What is conformal coating in PCB
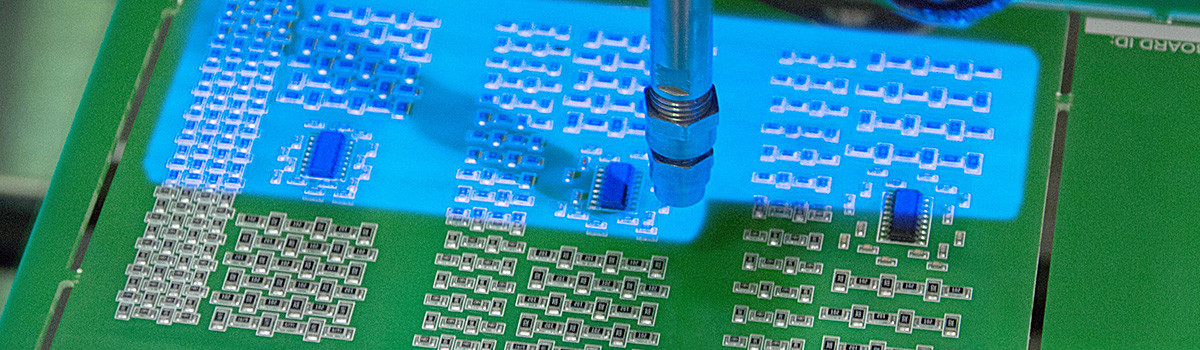
Conformal coating in PCB (Printed Circuit Board) assembly plays a crucial role in protecting electronic components from environmental factors such as moisture, dust, chemicals, and temperature extremes. It’s a thin protective layer applied to the surface of PCBs to insulate and safeguard them against adverse conditions. Understanding the significance, types, application methods, and benefits of conformal coating is essential for ensuring the reliability and longevity of electronic devices.
Table of Contents
ToggleVital details you need to be acquainted with:
What is conformal coating in PCB assembly?
Conformal coating is a protective layer applied to printed circuit boards (PCBs) to safeguard them against environmental factors such as moisture, dust, chemicals, and temperature extremes. This coating is essential for enhancing the reliability and longevity of electronic devices, particularly those used in harsh operating conditions like automotive, aerospace, marine, and industrial applications.
The primary purpose of conformal coating is to provide a barrier that prevents corrosion, electrical short circuits, and other forms of damage that could compromise the PCB’s functionality. It also offers insulation against electrical interference and reduces the risk of arcing or leakage between conductive elements.
Several types of conformal coatings are available, including acrylics, silicones, urethanes, and epoxies. Each type has its properties suited to different environmental challenges and application requirements. For example, acrylic coatings are cost-effective and protect against moisture and fungus, while silicone coatings offer excellent flexibility and high-temperature resistance.
The application process involves carefully spraying, dipping, or brushing the coating onto the PCB surface. It’s crucial to ensure uniform coverage without creating excess buildup that could lead to issues such as uneven coating thickness or interference with component functionality. Additionally, proper curing of the coating is essential to achieve the desired protective properties.
Conformal coating materials may be transparent or colored, allowing for visual inspection of the PCB after application. Some coatings also fluoresce under UV light, aiding inspection and quality control processes.
Despite its protective benefits, conformal coating can pose challenges during PCB rework or repair. It must be removed before soldering or component replacement. Specialized techniques and chemicals selectively remove the coating without damaging the underlying components of PCB traces.
Conformal coating plays a vital role in PCB assembly by safeguarding electronic devices from environmental hazards, enhancing reliability, and extending their operational lifespan in demanding applications. Proper selection and application of conformal coating are essential in ensuring electronic assemblies’ overall quality and performance.
Why is conformal coating necessary for PCBs?
Conformal coating is a protective layer applied to printed circuit boards (PCBs) to safeguard them from environmental factors and ensure their longevity and reliability. There are several reasons why conformal coating is necessary:
- Environmental Protection: PCBs are often exposed to harsh environments such as moisture, dust, chemicals, and temperature variations. Conformal coating acts as a barrier, preventing these elements from damaging the sensitive components on the board. It enhances the PCB’s resistance to corrosion, oxidation, and other forms of degradation, thereby extending its operational lifespan.
- Insulation: Conformal coatings provide electrical insulation, safeguarding the PCB against short circuits and electrical failures. By encapsulating conductive traces and components, the coating helps prevent unintended electrical connections caused by contamination, debris, or humidity, which could compromise the board’s performance or lead to catastrophic failures.
- Mechanical Protection: PCBs may encounter mechanical stresses during handling, transportation, or operation. Conformal coatings offer mechanical support by stabilizing components, reducing vibration-induced damage, and preventing physical impacts that could dislodge or damage fragile parts. This mechanical protection ensures the structural integrity of the PCB, reducing the risk of failures due to mechanical factors.
- Improved Performance: Conformal coatings can enhance the performance of PCBs by optimizing signal integrity, reducing crosstalk between traces, and minimizing electromagnetic interference (EMI). By effectively isolating sensitive components from external electromagnetic fields and noise, the coating helps maintain signal integrity and reliability, especially in high-frequency or noise-sensitive applications.
- **Conformal coating facilitates easier troubleshooting and repair by preventing accidental solder bridges between adjacent components or traces during rework or repair processes.
Conformal coating is essential for PCBs to ensure environmental resilience, electrical insulation, mechanical durability, improved performance, and easier maintenance. By providing a protective barrier against various environmental factors and enhancing the overall reliability of PCBs, conformal coatings contribute significantly to the functionality and longevity of electronic devices and systems.
