effect can introduce unwanted electrical noise into sensitive circuits, interfering with signal integrity and potentially causing malfunctions or inaccuracies in electronic devices.
Thermal conductivity is another critical consideration. Potting materials with poor thermal conductivity may hinder heat dissipation from enclosed components, leading to elevated operating temperatures. Elevated temperatures can degrade the performance and reliability of electronic components, affecting their lifespan and causing thermal-induced failures.
Additionally, potting compounds must be chosen carefully to ensure compatibility with the enclosed components. Some compounds contain chemicals that can react with certain materials or coatings on electronic components, leading to corrosion or degradation of electrical properties over time.
Furthermore, the curing process of potting compounds can introduce stresses on delicate components, such as microcracks or mechanical distortions, which may affect electrical connections or introduce points of failure.
While potting compounds provide essential protection for electronic components, their choice and application can significantly impact electrical performance. Designers must carefully consider factors such as dielectric constant, thermal conductivity, compatibility, and curing process to mitigate any adverse effects and ensure optimal performance and reliability of electronic systems.
What are some typical applications of potting compounds in electronics?
A potting compound, also known as encapsulant or potting resin, is widely used in electronics for various applications due to its ability to protect electronic components from environmental factors and mechanical stress. Here are some typical applications:
- Waterproofing and Moisture Protection: Potting compounds are often used to encapsulate sensitive electronic components such as circuit boards, sensors, and connectors to protect them from moisture and water ingress. This is particularly important in outdoor applications, automotive electronics, and marine electronics, where exposure to moisture is a concern.
- Vibration and Shock Absorption: In environments where electronic components are subjected to vibrations or mechanical shocks, potting compounds provide a protective barrier that helps absorb these shocks, preventing damage to the components. This is crucial in aerospace, automotive, and industrial automation industries.
- Insulation: Potting compounds offer excellent electrical insulation properties, making them ideal for insulating electronic components and assemblies. This insulation helps prevent electrical shorts, improves safety, and ensures the reliable performance of electronic devices.
- Thermal Management: Some potting compounds are formulated with thermal conductive properties, allowing them to dissipate heat generated by electronic components efficiently. By encapsulating heat-generating components such as power transistors or LEDs, potting compounds help in thermal management, preventing overheating and extending the lifespan of the devices.
- Chemical Resistance: Potting compounds can protect against exposure to various chemicals and solvents. This makes them suitable for harsh chemical environments such as industrial manufacturing plants or chemical processing facilities.
- Tamper Resistance: In applications where security is a concern, potting compounds can be used to encapsulate sensitive components or circuitry, making it difficult for unauthorized individuals to tamper with or reverse-engineer electronic devices.
- Noise Reduction: Potting compounds can help dampen electromagnetic interference (EMI) and radio frequency interference (RFI), improving the overall electromagnetic compatibility (EMC) of electronic devices.
Overall, potting compounds play a crucial role in enhancing electronic devices’ reliability, durability, and performance across various industries, ensuring their functionality even in challenging operating conditions.
Is potting compound suitable for outdoor electronic devices?
A potting compound, or potting resin or encapsulant, can be a suitable option for protecting outdoor electronic devices. However, its effectiveness depends on various factors, including the specific requirements of the application, environmental conditions, and the characteristics of the potting compound itself.
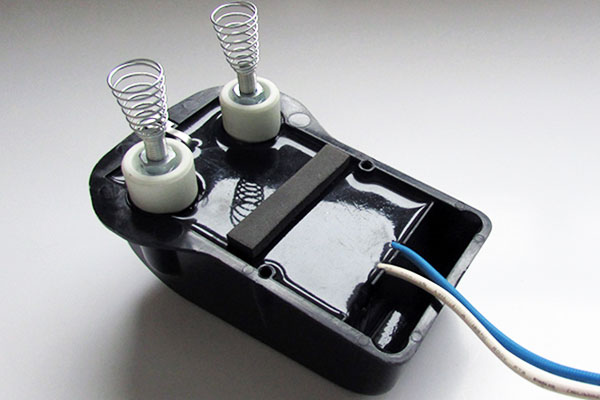
Potting compounds are typically epoxy or silicone-based materials designed to encapsulate electronic components, protecting against moisture, dust, vibrations, and other environmental hazards. Outdoor electronic devices, which are exposed to harsh conditions like rain, UV radiation, temperature fluctuations, and physical stressors, require robust protection to ensure reliable performance and longevity.
