What is potting compound used for
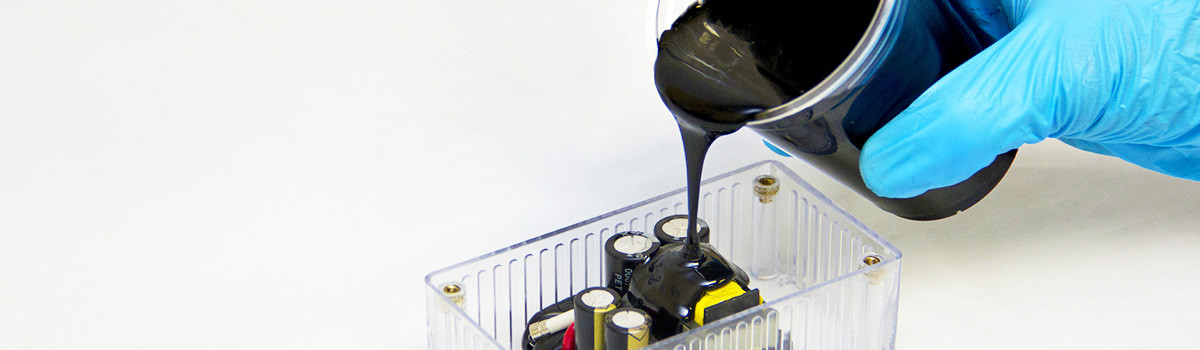
Potting compounds are versatile materials used across various industries for a multitude of applications. These compounds are designed to encapsulate electronic components, providing protection from environmental factors such as moisture, chemicals, and mechanical stresses. In this category, we delve into the wide-ranging uses of potting compounds, exploring their applications in different fields and shedding light on their significance in ensuring the durability and reliability of electronic devices.
Table of Contents
ToggleKey facts that are imperative to grasp:
What is a potting compound?
Potting compound, or potting resin or encapsulant, is a versatile material used in various industries for encapsulating, protecting, and insulating electronic components or assemblies. It serves as a barrier against environmental factors such as moisture, dust, vibration, and mechanical shock, ensuring the reliability and longevity of electronic devices.
Potting compounds are composed of polymers, epoxies, silicones, or urethanes and come in liquid or semi-liquid form before curing into a solid, protective shell. They possess thermal conductivity, electrical insulation, and chemical resistance properties, making them suitable for various applications.
The primary function of potting compounds is to protect sensitive electronic components from environmental stresses. The potting compound shields them from moisture by encapsulating components such as circuit boards, sensors, or wires, which can cause corrosion, short circuits, or electrical failure. Additionally, it provides mechanical support, reducing the risk of damage from shock or vibration during transportation or operation.
The choice of potting compound depends on the application’s specific requirements. For instance, applications requiring high thermal conductivity may opt for compounds with metallic fillers to enhance heat dissipation. Conversely, applications exposed to extreme temperatures might utilize silicone-based compounds known for their wide temperature range and flexibility.
Potting compounds also play a crucial role in enhancing the safety and reliability of electronic devices in hazardous environments. In industries such as automotive, aerospace, or oil and gas, where equipment operates in harsh conditions, potting compounds protect against moisture ingress, chemical exposure, and thermal cycling.
Moreover, potting compounds facilitate miniaturization by allowing designers to consolidate multiple components into one package. This reduces the overall size of electronic assemblies, simplifies manufacturing processes, and improves system reliability.
potting compounds are vital in electronics manufacturing, offering protection, insulation, and reliability to electronic components and assemblies. Its versatility and customizable properties make it indispensable across various industries where robustness and longevity are paramount.
How does potting compound differ from other encapsulation materials?
Potting compound, also known as potting resin or encapsulation compound, is a type of material used in electronics manufacturing to protect electronic components and circuitry from environmental factors such as moisture, dust, vibration, and thermal shock. It differs from other encapsulation materials primarily in its application method, composition, and properties.
- Application Method: Potting compound is typically applied as a liquid that cures to form a solid, protective layer around the electronic component or assembly. It is poured or dispensed onto the target area and allowed to cure, encapsulating the device completely. This method provides complete coverage and ensures that the component is fully sealed. In contrast, other encapsulation materials such as conformal coatings or encapsulating resins may be applied as coatings or sprayed onto the surface, providing a thin protective layer rather than complete encapsulation.