What are the environmental factors that conformal coating protects against?
Conformal coating is a protective material applied to electronic circuitry to safeguard against various environmental factors. These coatings are a barrier, shielding sensitive components from moisture, dust, chemicals, temperature fluctuations, and mechanical stress. Understanding these environmental factors is crucial for selecting the appropriate coating material and application method.
- Moisture: Moisture can lead to corrosion and short circuits in electronic components. Conformal coatings create a barrier that prevents moisture ingress, thus safeguarding the integrity of the circuitry.
- Dust and Debris: Dust particles and other debris can accumulate on electronic components, potentially causing overheating or electrical shorts. Conformal coatings seal off the circuitry, reducing the risk of contamination and ensuring reliable performance in dusty environments.
- Chemical Exposure: Harsh chemicals in industrial or automotive environments can corrode electronic components. Conformal coatings provide chemical resistance, protecting against exposure to solvents, fuels, oils, and other corrosive substances.
- Temperature Extremes: Electronic devices may operate in environments with extreme temperatures, such as automotive engine compartments or outdoor installations. Conformal coatings offer thermal insulation, dissipating heat and providing a protective barrier against high and low temperatures.
- Mechanical Stress: Vibrations, shocks, and physical impacts can damage delicate electronic components. Conformal coatings add a layer of protection, dampening vibrations and reducing the risk of mechanical damage during handling, transportation, or operation.
- UV Radiation: Exposure to ultraviolet (UV) radiation can degrade certain electronic materials and cause premature failure. Some conformal coatings offer UV stability, shielding the underlying circuitry from the harmful effects of sunlight or artificial UV sources.
- Fungal Growth: In humid or damp environments, fungal growth on electronic components can compromise performance and reliability. Conformal coatings with anti-fungal properties inhibit microbial growth, ensuring the longevity of the coated electronics.
By mitigating these environmental risks, conformal coatings play a vital role in enhancing electronic devices’ reliability, durability, and lifespan in diverse operating conditions. The appropriate coating material and application method depends on specific environmental challenges, desired performance characteristics, and regulatory requirements.
How does conformal coating prevent moisture damage to PCBs?
Conformal coating is a protective layer applied to printed circuit boards (PCBs) to safeguard them from environmental factors, primarily moisture. This coating is a barrier, preventing moisture from permeating the sensitive electronic components on the PCB. Its effectiveness in preventing moisture damage lies in several fundamental mechanisms:
- Barrier to Moisture Penetration: Conformal coatings create a physical barrier that obstructs moisture ingress into the PCB. These coatings are typically made of acrylics, silicones, urethanes, or epoxy resins, forming a continuous film over the PCBs surface. This film prevents direct contact between the components and any moisture in the surrounding environment.
- Hydrophobic Properties: Many conformal coatings exhibit hydrophobic characteristics that repel water. This property is advantageous as it discourages moisture from adhering to the surface of the PCB. Instead, water droplets tend to bead up and roll off, reducing the likelihood of moisture accumulation and penetration.
- Sealing of Vulnerable Areas: Conformal coatings can penetrate tiny crevices, gaps, and exposed solder joints on the PCB surface. By sealing these vulnerable areas, the coating prevents moisture from seeping into critical areas that could cause damage, such as corroding metal traces or short-circuiting electronic components.
- Insulation: In addition to protecting against moisture, conformal coatings provide electrical insulation. This insulation property is crucial for maintaining the integrity of the circuitry, as moisture ingress can lead to conductive pathways forming between components, resulting in malfunctions or failures.
- Chemical Resistance: Some conformal coatings resist chemicals commonly found in the environment, including moisture-carrying contaminants like salt or sulfur. The coating further enhances the PCB’s resilience against moisture-related damage by repelling or withstanding these corrosive substances.
Conformal coatings prevent moisture damage to PCBs by forming a protective barrier, repelling water, sealing vulnerable areas, providing insulation, and offering resistance to corrosive substances. By effectively mitigating the risks associated with moisture ingress, conformal coatings help ensure the reliability and longevity of electronic devices in various operating environments.
What types of conformal coatings are commonly used in PCB assembly?
Conformal coatings protect printed circuit boards (PCBs) from environmental factors such as moisture, dust, chemicals, and temperature variations. Common types of conformal coatings used in PCB assembly include:
- Acrylics: Acrylic conformal coatings are versatile and widely used due to their excellent moisture resistance, flexibility, and ease of application. They offer good protection against environmental factors and are relatively cost-effective. Acrylic coatings can be applied by spraying, brushing, or dipping methods.
- Silicones: Silicones provide outstanding resistance to high temperatures, making them suitable for applications where PCBs are exposed to extreme heat. They offer excellent flexibility and chemical resistance but can be more challenging to remove if rework or repair is needed.
- Urethanes: Urethane conformal coatings offer superior chemical resistance and durability compared to acrylics and silicones. They provide excellent protection against abrasion and harsh environments, making them suitable for applications in industries such as automotive and aerospace.
- Epoxy: Epoxy coatings provide exceptional protection against moisture and chemical exposure. They offer high dielectric strength and excellent adhesion to PCB substrates. Epoxy coatings can be either rigid or flexible, depending on the formulation, and they are often used in demanding applications where robust protection is required.
- Parylene: Parylene coatings offer unique properties such as ultra-thin and pinhole-free protection. They provide excellent moisture barrier properties and chemical resistance while maintaining the electrical properties of the PCB. Parylene coatings are deposited through vapor deposition, making them suitable for coating complex geometries and sensitive components.
