Waterproof Conformal Coating
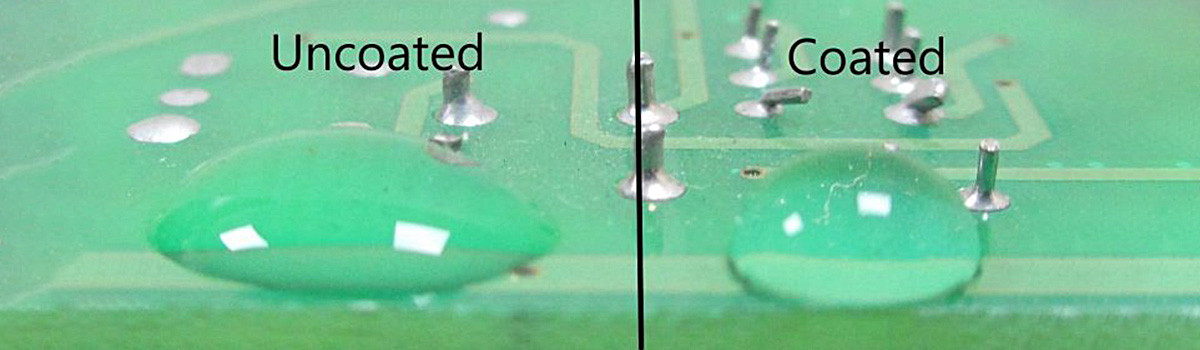
Waterproof conformal coatings protect electronic components from environmental hazards such as moisture, dust, chemicals, and temperature variations. These coatings are designed to provide a barrier against these elements, safeguarding delicate electronics from corrosion, short circuits, and other forms of damage. As technology advances and electronic devices become more ubiquitous, reliable waterproof conformal coatings are becoming increasingly vital across various industries, including automotive, aerospace, consumer electronics, and more. In this category, we delve into waterproof conformal coatings, exploring their features, applications, benefits, and the latest advancements in the field.
Table of Contents
ToggleAbout Waterproof Conformal Coating:
What is the waterproof conformal coating?
Waterproof conformal coating is a specialized material used in electronics manufacturing and maintenance to protect printed circuit boards (PCBs) and electronic components from environmental factors such as moisture, dust, chemicals, and temperature extremes. It is applied as a thin layer over the surface of electronic assemblies to create a protective barrier, conforming to the contours of the components and PCB.
The primary function of waterproof conformal coating is to prevent moisture and other contaminants from infiltrating electronic devices, which can cause corrosion, short circuits, and malfunction. This coating is essential for electronics used in harsh environments, such as outdoor equipment, automotive electronics, aerospace systems, and marine applications.
The coating material can vary, including acrylics, silicones, polyurethanes, and epoxies. Each type offers unique properties such as flexibility, chemical resistance, thermal stability, and ease of application. Acrylics, for example, are known for their transparency and fast drying time, while silicones provide excellent moisture protection and thermal stability. Polyurethanes offer good chemical resistance, and epoxies provide robust protection against mechanical stress.
Application methods for waterproof conformal coating include spray, brush, dip, and selective coating. The chosen method depends on factors such as the coating material type, the PCB assembly’s complexity, and production requirements.
Once applied, the conformal coating forms a protective layer that seals the electronic components and PCB against moisture ingress. It also provides insulation from dust and other contaminants, improving the reliability and longevity of electronic devices.
Despite its protective benefits, the waterproof conformal coating must be applied carefully to avoid issues such as uneven coverage, air entrapment, and coating bridging between components, which can compromise the effectiveness of the coating. Proper curing and drying processes ensure the coating adheres securely to the surface and achieves its intended protective properties.
Waterproof conformal coating is a critical element in electronics manufacturing. It offers vital protection against environmental factors to enhance the reliability and durability of electronic devices in a wide range of applications.
How does waterproof conformal coating protect electronic components?
Waterproof conformal coating is a protective layer applied to electronic components to safeguard them against damage from moisture, dust, chemicals, and other environmental factors. This coating, typically made of materials like silicone, acrylic, or urethane, serves several crucial functions in ensuring the longevity and reliability of electronic devices.
First and foremost, waterproof conformal coating is a barrier against moisture ingress. Moisture, whether from humidity in the air or exposure to liquids, can corrode metal components, cause short circuits, and degrade solder joints. By encapsulating the electronic components with a waterproof layer, the coating prevents water molecules from reaching sensitive areas, thereby shielding them from harm.
Furthermore, this protective coating also guards against dust and particulate matter, which could interfere with the operation of electronic circuits. Dust accumulation can lead to overheating, reduced performance, or even failure of the device. By creating a sealed barrier over the components, waterproof conformal coating mitigates the risk of dust infiltration, maintaining optimal functioning over time.
Moreover, waterproof conformal coating enhances the resistance of electronic components to various chemicals and contaminants in the environment. Whether it’s exposure to oils, solvents, or corrosive substances, the coating acts as a shield, preventing these materials from interacting with the delicate electronics underneath.
Additionally, conformal coatings can offer insulation properties, protecting against electrical leakage and short circuits. This insulation is particularly crucial in environments where electrical conductivity could pose a safety hazard or where the device operates near conductive materials.
Waterproof conformal coating provides a multi-layered defense mechanism for electronic components. It forms a protective barrier against moisture, dust, chemicals, and electrical interference, extending the lifespan and reliability of electronic devices in various environments and applications. This coating is essential for ensuring the durability and performance of electronics, especially in challenging operating conditions.
What are the different types of waterproof conformal coatings available?
Waterproof conformal coatings protect electronic components from moisture, dust, chemicals, and other environmental factors leading to corrosion, short circuits, and overall device failure. Several types of conformal coatings offer varying levels of protection and application methods:
- Acrylic Conformal Coatings: Acrylic coatings provide excellent moisture resistance and are easy to apply by spray, brush, or dip methods. They offer good dielectric properties and transparency, making them suitable for PCBs and LED assemblies. Acrylic coatings can withstand various temperatures and provide decent chemical resistance.