- Composition: Potting compounds are formulated from a variety of materials, including epoxies, silicones, urethanes, and polyurethanes. These materials are chosen for their ability to provide mechanical support, chemical resistance, thermal conductivity, and electrical insulation. The specific composition can be tailored to meet the requirements of the application, such as temperature range, flexibility, or hardness. Other encapsulation materials may have different compositions optimized for specific properties like flexibility, adhesion, or UV resistance.
- Properties: Potting compounds offer excellent protection against harsh environmental conditions, making them suitable for demanding applications in industries such as automotive, aerospace, and industrial electronics. They provide robust mechanical support, high dielectric strength, and resistance to chemicals and solvents. Additionally, potting compounds can dissipate heat effectively, enhancing the thermal management of electronic devices. Other encapsulation materials may prioritize different properties, such as flexibility for conformal coatings or optical clarity for optical encapsulants.
Potting compound differs from other encapsulation materials in its application method, composition, and properties. Its ability to provide complete encapsulation, along with a balance of mechanical, thermal, and chemical properties, makes it a preferred choice for protecting electronic components in challenging environments.
What are the primary components of potting compounds?
Potting compounds, also known as encapsulants or potting materials, protect electronic components, circuits, and devices from environmental factors such as moisture, dust, vibrations, and temperature fluctuations. They typically consist of several primary components carefully formulated to provide the desired properties. Here are the primary components of potting compounds:
- Resin: Resins serve as the matrix or binder in potting compounds. They are typically polymers like epoxies, silicones, polyurethanes, or acrylics. The choice of resin depends on the desired mechanical strength, flexibility, chemical resistance, and thermal conductivity.
- Hardener or Catalyst: Resins often require a hardener or catalyst to initiate curing. This component reacts with the resin to form a cross-linked network, providing the material with its final strength and rigidity. The ratio of resin to hardener is critical for achieving the desired properties and curing time.
- Fillers: Fillers are added to potting compounds to modify their physical properties and reduce costs. Joint fillers include silica, alumina, glass fibers, and mineral powders. They can improve thermal conductivity, reduce shrinkage during curing, enhance mechanical strength, and adjust viscosity.
- Plasticizers: Plasticizers are additives that improve the flexibility and elongation of potting compounds. They help prevent the material from becoming too brittle, especially when exposed to temperature variations. Phthalates, adipates, and trimellitates are examples of commonly used plasticizers.
- Adhesion Promoters: Adhesion promoters enhance the bonding between the potting compound and substrates such as metals, ceramics, or plastics. They improve adhesion by creating chemical bonds or increasing surface roughness. Silanes, titanates, and organofunctional silanes are typical adhesion promoters in potting compounds.
- Flame Retardants: Flame retardants are essential for ensuring the safety of electronic devices, particularly in applications where fire hazards are a concern. They inhibit or suppress the combustion process, reducing the spread of flames. Common flame retardants include phosphorus-based compounds, halogenated compounds, and inorganic fillers like aluminum trihydrate.
- Colorants and Additives: Colorants are sometimes added to potting compounds for identification or aesthetic purposes. Additionally, other additives such as antioxidants, UV stabilizers, and thickeners may be included to improve performance and longevity in specific applications.
The precise formulation of potting compounds depends on the application’s requirements, including environmental conditions, electrical properties, and desired physical characteristics. Balancing these components is essential to ensure optimal performance and reliability of encapsulated electronic devices.
How does potting compound protect electronic components?
A potting compound, or encapsulant or potting resin, encapsulates or encases electronic components within a protective shell. It serves several crucial functions in safeguarding electronic components:
- Mechanical Protection:A potting compound provides mechanical support and protection against physical damage, such as impact, vibration, and compression. Encapsulating delicate components prevents them from being damaged by external forces during handling, transportation, or operation. This is particularly important in rugged environments such as automotive, aerospace, or industrial settings where electronic devices are subjected to harsh conditions.
- Environmental Protection:Potting compounds offer resistance against environmental factors such as moisture, dust, chemicals, and extreme temperatures. By creating a barrier around the components, they shield them from moisture ingress, corrosion, chemical exposure, and thermal stress. This ensures the longevity and reliability of electronic devices, especially in outdoor or corrosive environments.
