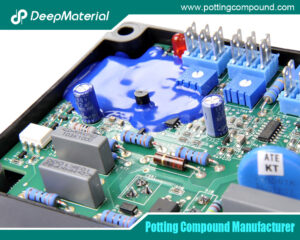
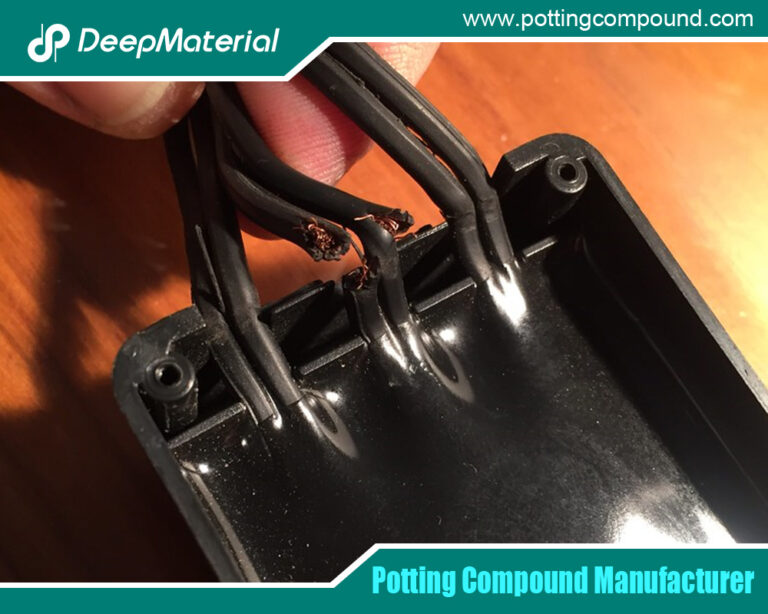
Understanding UV Cure Conformal Coating: A Comprehensive Guide
- Electronic Potting Material Manufacturer
- December 4, 2024
- Acrylic Conformal Coating, Connector Potting Compound, Electronic Conformal Coating, electronic potting compound, Industrial Conformal Coating, LED Potting Compound, pcb conformal coating, PCB Potting Compound, polyurethane potting compound, Silicone Conformal Coating, Urethane Conformal Coating, UV Cure Conformal Coating, UV cure conformal coating china hotsale, UV cure conformal coating china OEM, UV cure conformal coating china wholesale, UV cure conformal coating factory, UV cure conformal coating factory hotsale, UV cure conformal coating factory OEM, UV cure conformal coating factory wholesale, UV cure conformal coating manufacturer, UV cure conformal coating market, UV cure conformal coating supplier, Waterproof Conformal Coating, waterproof potting compound
Understanding UV Cure Conformal Coating: A Comprehensive Guide
Protecting delicate components from environmental factors in electronics manufacturing ensures longevity and reliability. One effective solution that has gained prominence is UV cure conformal coating. This innovative coating method provides a robust protective layer that safeguards electronic assemblies against moisture, dust, chemicals, and other potential hazards. This article will delve into the intricacies of UV cure conformal coating, its benefits, applications, and best practices for implementation.
What is UV Cure Conformal Coating?
UV cure conformal coating is a specialized protective layer applied to electronic circuits and components. It is formulated to provide a thin, transparent, and flexible barrier that conforms to the shape of the underlying surfaces. The unique aspect of this coating is that it cures or hardens when exposed to ultraviolet (UV) light, enabling rapid processing and efficient production cycles.
Key Features of UV Cure Conformal Coating
- Fast Curing Time:The use of UV light allows for immediate hardening, reducing downtime in manufacturing.
- Excellent Adhesion: Provides strong adherence to various substrates, including PCBs (Printed Circuit Boards) and metal surfaces.
- Chemical Resistance:Protects against various chemicals, solvents, and oils.
- Moisture Barrier: Shields electronic components from moisture, preventing corrosion and damage.
- Thermal Stability:Maintains integrity and performance under varying temperatures.
Advantages of UV Cure Conformal Coating
Enhanced Protection
UV cure conformal coatings offer superior protection against:
- Moisture:Prevents water ingress that can lead to short circuits and corrosion.
- Dust and Dirt:Acts as a barrier against particulate contamination.
- Chemicals:Protects against cleaning agents and other harmful substances.
Improved Efficiency
The rapid curing process enhances manufacturing efficiency:
- Shorter Production Times:UV curing drastically reduces drying times compared to traditional coatings.
- Less Waste:Precision application techniques minimize excess material usage.
Versatility
These coatings can be used across a wide range of applications:
- Consumer Electronics: Smartphones, tablets, and wearables.
- Industrial Equipment:Robotics, sensors, and control systems.
- Automotive: Engine control units and electronic assemblies.
Environmentally Friendly
- Low VOC Emissions:Many UV cure coatings have low volatile organic compound emissions, making them more environmentally friendly than traditional coatings.
Applications of UV Cure Conformal Coating
Consumer Electronics
In consumer electronics, UV cure conformal coatings are widely used to protect delicate components from moisture and contaminants, ensuring durability and reliability.
- Smartphones and Tablets:Shielding sensitive internal parts from water damage.
- Wearable Devices: Protecting against sweat and moisture.
Automotive Industry
UV cure conformal coatings have become essential with the rise of electronic vehicle components.
- Engine Control Units:Protecting sensitive circuitry from environmental exposure.
- Sensors:Ensuring reliable performance in harsh conditions.
Industrial Applications
In industrial settings, conformal coatings are critical for safeguarding equipment that operates in challenging environments.