- Silicone Conformal Coatings: Silicone coatings offer superior protection against moisture, extreme temperatures, and chemicals. They have excellent flexibility and adhesion properties, making them ideal for components subjected to thermal cycling and mechanical stress. Silicone coatings are often used in harsh environments like automotive, aerospace, and marine applications.
- Urethane Conformal Coatings: Urethane coatings provide robust protection against moisture, chemicals, and abrasion. They offer excellent resistance to solvents and fuels, making them suitable for military and automotive electronics. Urethane coatings provide good dielectric properties and are available in various formulations to meet specific application requirements.
- Epoxy Conformal Coatings: Epoxy coatings offer high chemical and solvent resistance and excellent adhesion to multiple substrates. They provide a hard, durable finish and are well-suited for applications where mechanical protection is crucial. Epoxy coatings are commonly used in industrial, medical, and consumer electronics.
- Parylene Conformal Coatings: Parylene coatings offer ultra-thin, pinhole-free protection with superior chemical and moisture resistance. They provide excellent dielectric properties and are biocompatible, making them suitable for medical implants and other sensitive applications. Parylene coatings are deposited through vapor deposition, ensuring uniform coverage even in complex geometries.
- Polyurethane Conformal Coatings: Polyurethane coatings balance flexibility, moisture, and chemical resistance. They provide reasonable protection against abrasion and mechanical stress, making them suitable for applications subjected to handling and vibration. Polyurethane coatings are available in solvent-based or UV-curable formulations, offering versatility in application methods.
Each type of conformal coating has advantages and limitations, and selection depends on factors such as the application environment, required level of protection, ease of application, and regulatory compliance. Proper selection and application of conformal coatings are essential to ensuring the long-term reliability of electronic assemblies in demanding operating conditions.
What industries commonly use waterproof conformal coatings?
Waterproof conformal coatings have extensive applications across various industries, where protecting electronic components from moisture, dust, chemicals, and other environmental factors is crucial. These coatings provide a thin protective layer that adheres to the contours of electronic assemblies, sealing them against potentially damaging elements. Here are some industries commonly using waterproof conformal coatings:
- Electronics and Electrical Industry: The electronics sector is one of the primary users of waterproof conformal coatings. Printed circuit boards (PCBs), sensors, and other electronic components are vulnerable to moisture and corrosion. Conformal coatings safeguard these components, ensuring reliable performance in applications ranging from consumer electronics to industrial automation.
- Automotive Industry: As automotive technology advances, vehicles incorporate more electronics for functionalities like infotainment systems, engine control units, and safety features. Waterproof conformal coatings protect these sensitive electronics from the harsh conditions encountered on the road, such as temperature variations, humidity, and exposure to road salts.
- Aerospace and Defense: In aerospace and defense applications, electronics face extreme conditions, including high altitude, temperature variations, and exposure to moisture. Conformal coatings protect avionics, communication systems, and other electronic equipment in aircraft, satellites, and military hardware.
- Medical Devices: Medical devices often contain sensitive electronic components that must operate reliably in challenging environments such as hospitals or even within the human body. Waterproof conformal coatings help medical electronics withstand sterilization procedures, bodily fluids, and environmental contaminants, ensuring patient safety and device reliability.
- Industrial Equipment: Machinery used in industrial environments is susceptible to moisture, dust, and chemical exposure, which can lead to corrosion and malfunctions. Conformal coatings extend the lifespan of electronic components in industrial equipment such as sensors, controllers, and motors, reducing maintenance costs and downtime.
- Telecommunications: Telecommunication infrastructure, including base stations, antennas, and networking equipment, is exposed to outdoor conditions where moisture and temperature variations can degrade electronic performance. Waterproof conformal coatings protect sensitive components, ensuring uninterrupted communication services.
- Marine Applications: Electronics used in marine environments face constant exposure to saltwater, humidity, and corrosive elements. Conformal coatings are vital for marine electronics, including navigation systems, sonar equipment, and communication devices, to withstand these harsh conditions and maintain functionality.
Waterproof conformal coatings protect electronic components across various industries, ensuring reliability, longevity, and performance in challenging environments.
What are the primary functions of conformal coatings?
Conformal coatings protect electronic components and assemblies from various environmental hazards, ensuring reliability and longevity. These coatings are applied thinly and uniformly over the surface of printed circuit boards (PCBs) and other electronic devices, forming a protective layer that conforms precisely to the contours of the substrate. The primary functions of conformal coatings can be categorized as follows:
- Environmental Protection: One of the primary functions of conformal coatings is to shield electronic components from environmental elements such as moisture, dust, chemicals, and pollutants. By creating a barrier between the sensitive electronic parts and the external environment, conformal coatings prevent corrosion, oxidation, and other forms of degradation that can compromise the performance and reliability of the devices.
- Insulation: Conformal coatings act as insulators, providing electrical insulation between adjacent conductive traces and components on the PCB. This insulation helps prevent short circuits and electrical leakage due to environmental contaminants or moisture ingress. By maintaining the integrity of electrical pathways, conformal coatings contribute to electronic systems’ overall reliability and safety.
- Mechanical Protection: In addition to environmental and electrical protection, conformal coatings offer mechanical protection to electronic assemblies. They can help prevent physical damage caused by vibration, shock, abrasion, and mechanical stress during handling, shipping, or operation. By encapsulating delicate components and securing them in place, conformal coatings enhance the mechanical robustness of electronic devices, reducing the risk of mechanical failure.
- Thermal Management: Some conformal coatings have thermal management properties, which help dissipate heat generated by electronic components during operation. By facilitating heat transfer away from critical components, these coatings aid in maintaining optimal operating temperatures, preventing overheating, and prolonging the lifespan of electronic devices.
- UV Resistance and Dielectric Strength: Certain conformal coatings are formulated to resist ultraviolet (UV) radiation, which can cause the degradation of unprotected electronic materials over time. These coatings exhibit high dielectric strength, ensuring reliable insulation and electrical performance even under challenging environmental conditions.
Conformal coatings serve multiple essential functions in electronic applications, including environmental protection, electrical insulation, mechanical reinforcement, thermal management, UV resistance, and dielectric strength. By effectively addressing these aspects, they contribute to the reliability, durability, and performance of electronic devices in various industries.
How is a waterproof conformal coating applied to electronic components?