Epoxy potting compounds offer excellent mechanical strength, chemical resistance, and adhesion properties, making them suitable for outdoor applications where durability is essential. However, some epoxy formulations may be susceptible to UV degradation over time unless formulated explicitly with UV stabilizers.
Silicone potting compounds are known for their flexibility, thermal stability, and resistance to moisture and extreme temperatures. They maintain their properties over various environmental conditions, making them a popular choice for outdoor electronics. Silicone-based potting materials also offer good UV resistance, crucial for prolonged outdoor exposure.
When selecting a potting compound for outdoor electronic devices, it’s essential to consider factors such as the expected temperature range, exposure to UV radiation, mechanical stresses, and compatibility with other materials in the device. Additionally, proper application techniques, such as ensuring adequate coverage and avoiding air entrapment, are critical for maximizing the protective benefits of the potting compound.
Potting compounds protect against moisture, dust, vibrations, and other environmental hazards for outdoor electronic devices. However, consideration of formulation, application method, and compatibility is necessary to ensure optimal performance and longevity in outdoor settings.
How does potting compound contribute to the longevity of electronic assemblies?
Potting compound, a type of resin material, plays a crucial role in enhancing the longevity and durability of electronic assemblies in various ways.
- Protection from Environmental Factors: Potting compounds protect against environmental elements such as moisture, dust, chemicals, and vibrations, which can otherwise cause corrosion, short circuits, or physical damage to electronic components. Potting compounds shield the sensitive electronic parts from adverse conditions by encapsulating the sensitive electronic parts, extending their lifespan.
- Mechanical Stability: Electronic assemblies often undergo mechanical stresses during handling, transportation, or operation. Potting compounds encapsulate delicate components, providing mechanical support and stability. This reduces the risk of damage due to mechanical shocks or vibrations, ensuring the assembly’s integrity over time.
- Thermal Management: Many electronic devices generate heat during operation, which can degrade performance and reliability if not managed effectively. Potting compounds with excellent thermal conductivity can act as heat sinks, dissipating heat away from critical components and maintaining optimal operating temperatures. By preventing overheating, potting compounds help prevent thermal-induced failures and prolong the lifespan of electronic assemblies.
- Electrical Insulation: Potting compounds often have insulating properties that protect electronic components from electrical hazards such as short circuits or electric shock. By providing a dielectric barrier between conductive elements, potting compounds minimize the risk of electrical failures caused by moisture ingress or accidental contact, thereby enhancing the safety and longevity of electronic assemblies.
- Shock and Vibration Resistance: In applications where electronic assemblies are subjected to frequent shocks or vibrations, potting compounds absorb mechanical energy and distribute stresses evenly throughout the encapsulated components. This reduces the risk of mechanical fatigue or damage, ensuring reliable performance over extended periods.
Overall, using potting compounds significantly enhances the longevity of electronic assemblies by providing comprehensive protection against environmental, mechanical, thermal, and electrical stresses. By safeguarding delicate components and ensuring optimal operating conditions, potting compounds contribute to the reliability and durability of electronic devices in a wide range of applications.
Can potting compounds be removed or replaced?
Potting compounds are used in electronics and electrical applications to encapsulate components and protect them from environmental factors such as moisture, heat, and vibration. While potting compounds are designed to provide a permanent seal, there are circumstances where removal or replacement may be necessary.
Removal of potting compounds typically involves mechanical or chemical methods. Mechanical methods include chiseling, grinding, or milling away the potting material. However, this can be labor-intensive and may damage the components being encapsulated. Chemical methods involve solvents or chemical agents to dissolve or soften the potting compound for easier removal. Care must ensure that the solvent or chemical used does not damage the components.
Potting compounds may need to be replaced when the encapsulated components need to be repaired or upgraded. In such cases, the existing potting material must be removed before new material can be applied. This process requires careful consideration to avoid damaging the components during removal and to ensure proper adhesion of the new potting compound.
Advancements in potting compound technology have led to the development of some formulations designed to be more easily removable or reworkable. These formulations may include additives that facilitate disassembly or solvents that can soften the material for easier removal. However, even with these advancements, removing and replacing potting compounds can still be challenging and require specialized equipment and expertise.
While potting compounds are intended to provide a permanent seal for encapsulated components, methods are available for their removal or replacement when necessary. These methods typically involve mechanical or chemical techniques; care must be taken to avoid damaging the components. Additionally, advancements in potting compound technology have led to the development of formulations designed to be more easily removable or reworkable. However, challenges may still be encountered during the removal and replacement process.