- Electrical Insulation:Potting compounds insulate electronic components electrically, preventing short circuits and electrical interference. Encapsulating conductive elements reduces the risk of unintended electrical connections and electromagnetic interference (EMI), which can degrade the performance and reliability of electronic systems.
- Thermal Management:Some potting compounds possess thermal conductivity properties that help dissipate heat generated by electronic components. By efficiently transferring heat away from sensitive devices, they prevent overheating and thermal damage, thereby enhancing the overall thermal management of electronic assemblies.
- Improved Reliability:By providing comprehensive protection against mechanical, environmental, and electrical threats, potting compound significantly enhances the reliability and lifespan of electronic components and assemblies. This is essential for critical applications where downtime or failure could have serious consequences, such as in medical devices, aerospace systems, or industrial machinery.
Potting compounds protect electronic components by offering mechanical support, environmental resistance, electrical insulation, thermal management, and overall reliability enhancement. Its usage is integral to ensuring the functionality and longevity of electronic devices across various industries and applications.
What industries commonly use potting compounds?
Potting compounds find applications across various industries due to their ability to encapsulate and protect electronic components from environmental factors such as moisture, dust, vibration, and thermal stress. Here are some industries where potting compounds are commonly used:
- Electronics:One of the primary users of potting compounds is the electronics industry. Potting compounds protect sensitive electronic components such as circuit boards, sensors, and connectors from moisture, corrosion, and mechanical damage. They ensure the longevity and reliability of electronic devices used in diverse applications ranging from consumer electronics to industrial automation.
- Automotive:In automotive manufacturing, potting compounds protect electronic control units (ECUs), sensors, and wiring harnesses from harsh operating conditions, including extreme temperatures, humidity, and vibration. These compounds enhance the durability and performance of automotive electronics, ensuring vehicle safety and reliability.
- Aerospace and Defense:Potting compounds are crucial in aerospace and defense applications where electronic systems operate in demanding environments such as high altitudes, fluctuating temperatures, and chemical exposure. They protect avionics, navigation systems, and communication equipment from the adverse effects of moisture, shock, and electromagnetic interference.
- Renewable Energy:The renewable energy sector, including solar and wind power generation, relies on potting compounds to safeguard electrical components like inverters, controllers, and sensors in renewable energy systems. These compounds help mitigate the impact of environmental factors, ensuring the efficient and reliable operation of renewable energy infrastructure.
- Medical Devices:Potting compounds manufacture medical devices to protect electronic components embedded in devices such as pacemakers, defibrillators, and diagnostic equipment. These compounds are essential for maintaining the integrity and functionality of medical electronics, particularly in environments where sterility and reliability are critical.
- Telecommunications:In telecommunications infrastructure, potting compounds protect sensitive electronic equipment like amplifiers, transceivers, and antennas from moisture, temperature variations, and physical damage. They ensure the robustness and longevity of telecommunications systems, supporting uninterrupted connectivity and data transmission.
Potting compounds are versatile materials widely used in industries ranging from electronics and automotive to aerospace, defense, renewable energy, medical devices, and telecommunications. Their ability to provide encapsulation and protection for electronic components makes them indispensable for ensuring reliability, durability, and performance across various applications.
Can potting compounds withstand extreme temperatures?
Potting compounds encapsulate electronic components, protecting them from environmental factors such as moisture, shock, and vibration. While the ability of potting compounds to withstand extreme temperatures depends on their composition and intended application, many potting compounds are formulated to offer thermal stability across a wide range of temperatures.
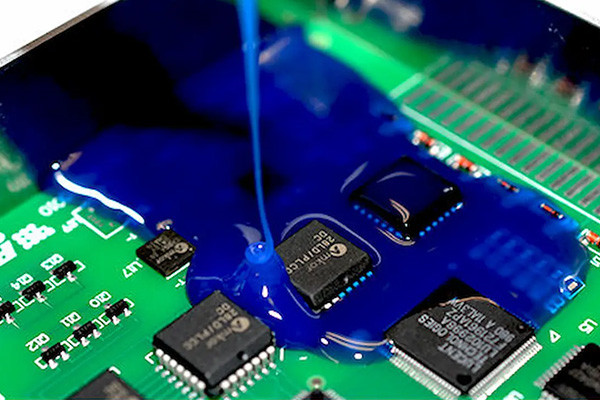
The thermal stability of potting compounds is typically determined by their glass transition temperature (Tg) and maximum operating temperature (Tm). The Tg is the temperature at which the material transitions from a rigid, glassy state to a softer, rubbery state. Potting compounds with higher Tg values can withstand higher temperatures without losing structural integrity. Tm refers to the temperature at which the material begins to degrade or lose its physical properties.