Waterproof conformal coating is a protective layer applied to electronic components to safeguard them against moisture, dust, chemicals, and other environmental factors that could lead to malfunctions or damage. The application process involves several key steps to ensure adequate protection:
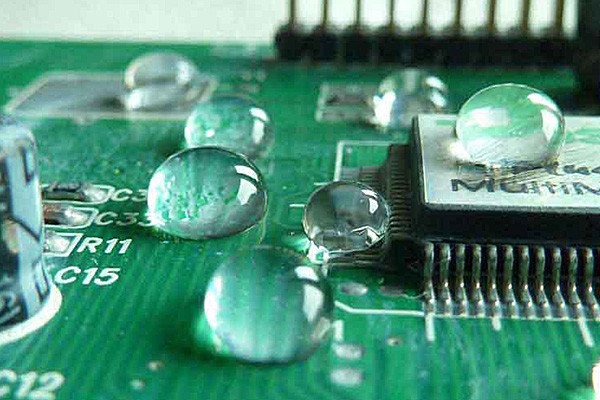
- Surface Preparation: Before applying the coating, the surface of the electronic components must be thoroughly cleaned to remove any contaminants such as dust, grease, or residues. This typically uses solvents, brushes, or specialized cleaning solutions to ensure maximum coating adhesion.
- Masking: Certain areas of the electronic components, such as connectors or sensitive components, may need to be masked off to prevent the conformal coating from interfering with their functionality. Masking tape or liquid masking materials are often used for this purpose.
- Application Method: Several methods exist for applying conformal coating, including spraying, dipping, brushing, and selective coating. The choice of method depends on factors such as the type of coating, the complexity of the components, and the desired level of coverage.
- Spraying: This method involves using a spray gun or automated spraying equipment to evenly coat the surface of the components with the conformal coating. It allows for fast and efficient application and covers large areas quickly.
- Dipping: Components can be immersed in a tank of conformal coating material, allowing the coating to flow over and around them. Dipping ensures complete coverage of all surfaces, including hard-to-reach areas, but may require longer drying times.
- Brushing: Conformal coating can be applied manually for smaller-scale or intricate components using brushes or applicators. This method provides precise control over the application and allows for targeted coverage.
- Curing: Once the coating is applied, it must cure or dry properly to form a protective barrier. Curing methods vary depending on the type of coating but may involve air drying, heat curing, UV curing, or chemical curing.
- Inspection and Testing: After the coating has cured, the components undergo inspection to ensure uniform coverage and quality. Various tests, such as moisture resistance testing and electrical testing, may be conducted to verify the coating’s effectiveness.
Applying waterproof conformal coating is a critical step in the manufacturing process of electronic components, helping to enhance their reliability and longevity in challenging environments.
What are the fundamental properties to consider when selecting a waterproof conformal coating?
Selecting a suitable waterproof conformal coating protects electronic components from environmental factors like moisture, dust, chemicals, and temperature variations. Several vital properties should be considered during the selection process:
- Waterproofing Ability: The primary purpose of a conformal coating is to provide waterproofing. Look for coatings that highly resist water ingress, preventing moisture from reaching sensitive electronic parts. Coatings should have low water absorption rates and maintain waterproofing integrity over time.
- Chemical Resistance: Electronic components may be exposed to various chemicals in their operating environments. Choose a conformal coating resistant to chemicals such as solvents, oils, fuels, and cleaning agents. Chemical resistance ensures the coating remains effective and maintains its protective properties.
- Adhesion Strength: The coating must adhere firmly to the substrate surface to provide adequate protection. Opt for coatings with solid adhesion properties to ensure they remain in place even under mechanical stress, thermal cycling, or vibration.
- Flexibility: Electronic assemblies often experience thermal expansion and contraction during operation. Flexible coatings can accommodate these movements without cracking or delaminating, maintaining a continuous protective barrier.
- Dielectric Properties: Conformal coatings should maintain electrical insulation properties to prevent short circuits and electrical malfunctions. Ensure the chosen coating maintains its dielectric strength over various operating conditions.
- Temperature Stability: Electronic devices may operate in environments with extreme temperatures. Select coatings that withstand high and low-temperature extremes without degradation, ensuring continued protection under all operating conditions.
- UV Resistance: If electronic components are exposed to sunlight or UV radiation, UV-resistant coatings are essential to prevent degradation and maintain the integrity of the protective layer.
- Ease of Application and Rework: Consider coatings that are easy to apply uniformly and can be reworked. Opt for formulations compatible with your application method (spraying, dipping, brushing) and curing process.
- Compliance and Certification: Depending on the industry and application, ensure the selected conformal coating meets relevant standards and certifications for safety, reliability, and environmental compliance.
By carefully evaluating these fundamental properties, you can select a waterproof conformal coating that protects your electronic assemblies in their specific operating environments.
What are the environmental conditions that waterproof conformal coatings protect against?
Waterproof conformal coatings protect electronic components, shielding them from various environmental conditions that could compromise their functionality or longevity. These coatings are designed to withstand a wide range of environmental stressors, ensuring the reliability and durability of sensitive electronics. Below are some critical ecological conditions that waterproof conformal coatings protect against:
- Moisture and Humidity: Waterproof conformal coatings are primarily formulated to prevent moisture ingress into electronic devices. They create a barrier that repels water and prevents it from reaching the sensitive internal components. This protection is essential in environments with high humidity levels or exposure to water, such as outdoor applications or industrial settings.
- Chemical Exposure: Many electronic devices encounter chemicals or solvents during operation or maintenance. Conformal coatings resist various chemicals, including oils, fuels, cleaning agents, and corrosive substances. This safeguard ensures that the components remain unaffected by chemical exposure, reducing the risk of corrosion or damage.
- Dust and Debris: Electronic equipment deployed in industrial or outdoor environments is susceptible to the accumulation of dust, dirt, and other debris, which can interfere with their operation. Waterproof conformal coatings create a barrier that prevents particles from settling on circuit boards or electronic components, maintaining optimal performance and reliability over time.
- Temperature Extremes: Electronic devices may be subjected to extreme temperatures, either hot or cold, depending on their operating environment. Conformal coatings offer thermal stability, protecting components from thermal shock, expansion, or contraction due to temperature fluctuations. This thermal protection helps maintain consistent performance and extends the lifespan of the electronics.