- Robotics: Protecting internal components from dust and moisture.
- Control Systems:Ensuring longevity and reliability in harsh conditions.
Application Techniques for UV Cure Conformal Coating
Spraying
- Overview:This method involves spraying the coating onto the PCB or component.
- Benefits:Allows for even coverage and is suitable for complex shapes.
Dipping
- Overview:The component is submerged in a tank containing the coating material.
- Benefits:Ensures complete coverage, especially for intricate designs.
Brush Application
- Overview:Hand application using a brush for precision.
- Benefits:Ideal for touch-ups and small-scale applications.
Selective Coating
- Overview:Automated processes apply the coating only where needed, avoiding excess.
- Benefits:Reduces material waste and ensures targeted protection.
Best Practices for UV Cure Conformal Coating
Surface Preparation
- Cleaning: Ensure surfaces are free from dust, grease, and oils.
- Drying:Components must be thoroughly dried to prevent trapping moisture under the coating.
Proper Application
- Consistency:Aim for an even layer to avoid uneven curing or protection.
- Thickness: Adhere to recommended thickness guidelines to ensure adequate protection.
Curing Process
- UV Exposure:Ensure all areas receive adequate UV exposure for complete curing.
- Timing:Follow manufacturer specifications for curing times to achieve optimal results.
Quality Control
- Inspection: Regularly inspect coated components for defects or uneven coverage.
- Testing:Conduct performance tests to validate the effectiveness of the coating.
Challenges and Considerations
UV Light Penetration
- Depth of Cure:The thickness of the coating can impact the curing process; deeper layers may not cure adequately.
- Shadows:Areas not receiving direct UV light may remain uncured, necessitating careful positioning during curing.
Material Compatibility
- Substrate Interaction:Ensure compatibility of the conformal coating with the underlying materials to prevent issues like delamination.
- Chemical Resistance:Choose a formulation that can withstand the specific chemicals it will encounter in its environment.
Cost Factors
- Initial Investment:UV cure systems may require a higher upfront investment than traditional coatings.
- Long-Term Savings:Despite the initial costs, the efficiency and durability can result in lower overall production costs.
Future Trends in UV Cure Conformal Coating
As technology advances, the field of UV cure conformal coating is evolving to meet the changing demands of various industries. Several emerging trends are likely to shape the future of this protective technology.
Increased Automation
- Automation in Application: More manufacturers are adopting automated spraying and selective coating systems, which enhance precision and reduce labor costs.
- Integration with Manufacturing Lines:UV cure processes are increasingly being integrated into automated production lines, streamlining workflows.
Advancements in Coating Formulations
- New Material Developments:Ongoing research is focused on creating coatings with improved chemical resistance, flexibility, and thermal stability.
- Nanotechnology:Incorporating nanomaterials is expected to enhance the protective qualities of conformal coatings, offering better performance in extreme conditions.
Expansion in Industry Applications
- Internet of Things (IoT):As IoT devices proliferate, the demand for reliable protective coatings that safeguard sensitive electronics will grow.
- Medical Devices: The medical industry is beginning to recognize the benefits of UV cure coatings for devices that must withstand sterilization and harsh cleaning processes.
Environmental Sustainability
- Low VOC Options:There is a growing demand for eco-friendly coating solutions with lower volatile organic compound emissions.
- Recyclable Materials:Manufacturers are exploring using recyclable or bio-based materials in conformal coatings, which aligns with global sustainability goals.
Enhanced Performance Testing
- More Rigorous Testing Protocols: As the importance of reliable electronic devices increases, testing methods for conformal coatings are becoming more sophisticated.
- Real-World Simulations:Companies are investing in advanced testing facilities that simulate real-world environmental conditions to assess coating performance more accurately.
Customization and Tailored Solutions
- Tailored Formulations: Manufacturers are beginning to offer customized conformal coatings designed to meet specific application requirements.
- Client-Specific Solutions:Increased collaboration with clients to develop coatings that address their products’ unique environmental challenges.
Conclusion
UV cure conformal coating represents a significant advancement in the protection of electronic components, offering a combination of rapid curing, excellent adhesion, and robust environmental resistance. As technology evolves, the importance of protecting sensitive electronics from harsh conditions will only grow. By understanding the advantages, applications, and best practices associated with UV cure conformal coating, manufacturers can enhance the reliability and longevity of their products. As industries increasingly adopt this innovative coating technology, we expect improved performance and durability across various electronic devices.
For more about understanding UV cure conformal coating: a comprehensive guide, you can pay a visit to DeepMaterial at https://www.pottingcompound.com/ for more info.
Recent Posts
- Influence of Encapsulation Thickness on the Heat Dissipation Performance and Electrical Insulation Performance of PCB
- Causes and Avoidance Methods of Bubble Generation in the Potting Process
- Technical Details on Controlling Parameters such as Temperature, Pressure, and Speed in the Potting Process to Ensure Potting Quality
- A Comprehensive Analysis of PCB Pretreatment Before Potting Process: A Crucial Link to Ensure the Performance and Reliability of Electronic Devices
- A Comprehensive Analysis of the Performance Differences of Epoxy Resin, Silicone Rubber and Polyurethane Encapsulation Materials
- How to Select Suitable Potting Materials for PCB According to the Working Environment
- What is PCB Potting
- The Evolution of Smart Watch Assembly Adhesive: A Key Component in Modern Wearable Technology
- Laptop Tablet Assembly Adhesive: The Key to Durable and Reliable Device Construction
- Power Bank Assembly Adhesive: The Essential Component for Building Durable Power Banks