Specialized potting compounds are available for applications requiring resistance to extreme temperatures, such as those encountered in aerospace, automotive, and industrial environments. These compounds are often formulated using high-temperature-resistant resins like epoxy, silicone, or polyurethane. Epoxy potting compounds, for example, can typically withstand temperatures ranging from -40°C to over 200°C, depending on the specific formulation and curing process.
Silicone potting compounds are known for their excellent thermal stability, offering resistance to temperatures ranging from -50°C to 250°C or higher. Their flexibility and ability to maintain mechanical properties over a wide temperature range make them ideal for applications subjected to thermal cycling or fluctuating temperatures.
Polyurethane potting compounds exhibit good thermal stability, with operating temperatures typically ranging from -40°C to 150°C. Additionally, they offer excellent chemical resistance and mechanical properties, making them suitable for harsh environments.
In extreme temperature applications exceeding the capabilities of conventional potting compounds, specialty formulations using advanced materials such as ceramic-filled epoxies or thermally conductive silicones may be employed. These materials can withstand temperatures exceeding 300°C and offer enhanced thermal conductivity for improved heat dissipation.
Overall, while potting compounds can offer varying degrees of thermal stability, selecting the appropriate material depends on factors such as the application’s temperature range, required mechanical properties, and environmental conditions. Collaboration with material suppliers and thorough testing are essential to ensure the selected potting compound meets the application’s specific requirements.
Are potting compounds resistant to chemicals?
Potting compounds, commonly used in electronics and industrial applications, offer varying degrees of resistance to chemicals depending on their composition and intended use. These compounds encapsulate and protect electronic components, wires, and circuits from environmental factors such as moisture, vibration, and chemicals. Their chemical resistance is crucial for ensuring the longevity and reliability of the components they encase.
Potting compounds are typically formulated from epoxies, silicones, polyurethanes, and resins, each offering different chemical resistance properties. Epoxies, for instance, are known for their excellent resistance to various chemicals, including solvents, acids, and bases. Silicones exhibit good chemical resistance, particularly against moisture, oxidation, and different solvents. Polyurethanes, while offering good resistance to many chemicals, may not be as robust in harsh chemical environments as epoxies or silicones.
The chemical resistance of potting compounds is further influenced by factors such as curing mechanisms, filler materials, and additives. For example, compounds with a high filler content may offer enhanced resistance to certain chemicals due to the inert nature of the fillers, which act as barriers against chemical attack. Additionally, additives like corrosion inhibitors or flame retardants can impact the compound’s chemical resistance properties.
It’s essential to consider the specific chemicals a potting compound will be exposed to in its intended application. While many potting compounds offer general chemical resistance, some may be more specialized for particular environments. For instance, compounds in automotive electronics may need to withstand exposure to oils, fuels, and hydraulic fluids. In contrast, those used in aerospace applications may need to resist aviation fuels and hydraulic fluids.
When selecting a potting compound for a particular application, the chemical environment must be thoroughly considered. Manufacturers often provide data sheets detailing their products’ chemical resistance, helping engineers and designers make informed decisions to ensure the longevity and reliability of electronic components in various operating conditions.
How do potting compounds prevent moisture ingress?
Potting compounds encapsulate electronic components and devices, protecting environmental factors such as moisture, dust, vibration, and thermal shock. One of the primary functions of potting compounds is to prevent moisture ingress, which can cause corrosion, electrical shorts, and degradation of electronic components over time. There are several mechanisms through which potting compounds achieve this:
- Physical Barrier: Potting compounds form a physical barrier around the electronic components, sealing them from the external environment. These compounds typically have low permeability to moisture, preventing water molecules from penetrating the encapsulated space. This barrier effectively shields the sensitive electronic components from direct contact with moisture.