- Fluoropolymers: Fluoropolymer coatings like Teflon offer exceptional non-stick and low-friction properties and good chemical resistance. They are often used in applications where PCBs are exposed to harsh chemicals or require easy cleaning, such as in medical devices and industrial equipment.
Each type of conformal coating has its advantages and is chosen based on the application’s specific requirements, including environmental conditions, desired protection level, ease of application, and cost considerations. Proper selection and application of conformal coatings are essential to ensure the reliability and longevity of PCBs in various operating environments.
What are the differences between acrylic, silicone, urethane, and epoxy conformal coatings?
Conformal coatings protect electronic components from environmental factors such as moisture, dust, chemicals, and temperature extremes. Acrylic, silicone, urethane, and epoxy coatings are among the most commonly used types, offering distinct properties and advantages.
Acrylic conformal coatings are known for their excellent moisture resistance, transparency, and ease of application. They form a thin protective layer that adheres well to various substrates, including printed circuit boards (PCBs). Acrylic coatings are typically cost-effective and provide good electrical insulation properties, making them suitable for multiple applications.
Silicone conformal coatings offer exceptional flexibility, high-temperature resistance, and excellent protection against moisture and chemicals. They maintain their properties over a wide temperature range, making them ideal for harsh environments where thermal cycling is prevalent. Silicone coatings also exhibit good dielectric properties, ensuring reliable insulation for electronic components.
Urethane conformal coatings provide robust protection against abrasion, chemicals, and solvents. They offer excellent mechanical strength and adhesion properties, making them suitable for applications requiring durability and resistance to physical damage. Urethane coatings are often chosen for outdoor or industrial environments where exposure to harsh conditions is expected.
Epoxy-conformal coatings are renowned for their superior adhesion and chemical resistance. They form a hard, durable protective layer that effectively withstands mechanical stress and environmental hazards. Epoxy coatings also provide excellent protection against moisture and humidity, making them suitable for applications where long-term reliability is crucial.
Each type of conformal coating has its unique characteristics and advantages. Acrylic coatings offer cost-effectiveness and ease of application; silicone coatings provide flexibility and high-temperature resistance; urethane coatings offer durability and chemical resistance; and epoxy coatings provide superior adhesion and protection against moisture. Selecting the most suitable coating depends on the application’s specific requirements, including environmental conditions, performance criteria, and budget constraints.
How does the choice of conformal coating material affect PCB performance?
The choice of conformal coating material significantly influences the performance and reliability of a printed circuit board (PCB) in various ways.
- Environmental Protection:Conformal coatings serve as a protective barrier against environmental factors such as moisture, dust, chemicals, and temperature fluctuations. The selection of coating material determines the level of protection provided. For instance, silicone coatings offer excellent resistance to moisture and temperature extremes, making them suitable for harsh environments, while acrylic coatings provide reasonable protection against dust and chemicals.
- Electrical Insulation:Conformal coatings insulate PCB components, preventing electrical shorts and leakage. Different coating materials have varying dielectric properties that can affect the electrical performance of the board. Silicone coatings generally have higher dielectric strength than acrylics, making them suitable for high-voltage applications.
- Thermal Management:Certain conformal coatings possess thermal conductivity properties that aid in heat dissipation from components, thereby improving overall thermal management. For instance, epoxy-based coatings with fillers like alumina offer better thermal conductivity than non-filled coatings, enhancing heat dissipation and preventing component overheating.
- Adhesion and Flexibility:The adhesion strength and flexibility of the coating material are crucial for long-term reliability, especially in applications where the PCB may experience mechanical stress or vibration. Polyurethane coatings are known for their excellent adhesion to various substrates and flexibility, providing robust protection even in dynamic environments.
- Chemical Compatibility:Conformal coatings must be compatible with the PCB components and soldering materials to ensure long-term reliability. Some coatings may react with certain materials or flux residues, leading to delamination or corrosion issues. Understanding the chemical compatibility of the coating material with other substances used in the assembly process is essential for preventing such problems.
The choice of conformal coating material plays a vital role in determining PCBs’ performance, reliability, and longevity by offering protection against environmental hazards, providing electrical insulation, aiding in thermal management, and ensuring strong adhesion, flexibility, and chemical compatibility with other materials used in the assembly process. Therefore, selecting the appropriate coating material based on the application’s specific requirements is crucial for optimizing PCB performance.
What factors should be considered when selecting a conformal coating for a specific application?
Selecting the appropriate conformal coating for a specific application involves carefully considering various factors to ensure optimal performance and protection of electronic components. Some key factors to consider include:
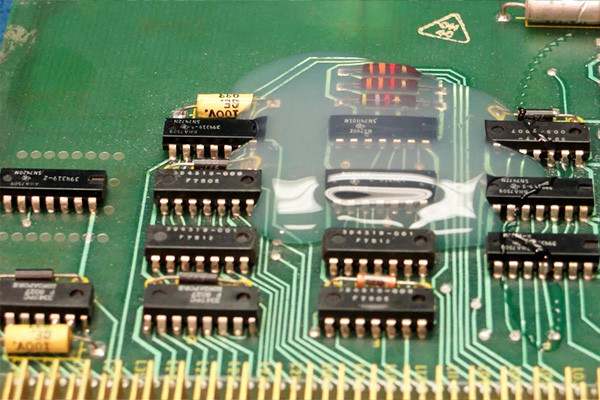
- Environmental Conditions: Evaluate the operating environment for factors such as temperature extremes, humidity, chemical exposure, and mechanical stress. Choose a coating that can withstand these conditions without degradation.