Are there any environmental concerns associated with potting compounds?
Potting compounds, commonly used in electronics and electrical applications, can raise environmental concerns primarily due to their chemical composition and disposal methods.
- Toxicity: Many potting compounds contain hazardous chemicals such as epoxy resins, silicones, and polyurethanes. These compounds often include additives such as plasticizers, flame retardants, and curing agents, which can be toxic to humans and the environment. When disposed of improperly, these compounds can leach harmful substances into the soil and water, posing risks to wildlife and ecosystems.
- Non-Biodegradability: Most potting compounds are not biodegradable, meaning they persist in the environment for extended periods. This characteristic leads to accumulation in landfills and can contribute to soil and water pollution. As a result, there is a growing need for more environmentally friendly alternatives that degrade over time or can be recycled.
- Energy Consumption: The production process of potting compounds often involves energy-intensive procedures, contributing to greenhouse gas emissions and overall environmental impact. Extracting and processing raw materials used in these compounds can further exacerbate ecological degradation.
- Waste Generation: The manufacturing and application of potting compounds generate waste, including leftover material, packaging, and cleaning solvents. Improper disposal of this waste can lead to pollution and environmental harm if not managed effectively.
- Health Risks: Workers involved in producing and applying potting compounds may face health risks due to exposure to volatile organic compounds (VOCs) and other harmful chemicals. Proper safety measures and ventilation systems are necessary to mitigate these risks and protect human health.
To address these environmental concerns, manufacturers increasingly focus on developing greener alternatives such as bio-based resins, recyclable materials, and low-toxicity formulations. Additionally, proper waste management practices, including recycling and responsible disposal, are essential to minimize the environmental footprint associated with potting compounds. Regulatory agencies also play a crucial role in enforcing environmental standards and promoting sustainable practices within the industry.
What are some key parameters to evaluate the quality of potting compounds?
Potting compounds are crucial materials used in electronics and electrical applications to protect components from environmental factors such as moisture, dust, vibration, and thermal stress. Evaluating the quality of potting compounds involves considering several vital parameters:
- Chemical Composition: Understanding the materials used in the potting compound is essential. Typical compounds include epoxy, silicone, polyurethane, and acrylic resins. Each material has different properties, such as flexibility, adhesion, and resistance to temperature and chemicals.
- Mechanical Properties: This includes factors like hardness, flexibility, and elongation. The potting compound should provide adequate protection while allowing some flexibility to accommodate thermal expansion and contraction.
- Adhesion: The ability of the compound to adhere to various substrates such as metals, plastics, and ceramics is critical for ensuring long-term protection. Poor adhesion can lead to delamination and reduced effectiveness of the potting.
- Thermal Conductivity: Effective dissipation of heat generated by components is essential to prevent overheating and potential damage. Potting compounds with good thermal conductivity help in heat dissipation, enhancing the reliability of electronic devices.
- Electrical Insulation Properties: Potting compounds should provide insulation to prevent electrical short circuits and leakage currents. Dielectric strength, volume resistivity, and surface insulation resistance are vital parameters to evaluate.
- Chemical Resistance: The compound should resist degradation when exposed to chemicals, solvents, and other substances commonly encountered in the operating environment. This ensures long-term protection and reliability.
- Environmental Resistance: Potting compounds should withstand ecological factors such as moisture, humidity, UV exposure, and temperature fluctuations without degrading or losing their protective properties.
- Curing Time and Process: The curing time and process influence manufacturing efficiency and product turnaround time. Quick-curing compounds can reduce production time and costs.
- Cost: While ensuring quality is paramount, considering the cost-effectiveness of the potting compound is also essential for overall project feasibility.
By evaluating these parameters, manufacturers can select potting compounds that best suit the specific requirements of their applications, ensuring optimal performance, reliability, and longevity of electronic components and devices.
Can potting compounds be customized for specific applications?
Potting compounds can be customized for specific applications, offering various properties to suit multiple needs across electronics, automotive, aerospace, and more industries. Potting compound, a thermosetting polymer resin, encapsulates electronic components to protect them from environmental factors like moisture, dust, vibration, and shock. Customization involves tailoring the compound’s formulation to meet the unique requirements of a particular application.
- Chemical Composition: Potting compounds can be formulated from various materials such as epoxy, polyurethane, silicone, and others. The choice of material depends on factors like desired flexibility, temperature resistance, chemical resistance, and adhesion properties.