- Chemical Resistance: Many potting compounds are formulated to resist chemical reactions with water or other moisture-containing substances. They may contain additives or polymers that are inherently hydrophobic or chemically inert, making them less susceptible to degradation when exposed to moisture. This chemical resistance helps maintain the integrity of the potting material and prevents it from breaking down in the presence of water.
- Hydrophobic Properties: Some potting compounds possess hydrophobic properties, repelling water molecules. This property reduces the tendency of moisture to adhere to the surface of the encapsulated components, minimizing the risk of water ingress. Hydrophobicity can be achieved by using certain additives or selecting specific polymer formulations that inherently repel water.
- Curing Process: During the curing process, potting compounds undergo a chemical transformation, forming a solid, impermeable matrix around the electronic components. This cured matrix effectively seals the components, creating a barrier against moisture ingress. Proper curing conditions and techniques are essential to ensure the integrity and effectiveness of the encapsulation.
Overall, potting compounds prevent moisture ingress through physical barriers, chemical resistance, hydrophobic properties, and curing. By encapsulating electronic components in a protective shell, these compounds help extend the lifespan and reliability of electronic devices, especially in harsh or demanding environments where exposure to moisture is a concern.
What role does potting compound play in prolonging the lifespan of electronic devices?
Potting compound, a type of encapsulant material, plays a crucial role in prolonging the lifespan of electronic devices by providing protection against environmental factors, mechanical stress, and electrical hazards. Here’s how it achieves this:
- Environmental Protection: Electronic devices are often exposed to harsh environmental conditions such as moisture, dust, chemicals, and temperature fluctuations. Potting compound forms a protective barrier around sensitive electronic components, shielding them from these elements. By preventing moisture ingress, corrosion, and contamination, potting compound helps maintain the integrity and functionality of the electronics over time.
- Mechanical Protection: Electronic components are vulnerable to mechanical stress from vibration, shock, and impact, especially in industrial or automotive applications. Potting compound encapsulates the components, dampening mechanical forces and providing structural support. This reduces the risk of physical damage and extends the device’s operational lifespan in demanding environments.
- Thermal Management: Heat dissipation is critical for the performance and reliability of electronic devices. Potting compounds with thermal conductive properties can efficiently transfer heat away from sensitive components, preventing overheating and thermal degradation. By maintaining optimal operating temperatures, potting compound contributes to the longevity of electronic devices.
- Electrical Insulation: Potting compound acts as an electrical insulator, preventing short circuits and electrical failures caused by contact with conductive materials or moisture. By isolating components from external electrical sources and reducing the risk of electrical arcing or leakage, potting compound ensures the safe and reliable operation of electronic devices over time.
- Shock and Vibration Resistance: In applications where electronic devices are subjected to constant vibration or mechanical shock, potting compound provides an additional layer of protection. By securing components in place and absorbing kinetic energy, potting compound minimizes the risk of component displacement or damage, thereby enhancing the durability and lifespan of the device.
In summary, potting compound plays a multifaceted role in safeguarding electronic devices against environmental hazards, mechanical stress, electrical issues, and thermal challenges. By providing robust protection and ensuring reliable performance, potting compound significantly contributes to prolonging the lifespan of electronic devices in various industrial, automotive, aerospace, and consumer applications.
What role does potting compound play in prolonging the lifespan of electronic devices?
Potting compound, a type of encapsulant material, plays a crucial role in prolonging the lifespan of electronic devices by protecting against environmental factors, mechanical stress, and electrical hazards. Here’s how it achieves this:
- Environmental Protection: Electronic devices are often exposed to harsh environmental conditions such as moisture, dust, chemicals, and temperature fluctuations. Potting compound forms a protective barrier around sensitive electronic components, shielding them from these elements. By preventing moisture ingress, corrosion, and contamination, the potting compound helps maintain the integrity and functionality of the electronics over time.
- Mechanical Protection: Electronic components are vulnerable to mechanical stress from vibration, shock, and impact, especially in industrial or automotive applications. Potting compound encapsulates the components, dampening mechanical forces and providing structural support. This reduces the risk of physical damage and extends the device’s operational lifespan in demanding environments.
- Thermal Management: Heat dissipation is critical for the performance and reliability of electronic devices. Potting compounds with thermal conductive properties can efficiently transfer heat away from sensitive components, preventing overheating and thermal degradation. By maintaining optimal operating temperatures, potting compound contributes to the longevity of electronic devices.