- Compatibility: Ensure compatibility between the conformal coating and the materials used in the assembly, including substrates, components, solder masks, and adhesives. Incompatibility could lead to adhesion issues or even damage to the components.
- Application Method: Consider the available application methods such as spray, dip, brush, or selective coating. Select a coating compatible with the chosen method to achieve uniform coverage and desired thickness.
- Curing Process: Determine the curing method required for the coating (e.g., heat cure, UV cure, moisture cure). Ensure that the curing process aligns with the manufacturing process and does not introduce additional complexities or bottlenecks.
- Thickness Requirements: Evaluate the desired coating thickness based on the level of protection required and any dimensional constraints. Different coatings may offer varying thickness capabilities, so choose one that meets the application’s specific requirements.
- Electrical Properties: Consider the impact of the coating on electrical properties such as insulation resistance, dielectric strength, and impedance. Ensure that the coating does not compromise the electrical performance of the assembly.
- Mechanical Properties: Assess the mechanical properties of the coating, including flexibility, hardness, and abrasion resistance. Choose a coating that can withstand mechanical stress and movement without cracking or delamination.
- Optical Clarity: In applications where visual inspection of components is necessary, consider the optical clarity of the coating. Select a coating that provides adequate transparency or clarity without compromising other properties.
- Regulatory Compliance: Ensure that the chosen conformal coating complies with relevant industry standards and regulations, such as RoHS (Restriction of Hazardous Substances) and REACH (Registration, Evaluation, Authorization, and Restriction of Chemicals).
- Cost Considerations: Evaluate the overall cost of the coating, including material cost, application costs, and potential rework or repair expenses. Balance the performance requirements with the project budget constraints.
By carefully considering these factors, manufacturers can select the most suitable conformal coating to ensure the reliability and longevity of electronic assemblies in their specific applications.
Can conformal coating improve the lifespan of electronic devices?
Conformal coating is a protective layer applied to electronic circuitry to enhance reliability and longevity by shielding components from environmental stresses. This thin film adheres tightly to the contours of PCBs (Printed Circuit Boards), providing insulation against moisture, dust, chemicals, and other contaminants. While its primary purpose is to prevent corrosion and electrical short circuits, conformal coating indirectly contributes to extending the lifespan of electronic devices through several mechanisms.
Firstly, conformal coating is a barrier against moisture ingress, a significant cause of electronic failure. Moisture can lead to corrosion, dendritic growth, and leakage currents, all of which can compromise the functionality and lifespan of electronic components. Conformal coating mitigates these risks by sealing vulnerable areas, especially in humid or wet environments.
Secondly, conformal coating offers protection against mechanical stresses such as vibrations and thermal expansion. Electronic devices often encounter mechanical shocks during handling, transportation, or operation. These shocks can cause physical damage to delicate components or dislodge solder joints, leading to malfunctions or failure. Conformal coating provides an additional support layer, dampening vibrations, and stabilizing components, reducing the likelihood of mechanical failure.
Moreover, conformal coating can enhance resistance to chemical exposure. Electronics deployed in industrial or harsh environments may come into contact with corrosive substances or solvents, which can degrade unprotected components over time. Conformal coating acts as a shield, preventing direct contact and chemical reactions that could compromise device functionality.
Additionally, the conformal coating offers insulation against electrical interference and reduces the risk of short circuits caused by debris or contaminants. This insulation helps maintain signal integrity and prevents unintended electrical paths, improving overall reliability.
Conformal coating plays a crucial role in extending the lifespan of electronic devices by safeguarding them against moisture, mechanical stresses, chemical exposure, and electrical interference. By enhancing reliability and protecting components, conformal coating contributes to the longevity and performance of electronic products across various applications and environments.
What are the application methods for conformal coating on PCBs?
Conformal coating is a protective layer applied to printed circuit boards (PCBs) to safeguard them from environmental factors such as moisture, dust, chemicals, and temperature fluctuations. There are several methods for applying conformal coatings, each with advantages and suitability for different applications.
- Brush Application: This is one of the simplest and most cost-effective methods. It involves using a brush to apply the conformal coating onto the PCB surface manually. While it’s easy to control the thickness and coverage, it can be time-consuming and may result in uneven coating if not applied carefully.
- Dip Coating: The PCB is dipped into a tank containing the conformal coating material in this method. As it’s withdrawn, the excess coating is drained, leaving a uniform layer on the PCB surface. Dip coating is relatively fast and suitable for high-volume production. However, it may require additional equipment for drying and curing.
- Spray Coating: Spray coating involves using a spray gun or nozzle to apply the conformal coating onto the PCB surface. It offers good coverage and is suitable for complex PCB geometries. However, controlling the thickness of the coating and preventing overspray can be challenging.
- Selective Coating: This method involves applying the conformal coating only to specific areas of the PCB, typically using a robotic dispenser or a stencil. It helps mask sensitive components or areas that don’t require coating, reducing coating material consumption.
- Vapor Deposition: Vapor deposition involves heating the conformal coating material until it vaporizes and then allowing it to condense onto the PCB surface. This method produces a thin, uniform coating suitable for applications where precise control over coating thickness is critical.
- Curing and Drying: After applying the conformal coating, it must be cured or dried to form a protective film. This can be achieved through various methods such as air drying, UV curing, thermal curing, or combining these techniques, depending on the coating material used.