- Mechanical Stress: Vibrations, shocks, and mechanical impacts can damage electronic components, leading to malfunctions or failure. Waterproof conformal coatings protect against mechanical stressors, dampening vibrations, and absorbing impacts to prevent damage to the delicate internal circuitry.
Waterproof conformal coatings play a crucial role in safeguarding electronic devices against moisture, chemicals, dust, temperature extremes, and mechanical stress. By effectively mitigating these environmental hazards, they help ensure the reliability, longevity, and performance of electronic systems in various applications and industries.
Can waterproof conformal coatings withstand extreme temperatures?
Waterproof conformal coatings protect electronic components and assemblies from environmental factors such as moisture, dust, chemicals, and temperature extremes. While these coatings can provide effective waterproofing, their ability to withstand extreme temperatures depends on several factors, including the type of coating material, application method, and the specific temperature range.
Many waterproof conformal coatings are formulated to withstand a wide range of temperatures, including both high and low extremes. Silicone-based coatings, for example, are known for their excellent temperature resistance and can typically withstand temperatures ranging from -55°C to 200°C or higher, depending on the specific formulation. Acrylic and polyurethane coatings also offer good temperature resistance but may have more limited operating ranges than silicone.
The effectiveness of a waterproof conformal coating in extreme temperatures also depends on its application method and thickness. Properly applied coatings with adequate thickness can provide better insulation and thermal protection for electronic components, enhancing their ability to withstand temperature fluctuations.
However, it’s important to note that extreme temperatures beyond the specified operating range of a conformal coating can still compromise its performance. Prolonged exposure to temperatures beyond its limits may cause the coating to degrade, become brittle, or lose its adhesion to the substrate, leaving electronic components vulnerable to environmental damage.
Specialized coatings or additional measures may be necessary to protect electronic assemblies operating in extremely high or low-temperature environments. For example, in applications where components are exposed to temperatures exceeding the capabilities of traditional conformal coatings, manufacturers may opt for ceramic-based coatings or encapsulation techniques to provide enhanced thermal protection.
While waterproof conformal coatings can offer adequate protection against moisture and environmental factors, their ability to withstand extreme temperatures depends on various factors, including the coating material, application method, and operating conditions. Proper selection and application of coatings tailored to the specific temperature requirements of the application are essential to ensure reliable performance and longevity of electronic components in challenging environments.
Are there any regulations or standards for waterproof conformal coatings?
Yes, regulations and standards govern waterproof conformal coatings, particularly in industries where electronics are exposed to harsh environments or moisture. These standards ensure the coatings protect electronic components from water damage, corrosion, and other environmental factors. Some key regulations and standards include:
- IPC Standards: The Institute for Printed Circuits (IPC) develops standards for the electronics manufacturing industry, including standards for conformal coatings. IPC-A-610 outlines acceptance criteria for electronic assemblies, including criteria for conformal coatings to ensure they meet industry standards for protection against moisture and other contaminants.
- UL Standards: Underwriters Laboratories (UL) is a global safety certification company. UL standards, such as UL 746E, provide guidelines for evaluating polymeric materials used in electrical equipment, including conformal coatings. These standards assess the material’s resistance to various environmental factors, including water and humidity.
- ASTM International Standards: ASTM International develops and publishes technical standards for various materials and products. ASTM D7866 is a standard practice for determining the resistance of coatings to water immersion, specifically designed to evaluate the water resistance of coatings such as conformal coatings.
- Military Standards (MIL): Military standards often set stringent requirements for electronic components and coatings due to the demanding environments in which military equipment operates. MIL-PRF-55342 outlines requirements for conformal coatings used in military applications, including waterproofing properties.
- IEC Standards: The International Electrotechnical Commission (IEC) develops standards for international electrical and electronic components. Standards such as IEC 61086 guide conformal coatings for printed circuit boards, including requirements for resistance to moisture and other environmental factors.
These regulations and standards ensure that conformal coatings meet specified criteria for waterproofing and protection against environmental hazards. Compliance with these standards helps manufacturers ensure the reliability and longevity of electronic products, particularly in applications where exposure to moisture is a concern. Adherence to these standards may also be necessary for regulatory approval or certification in specific industries.
What are the benefits of using waterproof conformal coatings?
Waterproof conformal coatings offer a range of benefits across various industries, particularly in electronics, aerospace, automotive, and marine applications. Here are some key advantages:
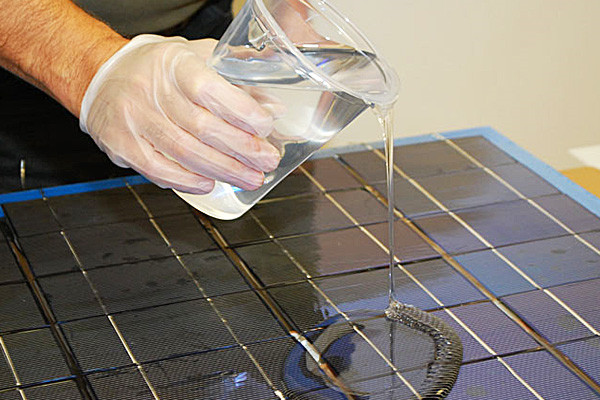
- Environmental Protection: Waterproof conformal coatings create a barrier against moisture, humidity, dust, chemicals, and other environmental factors. Sealing electronic components and circuitry prevents corrosion and damage caused by exposure to harsh conditions. This extends the lifespan of electronic devices and ensures reliable performance even in challenging environments.
- Improved Reliability: Coatings protect sensitive electronic components from moisture ingress, which can cause short circuits, electrical failures, and performance degradation. By minimizing the risk of these issues, waterproof coatings enhance the reliability and durability of electronic devices, reducing the need for costly repairs or replacements.
- Enhanced Performance: Conformal coatings can improve the electrical insulation properties of electronic assemblies, reducing the risk of electrical leakage and interference. This helps maintain signal integrity, prevent voltage breakdown, and ensure optimal performance of electronic systems, especially in high-frequency or high-voltage applications.