- Electrical Insulation: A potting compound acts as an insulator, preventing short circuits and electrical failures caused by contact with conductive materials or moisture. By isolating components from external electrical sources and reducing the risk of electrical arcing or leakage, potting compound ensures electronic devices’ safe and reliable operation over time.
- Shock and Vibration Resistance: In applications where electronic devices are subjected to constant vibration or mechanical shock, the potting compound provides an additional layer of protection. By securing components in place and absorbing kinetic energy, the potting compound minimizes the risk of component displacement or damage, thereby enhancing the device’s durability and lifespan.
potting compound plays a multifaceted role in safeguarding electronic devices against environmental hazards, mechanical stress, electrical issues, and thermal challenges. By providing robust protection and ensuring reliable performance, potting compound significantly prolongs the lifespan of electronic devices in various industrial, automotive, aerospace, and consumer applications.
Can potting compounds enhance the mechanical stability of electronic assemblies?
Potting compounds play a vital role in enhancing the mechanical stability of electronic assemblies. These compounds are typically resins or gels poured or injected into electronic devices to encapsulate delicate components, providing structural support and protection against environmental factors. Here’s how they contribute to mechanical stability:
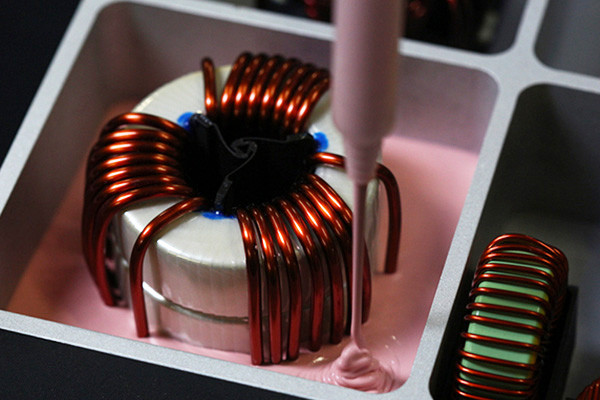
- Shock and Vibration Resistance: Electronic assemblies are often subjected to mechanical stresses, including shock and vibration, during handling, transportation, or operation. Potting compounds act as cushioning material, absorbing and dissipating the energy generated from these mechanical forces. By encapsulating the components within a solid matrix, potting compounds prevent them from shifting or vibrating excessively, thus reducing the risk of damage due to mechanical stress.
- Prevention of Moisture and Contaminant Ingress: Moisture, dust, and other contaminants can infiltrate electronic assemblies, leading to corrosion, short circuits, and other reliability issues. Potting compounds create a protective barrier around the components, sealing them from external elements. This barrier not only enhances mechanical stability by preventing movement but also ensures the longevity and reliability of the electronic device by safeguarding it against environmental factors.
- Improved Structural Integrity: Some electronic assemblies may have components mounted on flexible substrates or thin PCBs, making them susceptible to bending or flexing under mechanical loads. Potting compounds encapsulate these components, providing additional structural support and rigidity to the assembly. This reinforcement helps maintain the desired shape and alignment of the components, particularly in applications where dimensional stability is critical.
- Thermal Management: Many potting compounds exhibit excellent thermal conductivity properties, facilitating the efficient dissipation of heat generated by electronic components during operation. By dissipating heat effectively, these compounds help prevent overheating, which can lead to thermal expansion and mechanical stress within the assembly. This thermal management capability further contributes to the electronic device’s overall mechanical stability and reliability.
Potting compounds play a crucial role in enhancing the mechanical stability of electronic assemblies by providing shock and vibration resistance, preventing moisture and contaminant ingress, improving structural integrity, and aiding in thermal management. Their use ensures that electronic devices can withstand mechanical stresses and environmental conditions, enhancing their reliability and longevity.
What types of electronic components are typically potted?
Potting is a process in electronics manufacturing where electronic components or assemblies are encapsulated in a protective material, typically a resin or polymer compound. This encapsulation protects against environmental factors such as moisture, dust, vibration, and shock. Various electronic components may undergo potting to enhance their durability and reliability in harsh operating conditions. Here are some common types of electronic components that are typically potted:
- Printed Circuit Boards (PCBs): Entire PCBs or specific areas containing sensitive components like microcontrollers, integrated circuits, and connectors may be potted to safeguard them from environmental stressors.