Choosing the most appropriate application method depends on factors such as the complexity of the PCB design, production volume, desired coating thickness, and budget constraints. Each method offers unique benefits and considerations, and manufacturers may employ various techniques to achieve the desired results.
How thin is the conformal coating layer typically applied to PCBs?
Conformal coating is a protective layer applied to printed circuit boards (PCBs) to safeguard them from environmental factors such as moisture, dust, chemicals, and temperature extremes. The thickness of the conformal coating is a critical parameter, as it must provide adequate protection without interfering with the functionality of the components or the assembly process. Typically, the thickness of conformal coating layers ranges from 25 to 250 micrometers (1 to 10 mils), with variations based on the application requirements and the specific coating material used.
The thickness of the conformal coating layer is determined by factors such as the viscosity of the coating material, the application method, and the desired level of protection. Low-viscosity coatings are applied in thin layers, while higher-viscosity coatings may result in thicker layers. Standard application methods include spraying, dipping, brushing, and selective coating.
Spraying is one of the most widely used methods for applying conformal coatings. It allows for precise control over the thickness of the coating layer and is suitable for both manual and automated processes. In spraying, the coating material is atomized into fine droplets and evenly distributed over the surface of the PCB. The thickness of the coating layer can be adjusted by controlling parameters such as spray pressure, nozzle size, and spraying distance.
Dipping involves immersing the PCB into a bath of liquid coating material. As the PCB is withdrawn from the tub, excess coating material drips off, leaving a uniform layer on the surface. The thickness of the coating layer is determined by factors such as the withdrawal speed and the viscosity of the coating material.
Brushing is a manual method for applying the coating material to the PCB surface using a brush or applicator. While brushing allows for precise control over the coating thickness in localized areas, it is less commonly used in automated assembly processes due to its labor-intensive nature.
Selective coating involves applying the coating material only to specific areas of the PCB, leaving other areas unprotected. This method is often used to protect sensitive components or areas prone to environmental damage while minimizing material usage and production costs.
The thickness of conformal coating layers applied to PCBs typically ranges from 25 to 250 microns, with variations based on factors such as coating material, application method, and desired level of protection. Precise control over the coating thickness is essential to ensure adequate protection of the PCB while avoiding interference with the components’ functionality.
What challenges may arise during the conformal coating process?
Conformal coating, a critical step in electronics manufacturing, involves applying a protective material layer onto circuit boards to safeguard them against environmental factors such as moisture, dust, chemicals, and temperature extremes. However, several challenges can arise during this process:
- Uniformity: Achieving uniform coating thickness across the circuit board can be challenging. Variations in substrate materials, component heights, and board geometries can lead to uneven coating thickness. Inadequate coverage may expose vulnerable areas, while excessive coating can cause issues with component functionality.
- Adhesion: Ensuring proper adhesion of the conformal coating to the substrate is crucial for long-term reliability. Poor adhesion can result in delamination or flaking of the coating, leaving underlying components vulnerable to environmental damage. Factors such as surface cleanliness, substrate material, and coating material compatibility influence adhesion quality.
- Curing: Conformal coatings typically require curing to achieve their desired properties, such as hardness and chemical resistance. Inadequate curing conditions, such as incorrect temperature, humidity, or duration, can lead to insufficient cross-linking and reduced coating performance. Improper curing can also result in issues such as tackiness or brittleness.
- Component Compatibility: Some conformal coating materials may not be compatible with specific electronic components or substrates. Chemical interactions between the coating and components could lead to corrosion, electrical malfunctions, or altered performance. Understanding material compatibility is essential to prevent such issues.
- Masking and Rework: Components that should not be coated, such as connectors or heatsinks, require masking during the coating process. Improper masking or incomplete removal post-coating can lead to functionality issues or damage. Reworking improperly coated boards adds time and cost to the manufacturing process.
- Environmental Considerations: Environmental factors such as temperature, humidity, and contaminants in the manufacturing environment can affect the coating process and the quality of the final product. Controlling these variables is essential to ensure consistent coating quality and reliability.
- Quality Control: Implementing robust quality control measures is necessary to detect defects or inconsistencies in the coating process. Automated inspection techniques, such as optical inspection or coating thickness measurement, can help identify and address issues early in manufacturing.
To ensure consistent and reliable conformal coating application, addressing these challenges requires careful process design, material selection, equipment calibration, and quality assurance measures.
Is there a risk of coating material interfering with PCB functionality?
Coating materials are likely to interfere with PCB (Printed Circuit Board) functionality. Coating materials are often applied to PCBs to protect against environmental factors such as moisture, dust, chemicals, and physical damage. However, if not carefully chosen or applied, these coatings can introduce several potential issues:
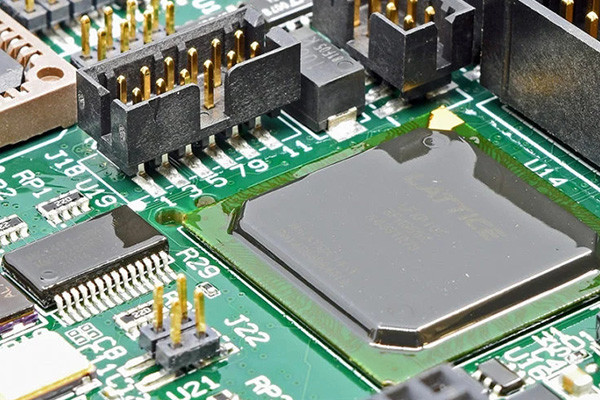
- Electrical Insulation: Coating materials are typically insulators. While this property protects the PCB from moisture and short circuits, it can also interfere with the electrical connections on the board if it seeps into or covers conductive traces, vias, or pads. This interference can result in unintended electrical discontinuities, signal degradation, or complete circuit failure.