- Miniaturization: With the trend towards smaller and more compact electronic devices, waterproof conformal coatings enable designers to protect delicate components without adding bulk or weight. This allows for greater design flexibility and facilitates the development of compact, lightweight products for various applications.
- Ease of Application: Many waterproof conformal coatings are designed for easy application through methods such as spraying, dipping, brushing, or selective coating. This simplifies the manufacturing process and reduces production time and costs. Additionally, some coatings cure quickly at ambient temperatures, further streamlining the assembly process.
- Compliance and Certification: Waterproof conformal coatings can help electronic products meet industry standards and regulatory requirements for reliability, safety, and environmental protection. By using certified coatings, manufacturers can ensure their products comply with relevant regulations and gain customer trust and confidence.
- Versatility: Waterproof conformal coatings are available in various formulations to suit different substrates, application methods, and performance requirements. Whether silicone, acrylic, urethane, or epoxy-based coatings, there’s a solution for almost every application, providing flexibility and adaptability across diverse industries and environments.
Waterproof conformal coatings offer a comprehensive range of benefits, including environmental protection, improved reliability, enhanced performance, miniaturization, ease of application, compliance with standards, and versatility. These make them indispensable for protecting electronic components and assemblies in demanding operating conditions.
How long do waterproof conformal coatings typically last?
Waterproof conformal coatings protect electronic components from environmental factors such as moisture, dust, chemicals, and temperature extremes. Their longevity depends on various factors, including the type of coating used, application method, environmental conditions, and the quality of the coating process. Generally, waterproof conformal coatings can last from several months to several years.
One of the most commonly used waterproof conformal coatings is silicone-based. Silicone coatings provide excellent protection against moisture and offer flexibility, making them suitable for various applications. Silicone coatings can last for several years in moderate environmental conditions when applied correctly. However, exposure to harsh conditions such as extreme temperatures or chemicals can reduce their lifespan.
Another popular type of waterproof conformal coating is acrylic-based. Acrylic coatings offer good moisture resistance and are relatively easy to apply. They tend to be more cost-effective than silicone coatings but may not offer the same level of durability. Acrylic coatings typically last for several months to a few years, depending on the application and environmental conditions.
Polyurethane coatings are also used to waterproof electronic components. These coatings provide excellent protection against moisture, chemicals, and abrasion. Polyurethane coatings offer durability and can withstand harsh environmental conditions, making them suitable for outdoor applications. With proper application and maintenance, polyurethane coatings can last for several years.
The longevity of waterproof conformal coatings can be extended through proper application techniques, such as ensuring uniform coverage and adequate thickness. Regular inspections and maintenance can also help identify areas where the coating may have degraded or been damaged, allowing for timely repairs or reapplication.
The lifespan of waterproof conformal coatings varies depending on several factors. Still, with proper selection, application, and maintenance, they can provide adequate protection for electronic components for an extended period, ranging from months to several years.
What are the challenges associated with applying waterproof conformal coatings?
Applying waterproof conformal coatings presents several challenges, primarily due to the intricate nature of the coating process and the demanding environmental conditions these coatings must withstand. Here are some key challenges:
- Surface Preparation: Proper surface preparation is crucial for ensuring adhesion and effectiveness of the coating. Contaminants such as dust, oils, and residues can hinder adhesion and compromise the coating’s waterproofing properties. Achieving a clean and uniform surface often requires meticulous cleaning and possibly using chemical agents or abrasives, which can be time-consuming and costly.
- Coating Uniformity: Achieving uniform coating thickness across complex and irregular surfaces can be challenging. Inconsistencies in coating thickness may lead to areas with inadequate protection or regions prone to delamination, compromising the overall waterproofing performance.
- Compatibility: Ensuring compatibility between the conformal coating material and the substrate is essential. Some substrates may react adversely with certain coating materials, leading to issues such as poor adhesion, discoloration, or even degradation of the substrate material over time. Compatibility testing and selecting appropriate coating materials are critical steps in the coating process.
- Curing Process: Proper curing of the conformal coating is essential for achieving optimal performance. Factors such as temperature, humidity, and curing time must be carefully controlled to ensure complete curing without causing damage to the coated components. Inadequate curing can result in poor adhesion, reduced mechanical strength, and compromised waterproofing properties.
- Mechanical Stress: Conformal coatings must withstand various mechanical stresses, including thermal cycling, vibration, and physical impact, without cracking or delamination. Ensuring the durability and resilience of the coating under such conditions requires careful selection of coating materials and proper application techniques.
- Quality Control: Maintaining consistent quality across batches and ensuring compliance with industry standards and specifications is essential. Robust quality control measures, including inspection, testing, and documentation, are necessary to detect any defects or inconsistencies in the coating process and ensure the reliability of the waterproofing protection.
Addressing these challenges requires technical expertise, meticulous process control, and appropriate selection of materials and equipment. Despite the obstacles, effectively applying waterproof conformal coatings is crucial for protecting electronic components and assemblies from moisture, contaminants, and environmental hazards, ensuring reliable performance and longevity.
Are there any differences between waterproof conformal coatings and other conformal coatings?
There are differences between waterproof conformal coatings and other types of conformal coatings, primarily in their composition, properties, and intended applications. Here’s an overview of some key distinctions:
- Waterproof Properties: The primary difference lies in the waterproofing capabilities of waterproof conformal coatings. These coatings are specifically formulated to provide a high degree of protection against moisture and water ingress, making them suitable for applications exposed to harsh environmental conditions, such as outdoor electronics, marine equipment, or automotive components subject to water exposure. In contrast, other conformal coatings may offer protection against environmental contaminants like dust, chemicals, or humidity but may not provide the same level of waterproofing.
- Chemical Composition: Waterproof conformal coatings often utilize specialized formulations containing hydrophobic materials such as silicone, polyurethane, or acrylic resins. These materials form a barrier that repels water and prevents penetration into sensitive electronic components. Other types of conformal coatings may employ different chemical compositions tailored to protect against specific environmental challenges, such as thermal cycling, vibration, or corrosive chemicals.