- Physical Properties: The physical properties of potting compounds can be adjusted to match specific application needs. This includes viscosity, cure time, hardness, thermal conductivity, and expansion coefficient. For example, applications requiring fast curing times may utilize compounds with accelerators, while those needing high thermal conductivity might incorporate thermally conductive fillers like ceramics or metallic particles.
- Environmental Considerations: Different environments demand different levels of protection. Potting compounds can be customized to resist moisture, chemicals, UV radiation, and extreme temperatures. For instance, compounds used in outdoor applications may require UV stabilizers to prevent degradation from sunlight exposure.
- Electrical Insulation Properties: In electronic applications, potting compounds must provide effective electrical insulation to prevent short circuits and electrical failures. Formulations can be tailored to achieve specific dielectric strengths, resistivity, and impedance characteristics.
- Adhesion and Compatibility: Potting compounds must adhere well to various substrates, including metals, plastics, and ceramics. Customization can ensure optimal adhesion and compatibility with specific materials commonly encountered in the application.
- Regulatory Compliance: Depending on the industry and application, potting compounds may need to meet specific regulatory standards, such as UL (Underwriters Laboratories) certification for electrical safety or RoHS (Restriction of Hazardous Substances) compliance for environmental safety. Custom formulations can be developed to meet these requirements.
Overall, the versatility of potting compounds allows for extensive customization to address the diverse needs of different applications, providing tailored solutions for reliable and durable encapsulation of electronic components.
What advancements are being made in the field of potting compounds for electronics?
Advancements in potting compounds for electronics are being driven by the demand for higher performance, miniaturization, and increased reliability in electronic devices across various industries. Potting compounds are materials encapsulating or protecting electronic components from environmental factors such as moisture, vibration, and thermal cycling. Here are some key advancements:
- Enhanced Thermal Management: With the increasing power densities in electronics, there’s a need for potting compounds with superior thermal conductivity to effectively dissipate heat. New formulations incorporate materials like graphene or boron nitride to improve thermal management, ensuring better performance and reliability, especially in high-power applications like electric vehicles and power electronics.
- Improved Flexibility and Durability: Flexible potting compounds are gaining popularity, especially in applications where components are subjected to mechanical stress or thermal expansion. Advances in polymer chemistry have led to the development of flexible formulations that maintain their properties over a wide temperature range, enhancing durability and reliability in harsh environments.
- Miniaturization and Thin Film Encapsulation: As electronic devices become smaller and more complex, there’s a growing need for potting compounds that can provide effective encapsulation without adding significant bulk. Thin film encapsulation techniques using ultra-thin layers of specialized polymers are being developed to protect delicate electronic components while maintaining compactness and lightweight design.
- Optical Transparency: In applications like LED lighting and optical sensors, where transparency is crucial for performance, there’s a demand for potting compounds that offer excellent optical clarity. Advanced formulations with optical-grade materials enable transparent encapsulation while protecting against moisture and environmental contaminants.
- Environmental Sustainability: As ecological concerns rise, there’s a shift towards eco-friendly potting compounds derived from renewable sources or recyclable materials. Manufacturers are focusing on reducing the environmental footprint of their products by using bio-based resins, solvent-free formulations, and recyclable packaging materials.
- Innovative Potting Compounds: With the advent of IoT devices and intelligent electronics, there’s a trend towards incorporating functionalities into potting compounds. Innovative potting compounds may include self-healing properties to repair minor cracks or sensors to monitor environmental conditions such as temperature and humidity, enhancing overall device performance and longevity.
Overall, advancements in potting compounds for electronics are driven by the need for improved performance, reliability, miniaturization, and environmental sustainability, making them an essential component in the development of next-generation electronic devices across various industries.
Conclusion:
In conclusion, the potting compound serves as a vital element in the protection and stability of electronic components, offering insulation, moisture resistance, and mechanical reinforcement. As technology advances, the development of innovative potting compounds will play a pivotal role in ensuring the reliability and longevity of electronic devices in various industries. Understanding potting compounds’ properties, applications, and considerations is essential for anyone designing, manufacturing, or maintaining electronic systems.