- Thermal Insulation: Some coating materials may have poor thermal conductivity, leading to the trapping of heat generated by electronic components on the PCB. Excessive heat buildup can degrade component performance, reduce lifespan, or cause thermal stress-related failures.
- Chemical Compatibility: Coating materials must be compatible with the components and substances they protect against. Suppose the coating reacts chemically with any PCB materials or substances encountered in its operating environment. In that case, it can compromise the coating integrity and the functionality of the components.
- Mechanical Stress: Improperly applied or overly thick coating layers can introduce mechanical stress on the PCB. This stress may cause warping, delamination, or even physical damage to delicate components during assembly, operation, or thermal cycling.
- Corrosion and Contamination: While coating materials primarily aim to prevent corrosion and contamination, certain coatings may be susceptible to degradation over time when exposed to harsh environmental conditions. This degradation can compromise their protective properties and potentially introduce contaminants into the PCB environment.
To mitigate these risks, carefully selecting coating materials based on the specific application and operating environment is crucial. Additionally, precise application techniques, such as masking critical areas before coating, controlling coating thickness, and ensuring proper curing, can help minimize the potential for interference with PCB functionality while still providing adequate protection. Regular testing and inspection of coated PCBs are essential to ensure continued functionality and reliability.
How does conformal coating impact PCB repair and rework processes?
Conformal coating, a thin protective layer applied to printed circuit boards (PCBs), significantly impacts PCB repair and rework processes. While conformal coating protects against environmental factors such as moisture, dust, chemicals, and temperature fluctuations, it can also pose challenges during repair and rework.
One of the primary challenges is removing conformal coating to access and repair components. Traditional methods like scraping or chemical stripping may damage sensitive components or compromise the board’s integrity. Hence, specialized techniques such as laser ablation or localized heating are often employed to selectively remove the conformal coating without harming nearby components.
Furthermore, conformal coating can hinder visual inspection of PCBs, making identifying faults or damaged components difficult. Technicians may need to rely on X-ray inspection or other non-destructive testing methods to thoroughly examine the board’s integrity.
Conformal coating may interfere with soldering operations during rework processes, such as replacing faulty components or modifying circuitry. The coating’s insulating properties can inhibit proper solder wetting and adhesion, leading to poor solder joints or cold solder connections. To mitigate this issue, preheating the PCB or using specialized fluxes designed for coated surfaces may be necessary to ensure reliable soldering.
Relying on conformal coating after repair or rework is essential to protect the PCB against environmental hazards. However, achieving uniform coverage without causing bridging or uneven coating thickness can be challenging, particularly in the board’s intricate or densely populated areas. Careful application techniques, such as selective spraying or robotic dispensing, ensure consistent and reliable coating performance.
While conformal coating provides valuable protection for PCBs, it introduces complexities during repair and rework. Specialized techniques and careful handling are necessary to overcome challenges such as coating removal, inspection limitations, soldering difficulties, and reapplication to ensure the integrity and functionality of the PCBs after repair or modification.
Are there any industry standards or regulations governing conformal coating applications?
Conformal coating application is a crucial process in electronics manufacturing. It protects printed circuit boards (PCBs) and electronic components from environmental factors such as moisture, dust, chemicals, and temperature variations. While there isn’t a single global standard governing conformal coating application, several industry standards and regulations guide manufacturers to ensure quality and reliability in their processes.
One prominent standard is IPC-A-610, developed by the Association of Connecting Electronics Industries (IPC). IPC-A-610 sets the acceptability criteria for electronic assemblies, including conformal coating application. It defines various requirements for coating thickness, coverage, and uniformity, ensuring that coatings protect PCBs without causing electrical or mechanical issues.
MIL-STD-883 and MIL-STD-202, established by the U.S. Department of Defense, outline testing methods and performance requirements for electronic components and materials, including conformal coatings. These standards are often referenced in industries where reliability and ruggedness are critical, such as aerospace and defense.
ISO 9001, an international standard for quality management systems, also influences conformal coating applications by emphasizing process control, documentation, and continuous improvement. Adhering to ISO 9001 helps manufacturers ensure consistency and reliability in their coating processes.
In terms of regulations, the Restriction of Hazardous Substances (RoHS) Directive and the Registration, Evaluation, Authorization, and Restriction of Chemicals (REACH) Regulation in the European Union restrict the use of certain hazardous substances in electronics, including those used in conformal coatings. Compliance with RoHS and REACH requires manufacturers to carefully select coating materials and meet specified environmental and safety standards.
Moreover, industry-specific regulations, such as those imposed by the automotive or medical device sectors, may also dictate requirements for conformal coating applications to meet safety, reliability, and performance criteria.
Overall, while there isn’t a singular comprehensive standard for conformal coating application, manufacturers must navigate and adhere to a combination of industry standards, regulations, and customer specifications to ensure the quality and reliability of their coated electronic products.
What are the key benefits of using conformal coating in PCB assembly?
Conformal coating in PCB (Printed Circuit Board) assembly offers a range of benefits that enhance electronic devices’ reliability, durability, and performance. Here are the key advantages:
- Protection from Environmental Factors: Conformal coatings create a barrier between the delicate components of a PCB and potentially harmful environmental factors such as moisture, dust, chemicals, and extreme temperatures. This protection reduces the risk of corrosion, short circuits, and other damage caused by exposure to these elements, extending the lifespan of the PCB and the overall device.