- Flexibility and Durability: Waterproof conformal coatings typically exhibit high flexibility and durability to withstand mechanical stresses, temperature fluctuations, and other environmental factors while maintaining their waterproofing properties over time. This enhanced durability is essential for applications where components are exposed to outdoor or rugged operating conditions. In contrast, other types of conformal coatings may prioritize properties such as electrical insulation, thermal conductivity, or chemical resistance, depending on the application’s specific requirements.
- Application Method: While the application methods for waterproof conformal coatings are similar to other types of conformal coatings (e.g., spray, dip, brush, or selective coating), the specific application techniques and process parameters may vary to ensure adequate coverage and adhesion for waterproofing purposes. Additionally, post-application curing processes may be tailored to optimize the waterproofing performance of these coatings.
While waterproof conformal coatings share similarities with other types of conformal coatings in terms of application methods and protective functions, their specialized formulation and emphasis on waterproofing distinguish them as a specific category tailored for applications requiring robust protection against water and moisture ingress.
Can waterproof conformal coatings be removed or reworked?
Waterproof conformal coatings protect electronic components from environmental factors such as moisture, dust, chemicals, and temperature fluctuations. While these coatings provide excellent protection, there are circumstances where they may need to be removed or reworked. Here’s a brief overview of the processes involved:
- Chemical Stripping: Some conformal coatings can be chemically stripped using specialized solvents or strippers. These chemicals dissolve the coating, making it easier to remove from the electronic components. However, this process requires careful handling to avoid damaging the underlying circuitry or components.
- Mechanical Removal: In cases where chemical stripping is not feasible or safe, mechanical methods may be employed. This involves scraping, sanding, or grinding the coating off the surface of the electronic assembly. Mechanical removal can be more labor-intensive and carries a higher risk of damaging the components if not done carefully.
- Thermal Rework: Another method for removing conformal coatings involves thermal rework. This process uses heat to soften the coating, making it easier to peel or scrape away. Specialized equipment such as hot air pencils or infrared heaters are often used. Thermal rework can be effective for localized removal of coatings without causing damage to surrounding components.
- Recoating: After removing the old coating, the electronic assembly may require recoating to restore protection. This involves applying a new layer of conformal coating using methods such as spraying, dipping, or brushing. Proper surface preparation is essential to ensure adhesion and effectiveness of the new coating.
- Testing and Quality Control: Throughout the removal and rework process, it’s crucial to perform testing to ensure the integrity of the electronic components and the effectiveness of the new coating. This may include electrical testing, visual inspection, and environmental testing to verify that the assembly meets required standards and specifications.
While waterproof conformal coatings are designed to provide long-lasting protection, they can be removed or reworked using various methods such as chemical stripping, mechanical removal, thermal rework, and recoating. However, these processes require careful consideration and expertise to avoid damage to the electronic components and ensure the continued reliability of the assembly.
What are some standard application methods for waterproof conformal coatings?
Waterproof conformal coatings protect electronic components from moisture, dust, chemicals, and other environmental contaminants. These coatings are often applied to printed circuit boards (PCBs), electronic assemblies, and other sensitive components to ensure reliability and longevity. Several standard application methods are utilized to apply these coatings effectively:
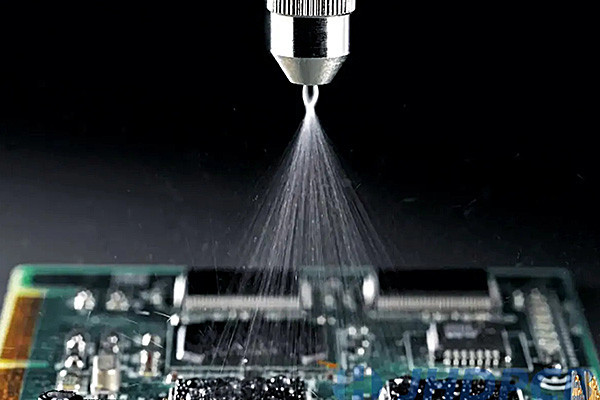
- Dipping: Dipping is one of the most common methods for applying conformal coatings. During this process, the electronic components are submerged in a tank containing the coating material. The coating material adheres to the surface of the components, forming a protective layer. Dipping is suitable for simultaneously coating large batches of components, making it a cost-effective and efficient method.
- Spraying: Spraying involves using specialized equipment to spray the coating material onto the surface of the electronic components. This method offers more control over the thickness and coverage of the coating compared to dipping. It is beneficial for coating complex shapes or assemblies where dipping may not be practical.
- Brushing: Brushing is a manual method where the coating material is applied using brushes or applicators. This method is suitable for coating specific areas or components that cannot be dipped or sprayed easily. However, it is more labor-intensive and may not provide a coating that is as uniform as dipping or spraying.
- Selective Coating: Selective coating involves applying the conformal coating material only to specific areas of the electronic components, leaving other regions uncoated. This method is commonly used to protect sensitive areas while avoiding coating areas such as connectors or heat sinks where the coating could interfere with functionality.
- Curing: Once applied, the conformal coating material must be cured to form a durable protective layer. Curing can be achieved through various methods, such as air drying, heat curing, or UV curing, depending on the type of coating material used.
Each application method has its advantages and limitations, and the choice of method depends on factors such as the type of components being coated, production volume, cost considerations, and desired coating properties. Manufacturers often employ a combination of these methods to achieve the desired level of protection for their electronic products.
Are there any advancements or innovations in waterproof conformal coating technology?
There have been notable advancements and innovations in waterproof conformal coating technology, mainly driven by the demand for enhanced protection of electronic devices in various industries, including automotive, aerospace, consumer electronics, and more.
One significant advancement lies in the development of nano-coatings. These coatings utilize nanotechnology to create ultra-thin layers that provide superior waterproofing while maintaining flexibility and transparency. These coatings can achieve excellent coverage even in intricate electronic assemblies without adding bulk or compromising performance by leveraging nanomaterials such as nanoparticles or nanocomposites.
Another innovation is the emergence of self-healing coatings. These coatings can automatically repair minor damages or breaches when exposed to certain stimuli such as heat, light, or moisture. This self-healing property prolongs the lifespan of the coating and ensures continuous protection against water ingress, even in harsh environments where physical damage is likely to occur.
Furthermore, the development of environmentally friendly and sustainable coatings is gaining momentum. Manufacturers are exploring alternative materials derived from renewable sources or employing green chemistry principles to formulate coatings that meet regulatory requirements while minimizing environmental impact throughout their lifecycle.