- Transformers and Inductors: These components are often potted to insulate windings and cores, preventing moisture ingress and improving electrical insulation properties.
- Capacitors and Resistors: Potting can enhance the longevity and reliability of these passive components by shielding them from corrosive agents and mechanical damage.
- Sensors: Potting protects sensors such as temperature sensors, pressure sensors, and proximity sensors from exposure to moisture, chemicals, and mechanical stress, ensuring accurate and reliable operation.
- Connectors and Contacts: Potting connector interfaces and contacts can prevent corrosion and ensure stable electrical connections, particularly in outdoor or corrosive environments.
- Power Supplies and Modules: Potting is commonly employed in encapsulating power supplies, voltage regulators, and other electronic modules to enhance thermal conductivity, mechanical stability, and resistance to environmental hazards.
- LEDs (Light-Emitting Diodes): Potting LED assemblies can improve their resistance to vibration, shock, and moisture, extending their operational lifespan in outdoor or industrial applications.
- Coils and Solenoids: Potting provides mechanical support and environmental protection for coils and solenoids, often used in electromechanical devices and systems.
- Relays and Switches: Potting relay and switch assemblies can improve their resistance to moisture, dust, and mechanical stress, ensuring reliable switching operations in various applications.
- Integrated Circuit (IC) Packages: While ICs are typically sealed within their packages, potting may be applied in specialized applications where additional protection is required, such as aerospace or automotive electronics.
Overall, potting plays a crucial role in enhancing electronic components’ durability, reliability, and performance across a wide range of industries and applications, from consumer electronics to industrial automation and beyond.
Are there different formulations of potting compounds available?
Yes, a wide range of formulations are available for potting compounds, each tailored to specific application requirements and environmental conditions. Potting compounds encapsulate electronic components, protecting them from moisture, vibration, thermal cycling, and other potentially damaging factors. Here are some standard formulations:
- Epoxy Resins: Epoxy potting compounds offer excellent adhesion, chemical resistance, and mechanical strength. They can be formulated with various additives to modify flexibility, thermal conductivity, and flame retardancy.
- Polyurethanes: Polyurethane potting compounds provide good flexibility and resistance to vibration, making them suitable for applications where thermal cycling and mechanical stress are concerns. They also offer good adhesion to a variety of substrates.
- Silicone Rubbers: Silicone potting compounds offer exceptional thermal stability, comprehensive temperature range performance, and excellent electrical insulation properties. They are often chosen for high-temperature applications and harsh environmental conditions.
- Acrylics: Acrylic potting compounds offer fast curing times and good adhesion to various substrates. They are often used in applications requiring rapid processing or resistance to moisture and chemicals is essential.
- Polyesters: Polyester potting compounds offer good electrical insulation properties and resistance to moisture and chemicals. They can be formulated to provide different levels of hardness and flexibility.
- Hybrid Formulations: Some potting compounds combine properties of two or more resin types to achieve specific performance requirements. For example, epoxy-polyurethane hybrids may balance epoxies’ mechanical strength and the polyurethanes’ flexibility.
- Thermally Conductive Compounds: Thermally conductive potting compounds are available for heat dissipation applications. These formulations typically contain additives such as ceramics or metallic fillers to enhance thermal conductivity while providing the necessary encapsulation properties.
The choice of potting compound depends on factors such as the specific application requirements, environmental conditions, desired properties (e.g., flexibility, thermal conductivity), and processing considerations. It’s essential to select a formulation that best meets the needs of the intended application to ensure optimal performance and reliability.
How are potting compounds applied?
Potting compounds encapsulate electronic components, such as circuits, sensors, or transformers, protecting environmental factors like moisture, vibration, and thermal shock. They are applied using various techniques tailored to the application’s specific needs.
One standard method is manual potting, where the compound is mixed according to manufacturer specifications and poured or injected around the electronic components. This method offers flexibility in handling different shapes and sizes of components but can be labor-intensive and may lead to consistency in coverage.
Another approach is automated potting, which involves using machinery to accurately and efficiently dispense the compound. Automated systems can control temperature, pressure, and curing time, ensuring consistent results and higher production rates. Dispensing methods include meter-mix dispensing, where two or more compound components are mixed in precise ratios before application, and vacuum potting, which removes air bubbles from the mixture for better insulation properties.