- Enhanced Reliability: By safeguarding against environmental factors, conformal coatings increase the reliability of PCBs in various operating conditions. This is particularly crucial in automotive, aerospace, and medical devices, where reliability is paramount. The coating ensures consistent performance even in challenging environments, minimizing the likelihood of failures and costly repairs or replacements.
- Improved Electrical Insulation: Conformal coatings provide electrical insulation to prevent short circuits and other electrical failures. These coatings help maintain the integrity of the circuitry by isolating conductive traces and components from each other and external sources of electrical interference, thus reducing the risk of malfunctions and enhancing overall performance.
- Mechanical Protection: Besides electrical insulation, conformal coatings offer mechanical protection against physical damage such as scratches, abrasion, vibration, and impact. This is especially beneficial in applications where PCBs are subjected to mechanical stress during operation or handling, such as in portable electronic devices, industrial equipment, and automotive systems.
- Ease of Application and Maintenance: Conformal coatings can be applied using various methods, including spraying, dipping, brushing, or selective coating, making them suitable for different PCB designs and production processes. Moreover, these coatings are typically transparent and thin, allowing for easy visual inspection of the PCB and facilitating maintenance and repair tasks.
- Compliance with Standards and Regulations: Many industries have strict requirements regarding electronic devices’ reliability, safety, and environmental impact. Conformal coatings help PCB assemblies meet these standards and regulations by providing the necessary protection and insulation, thus ensuring compliance and regulatory approval.
Conformal coating in PCB assembly offers significant benefits, including protection from environmental factors, enhanced reliability, improved electrical insulation, mechanical protection, ease of application and maintenance, and compliance with industry standards and regulations. These advantages contribute to electronic devices’ overall performance, longevity, and safety across various applications and industries.
Can conformal coating enhance the reliability of electronic devices in harsh environments?
Conformal coating is a protective layer applied to electronic components and circuit boards to enhance reliability, particularly in harsh environments. This coating is typically made of materials such as silicone, acrylic, or urethane. It conforms to the contours of the electronic assembly, providing a barrier against environmental factors like moisture, dust, chemicals, and temperature extremes. The application of conformal coating can significantly improve the durability and longevity of electronic devices in challenging conditions.
One key benefit of conformal coating is its ability to protect against moisture ingress, which is a leading cause of electronic failure. The coating seals components and circuitry from moisture, preventing corrosion and short circuits resulting from water exposure. This is particularly important in outdoor applications, industrial settings, or areas with high humidity.
Moreover, the conformal coating is a barrier against dust and debris, preventing them from accumulating on sensitive electronic components and causing malfunctions or failures. In environments where airborne particles are prevalent, such as manufacturing facilities or construction sites, this protective layer can be instrumental in maintaining the reliability of electronic devices.
Additionally, the conformal coating can offer insulation against electrical interference and enhance the dielectric strength of the assembly. This is especially beneficial in environments where electromagnetic interference (EMI) or radio frequency interference (RFI) may be present, as the coating helps mitigate potential disruptions to the electronics’ functionality.
Furthermore, conformal coating can improve the resistance of electronic devices to chemical exposure, including solvents, oils, and cleaning agents. This is advantageous in automotive, aerospace, and healthcare industries, where equipment may come into contact with various chemicals during operation or maintenance.
Conformal coating plays a crucial role in enhancing the reliability of electronic devices in harsh environments by protecting against moisture, dust, chemicals, and electrical interference. Its ability to safeguard components and circuitry from these environmental stressors helps prolong electronic assemblies’ lifespan and ensures consistent performance in demanding conditions.
How does conformal coating contribute to the overall reliability of electronic assemblies?
Conformal coating plays a crucial role in enhancing the reliability of electronic assemblies by providing a protective barrier against various environmental factors, mechanical stresses, and chemical contaminants. Here’s how it contributes:
- Environmental Protection: Electronic assemblies are often exposed to harsh environments, including moisture, dust, chemicals, and temperature fluctuations. Conformal coatings, typically silicone, acrylic, or polyurethane, form a protective layer that shields delicate electronic components from these external elements. By preventing moisture ingress, corrosion, and contamination, conformal coatings help extend the lifespan of electronic assemblies.
- Insulation: Conformal coatings are excellent electrical insulators, avoiding short circuits and leakage currents. They cover conductive traces, solder joints, and other exposed electrical components, reducing the risk of electrical failures caused by unintended contact with conductive materials or environmental contaminants. This insulation property is particularly critical in high-humidity or dusty environments where moisture or conductive debris could compromise the assembly’s integrity.
- Mechanical Stability: Electronic assemblies may experience mechanical stresses during handling, transportation, or operation. Conformal coatings provide mechanical reinforcement by encapsulating fragile components and stabilizing solder connections. This helps to mitigate the risks of mechanical damage such as cracks, fractures, or component displacement, thereby improving the overall robustness and reliability of the assembly.
- Enhanced Chemical Resistance: Conformal coatings resist various chemicals, including solvents, fuels, and cleaning agents. By forming a barrier against chemical exposure, they protect electronic components from degradation, corrosion, and performance degradation. This is particularly important in industrial or automotive applications where electronic assemblies may come into contact with aggressive chemicals or pollutants.