In addition to material advancements, there have been improvements in application techniques and equipment. Automated coating processes such as selective coating robots or spray systems equipped with precision control mechanisms enable uniform and efficient coating application, ensuring consistent coverage and minimizing waste.
Moreover, advancements in testing and inspection technologies play a crucial role in ensuring the reliability and effectiveness of waterproof conformal coatings. Techniques such as accelerated aging tests, impedance spectroscopy, and infrared imaging allow for thorough evaluation of coating performance under various conditions, facilitating quality control and optimization of coating formulations.
Continuous innovation in waterproof conformal coating technology enhances the durability and reliability of electronic devices and contributes to the advancement of industries reliant on such technologies, fostering progress and innovation in diverse fields.
How do you test the effectiveness of waterproof conformal coatings?
Testing the effectiveness of waterproof conformal coatings is crucial to ensure their reliability in protecting electronic components from moisture, chemicals, and other environmental factors. Several methods are employed to evaluate their effectiveness:
- Water Immersion Test: This involves submerging coated electronic assemblies in water for a specified duration while monitoring for any signs of water ingress. After immersion, components are inspected for signs of moisture penetration, such as corrosion or electrical malfunction.
- Humidity Testing: Coated assemblies are subjected to high-humidity environments, often using environmental chambers set to specific humidity levels. This test assesses the coating’s ability to resist moisture absorption over time.
- Thermal Cycling Test: Thermal cycling involves subjecting the coated assemblies to alternating extreme temperatures. This test evaluates the coating’s ability to withstand temperature variations without cracking or delamination, which could compromise its waterproofing properties.
- Chemical Resistance Test: Conformal coatings may encounter various chemicals in their operational environment. Testing involves exposing the coated samples to specific chemicals and assessing any adverse effects on the coating’s integrity.
- Abrasion Resistance Test: Coatings should withstand mechanical abrasion encountered during handling or operation. Abrasion tests simulate these conditions to evaluate the coating’s durability.
- Dielectric Strength Test: This test measures the coating’s ability to resist electrical breakdown when subjected to high voltage. A compromised coating may allow moisture ingress, leading to electrical failure.
- Salt Spray Test: Coated samples are exposed to a salt spray mist to simulate harsh maritime environments. The test assesses the coating’s ability to resist corrosion caused by saltwater exposure.
- Electrochemical Impedance Spectroscopy (EIS): EIS measures the electrical impedance of the coating system over a range of frequencies. Changes in impedance can indicate the presence of defects or degradation in the coating.
- Visual Inspection and Microscopy: Optical and electron microscopy techniques can examine the coating’s surface for defects, cracks, or voids that may compromise its effectiveness.
Combining these tests provides a comprehensive evaluation of the waterproof conformal coating’s effectiveness, ensuring the reliability and longevity of electronic devices in challenging environments.
What considerations are essential for selecting the suitable waterproof conformal coating for a specific application?
Selecting the appropriate waterproof conformal coating for a specific application involves careful consideration of several key factors to ensure optimal performance and compatibility:
- Environmental Conditions: Understand the operating environment where the coated component will be deployed. Consider factors such as temperature extremes, humidity levels, chemical exposure, UV radiation, and potential mechanical stresses. The coating must withstand these conditions without degrading or compromising its protective capabilities.
- Substrate Compatibility: Assess the material composition of the substrate to be coated. Ensure compatibility between the conformal coating and the substrate material to prevent delamination, adhesion failure, or chemical reactions that could compromise performance or damage the substrate.
- Application Method: Evaluate the preferred application method, whether spraying, dipping, brushing, or selective coating. Different coatings may be better suited for specific application techniques, and compatibility with the chosen method is crucial for achieving uniform coverage and optimal protection.
- Thickness and Coverage: Determine the conformal coating’s required thickness and coverage area to provide adequate protection against moisture and other environmental hazards. Balance the need for sufficient coverage with the risk of adding excessive weight or thickness that could impact the performance or functionality of the coated component.
- Curing Process: Consider the curing mechanism and requirements of the coating, including temperature, humidity, and curing time. Ensure that the curing process can be effectively carried out within the constraints of the manufacturing or assembly process without causing delays or compromising quality.
- Regulatory Compliance: Verify that the selected conformal coating meets relevant industry standards and regulatory requirements for the intended application, especially in industries such as aerospace, automotive, or medical devices where stringent standards may apply.
- Long-Term Reliability: Assess the long-term reliability and durability of the conformal coating under anticipated operating conditions. Look for coatings with proven track records of performance in similar applications or environments to minimize the risk of premature failure or degradation over time.
By carefully considering these factors and conducting thorough testing and evaluation, you can select the suitable waterproof conformal coating that offers reliable protection and longevity for your specific application.
What future trends are anticipated in developing and using waterproof conformal coatings?
In waterproof conformal coatings, several future trends are anticipated, driven primarily by advancements in materials science, industry demands, and technological innovations. Here are some critical trends expected:
- Nanotechnology Integration: The integration of nanotechnology is expected to revolutionize waterproof conformal coatings. Nanoparticle-based coatings offer superior properties such as enhanced durability, increased resistance to harsh environments, and improved adhesion. These coatings can provide superior barrier properties while maintaining flexibility, which is crucial for conformal coatings used in various electronic and automotive applications.
- Eco-friendly Formulations: With increasing environmental awareness and regulations, there is a growing demand for eco-friendly conformal coatings. Future trends will likely see the development of coatings based on renewable materials, bio-based polymers, and solvent-free formulations. These coatings will effectively protect against moisture and contaminants while reducing environmental impact.
- Enhanced Durability and Performance: Future coatings will exhibit enhanced durability and performance characteristics. This includes improved resistance to temperature extremes, chemicals, UV radiation, and mechanical stress. Advanced formulations will ensure prolonged protection of electronic components, even in challenging operating conditions, thus extending the lifespan of devices and reducing maintenance requirements.
- Innovative Coatings with Self-Healing Properties: Developing intelligent coatings with self-healing properties is a promising future trend. These coatings can autonomously repair minor damages, scratches, or cracks, thereby maintaining the integrity of the protective layer over time. Self-healing coatings will be particularly beneficial in applications where continuous protection is critical, such as aerospace, automotive, and marine industries.