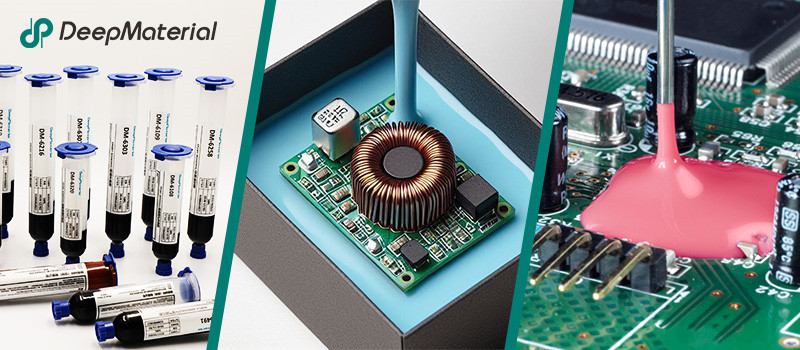
About DeepMaterial
DeepMaterial is a trusted supplier of encapsulant materials that are used in electronics manufacturing worldwide. From chip on board encapsulants such as glob top material to conformal coatings, underfills, low pressure molding, and potting solutions, DeepMaterial offers a full range of circuit board protection materials that effectively protect circuit boards while help reduce costs. More…Deepmaterial is a the manufacturer of epoxy adhesives including hardeners, metalbond, and metal filled resins. Structural, toughened medium viscosity, and non-sag adhesives are also offered. Some adhesives are resistant to thermal shock, chemical, vibration dampening, and impact. Suitable for metals, plastics, wood, and ceramics. Serves electronics, aerospace, automotive, tooling, marine, and construction industries. REACH and RoHS compliant. FDA approved. UL listed. Meets military specifications. We are the one of best adhesive manufacturers in China.
Blogs & News
Potting compounds are at the frontline of electronics assembly, delivering effective protection in challenging environmental conditions while improving mechanical strength and offering high electric insulation. Used within a variety of industries, electrical potting compounds are found within a broad range of consumer electronics, as well as used in applications across the automotive, aerospace, and other industries where electronic assemblies are prevalent.
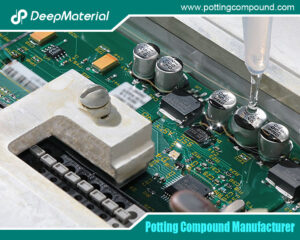
Silicone Potting Compound for Electronics
Silicone Potting Compound for Electronics In the rapidly evolving world of electronics, ensuring the reliability, durability, and performance of electronic components is paramount. One critical
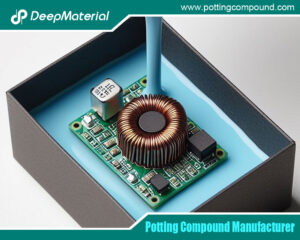
Potting Compound vs. Epoxy: A Comprehensive Comparison
Potting Compound vs. Epoxy: A Comprehensive Comparison In the world of electronics, manufacturing, and material encapsulation, two terms frequently come up: potting compounds and epoxy.
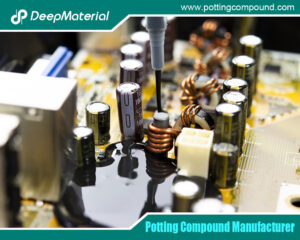
Potting Compound for PCB
Potting Compound for PCB A potting compound is a liquid or semi-liquid material that is poured or injected over a PCB or electronic assembly, then
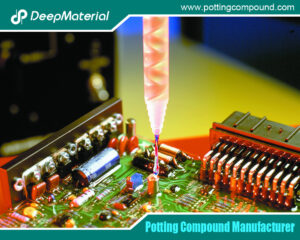
In – depth Analysis of the Curing Characteristics of Electronic Potting Compounds
In – depth Analysis of the Curing Characteristics of Electronic Potting Compounds Electronic potting compounds play a vital role in the electronics industry. They can
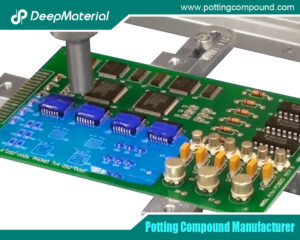
A Comprehensive Analysis of the Environmental Performance of Encapsulating Materials: From Regulations to Practices
A Comprehensive Analysis of the Environmental Performance of Encapsulating Materials: From Regulations to Practices In modern industrial manufacturing, encapsulating materials are widely used in numerous

A Comprehensive Analysis of PCB Encapsulation Quality Inspection: Innovative Application of Non-Destructive Testing Technologies
A Comprehensive Analysis of PCB Encapsulation Quality Inspection: Innovative Application of Non-Destructive Testing Technologies In the field of electronic manufacturing, the encapsulation process of printed