- Thermal Management: Some conformal coatings also exhibit thermal management properties, dissipating heat away from critical components and preventing overheating. By enhancing thermal conductivity or acting as thermal insulators, these coatings help maintain optimal operating temperatures, thereby reducing the risk of thermal-induced failures and improving the overall reliability of electronic assemblies.
Conformal coatings contribute significantly to the reliability of electronic assemblies by providing environmental protection, insulation, mechanical stability, chemical resistance, and thermal management. By mitigating the effects of external factors and enhancing the integrity of electronic components, conformal coatings play a vital role in ensuring the long-term performance and durability of electronic devices and systems.
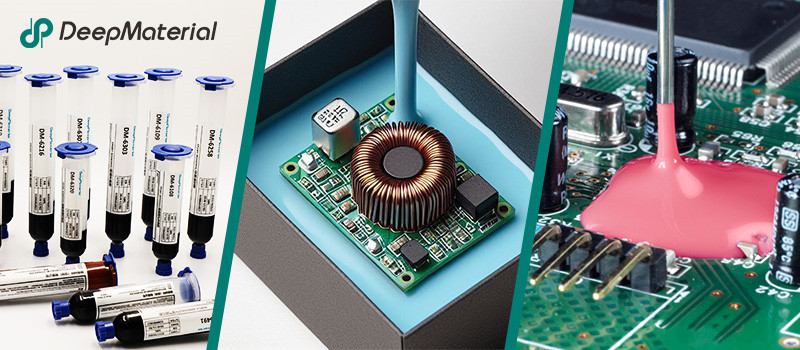
About DeepMaterial
DeepMaterial is a trusted supplier of encapsulant materials that are used in electronics manufacturing worldwide. From chip on board encapsulants such as glob top material to conformal coatings, underfills, low pressure molding, and potting solutions, DeepMaterial offers a full range of circuit board protection materials that effectively protect circuit boards while help reduce costs. More…Deepmaterial is a the manufacturer of epoxy adhesives including hardeners, metalbond, and metal filled resins. Structural, toughened medium viscosity, and non-sag adhesives are also offered. Some adhesives are resistant to thermal shock, chemical, vibration dampening, and impact. Suitable for metals, plastics, wood, and ceramics. Serves electronics, aerospace, automotive, tooling, marine, and construction industries. REACH and RoHS compliant. FDA approved. UL listed. Meets military specifications. We are the one of best adhesive manufacturers in China.
Blogs & News
Potting compounds are at the frontline of electronics assembly, delivering effective protection in challenging environmental conditions while improving mechanical strength and offering high electric insulation. Used within a variety of industries, electrical potting compounds are found within a broad range of consumer electronics, as well as used in applications across the automotive, aerospace, and other industries where electronic assemblies are prevalent.
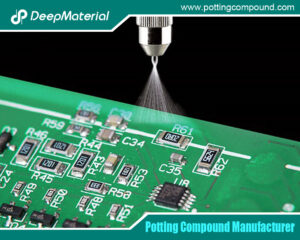
The Ultimate Guide to Electrical Potting Compound and Market Application
The Ultimate Guide to Electrical Potting Compound and Market Application In the modern world of electronics, where devices are increasingly compact and exposed to harsh
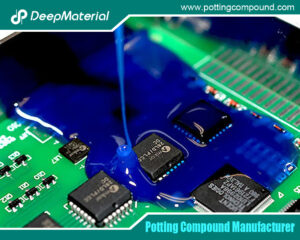
The Top Polyurethane Potting Compound
The Top Polyurethane Potting Compound In the fast-evolving world of electronics and industrial manufacturing, protecting sensitive components from environmental hazards is critical to ensuring reliability
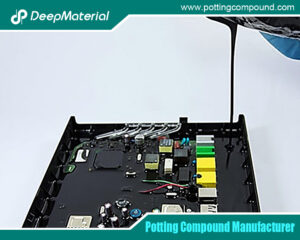
Advanced Epoxy Potting Compound for Superior Electronic Protection
Advanced Epoxy Potting Compound for Superior Electronic Protection In the realm of electronics and industrial manufacturing, protecting sensitive components from environmental hazards is critical to
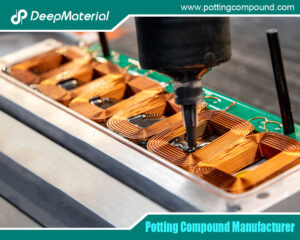
Waterproof Potting Compound: A Comprehensive Guide
Waterproof Potting Compound: A Comprehensive Guide In today’s technology-driven world, protecting sensitive electronic components from environmental hazards is paramount. One of the most effective solutions
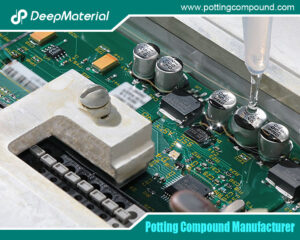
Silicone Potting Compound for Electronics
Silicone Potting Compound for Electronics In the rapidly evolving world of electronics, ensuring the reliability, durability, and performance of electronic components is paramount. One critical
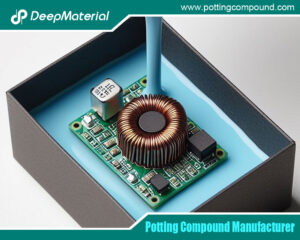
Potting Compound vs. Epoxy: A Comprehensive Comparison
Potting Compound vs. Epoxy: A Comprehensive Comparison In the world of electronics, manufacturing, and material encapsulation, two terms frequently come up: potting compounds and epoxy.