- Conformal Coatings for Flexible Electronics: With the growing popularity of flexible and wearable electronics, there will be an increased demand for conformal coatings tailored to these specific applications. Future coatings must offer flexibility, stretchability, and conformability to accommodate the unique requirements of flexible substrates while providing reliable waterproofing and protection.
The future of waterproof conformal coatings will be characterized by integrating advanced materials, eco-friendly formulations, enhanced performance, and tailored solutions for emerging technologies like flexible electronics. These trends will contribute to developing more robust, sustainable, and versatile coatings capable of meeting the evolving needs of various industries.
Conclusion:
Waterproof conformal coatings are indispensable guardians for electronic devices, ensuring their longevity and reliability in harsh environments. From safeguarding automotive electronics from moisture to protecting aerospace components from corrosive chemicals, these coatings play a pivotal role across various industries. As technology evolves, so do the demands placed on waterproof conformal coatings, driving innovation and the development of more advanced solutions. By understanding the intricacies of waterproof conformal coatings and staying abreast of the latest advancements, industries can effectively mitigate risks and enhance the performance of their electronic systems.
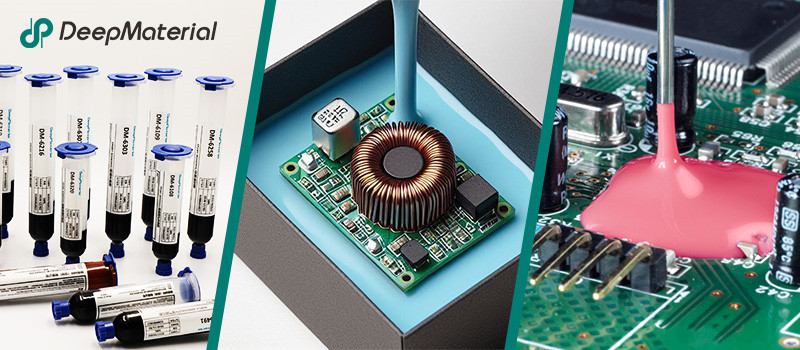
About DeepMaterial
DeepMaterial is a trusted supplier of encapsulant materials that are used in electronics manufacturing worldwide. From chip on board encapsulants such as glob top material to conformal coatings, underfills, low pressure molding, and potting solutions, DeepMaterial offers a full range of circuit board protection materials that effectively protect circuit boards while help reduce costs. More…Deepmaterial is a the manufacturer of epoxy adhesives including hardeners, metalbond, and metal filled resins. Structural, toughened medium viscosity, and non-sag adhesives are also offered. Some adhesives are resistant to thermal shock, chemical, vibration dampening, and impact. Suitable for metals, plastics, wood, and ceramics. Serves electronics, aerospace, automotive, tooling, marine, and construction industries. REACH and RoHS compliant. FDA approved. UL listed. Meets military specifications. We are the one of best adhesive manufacturers in China.
Blogs & News
Potting compounds are at the frontline of electronics assembly, delivering effective protection in challenging environmental conditions while improving mechanical strength and offering high electric insulation. Used within a variety of industries, electrical potting compounds are found within a broad range of consumer electronics, as well as used in applications across the automotive, aerospace, and other industries where electronic assemblies are prevalent.
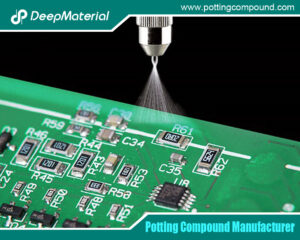
The Ultimate Guide to Electrical Potting Compound and Market Application
The Ultimate Guide to Electrical Potting Compound and Market Application In the modern world of electronics, where devices are increasingly compact and exposed to harsh
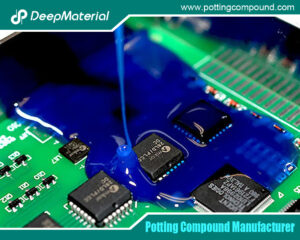
The Top Polyurethane Potting Compound
The Top Polyurethane Potting Compound In the fast-evolving world of electronics and industrial manufacturing, protecting sensitive components from environmental hazards is critical to ensuring reliability
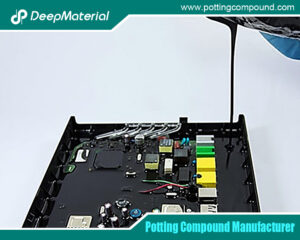
Advanced Epoxy Potting Compound for Superior Electronic Protection
Advanced Epoxy Potting Compound for Superior Electronic Protection In the realm of electronics and industrial manufacturing, protecting sensitive components from environmental hazards is critical to
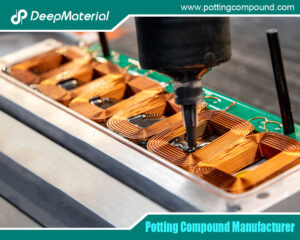
Waterproof Potting Compound: A Comprehensive Guide
Waterproof Potting Compound: A Comprehensive Guide In today’s technology-driven world, protecting sensitive electronic components from environmental hazards is paramount. One of the most effective solutions
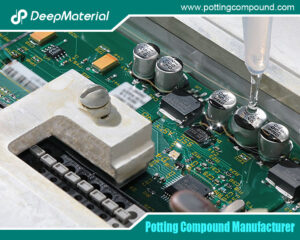
Silicone Potting Compound for Electronics
Silicone Potting Compound for Electronics In the rapidly evolving world of electronics, ensuring the reliability, durability, and performance of electronic components is paramount. One critical
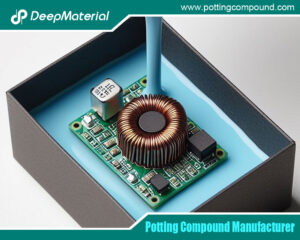
Potting Compound vs. Epoxy: A Comprehensive Comparison
Potting Compound vs. Epoxy: A Comprehensive Comparison In the world of electronics, manufacturing, and material encapsulation, two terms frequently come up: potting compounds and epoxy.