Sometimes, potting compounds are applied using casting techniques, where the components are placed in a mold, and the compound is poured over them. This method is suitable for mass production and allows for complex shapes and configurations. It requires careful mold design to prevent voids and ensure proper encapsulation.
Thermally conductive or electrically insulating potting compounds are available for applications requiring enhanced thermal conductivity or electrical insulation. To achieve the desired properties, these materials typically contain fillers such as ceramics or metallic particles. Specialized techniques may be necessary to ensure an even distribution of fillers and maximize performance.
After application, the potting compound undergoes curing, solidifying, and forming a protective barrier around the components. Curing methods vary depending on the compound and may involve exposure to heat, UV light, or chemical reactions. Proper curing is essential for achieving the encapsulation’s desired mechanical and electrical properties.
Potting compounds are applied using manual or automated techniques tailored to the specific application requirements. Factors such as component size, shape, desired properties, and production volume influence the application method and equipment choice. Careful attention to mixing, dispensing, and curing processes is crucial to ensure the reliability and performance of the encapsulated electronic devices.
What are the key considerations when selecting a potting compound?
A suitable potting compound ensures electronic components’ long-term performance and reliability, particularly in harsh environments. Several key considerations should be taken into account:
- Chemical Compatibility: The potting compound must be compatible with the materials it will contact, including the electronic components, circuit board materials, and any other substrates. Chemical incompatibility can lead to degradation or failure of the components.
- Environmental Resistance: Consider the environmental conditions the potting compound will be exposed to, such as temperature extremes, moisture, chemicals, and UV radiation. Choose a compound with appropriate resistance to these factors to ensure the stability and longevity of the encapsulated components.
- Mechanical Properties: The potting compound should protect against mechanical stresses, such as vibration, shock, and impact. It should also maintain adhesion to the components and substrates to prevent delamination or cracking.
- Electrical Insulation: Ensure the potting compound has high dielectric strength and insulation resistance to avoid electrical leakage or short circuits. This is especially important for applications where electrical isolation is critical.
- Thermal Conductivity: Consider the thermal management requirements of the electronic components. Choose a potting compound with appropriate thermal conductivity to dissipate heat effectively and prevent overheating, which can degrade component performance and reliability.
- Curing Properties: Evaluate the curing characteristics of the potting compound, including cure time, temperature requirements, and pot life. Select a compound that can be processed efficiently within the manufacturing environment while providing adequate time for proper application and curing.
- Application Method: Consider the application method, whether it’s manual dispensing, automated dispensing, or casting. Choose a potting compound compatible with the selected application method to ensure uniform coverage and minimal voids or air entrapment.
- Regulatory Compliance: Ensure that the potting compound meets relevant industry standards and regulatory requirements, such as RoHS (Restriction of Hazardous Substances) compliance, UL (Underwriters Laboratories) certification, or specific industry standards for performance and safety.
By carefully considering these factors, engineers can select a potting compound that provides optimal protection and performance for their electronic assemblies, ensuring reliability and longevity in various operating environments.
Can potting compounds be removed or reworked?
Potting compounds, often used in electronics and electrical applications, are materials designed to encapsulate components to protect them from environmental factors like moisture, vibration, and shock. While potting compounds are typically chosen for their durability and stability, there are circumstances where removal or rework may be necessary.
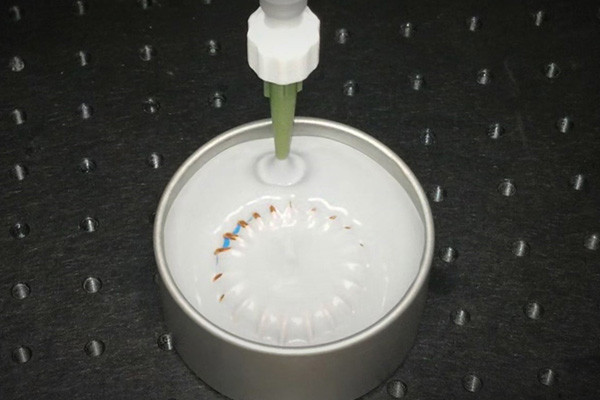
Removing or reworking potting compounds can be a challenging task due to their intended permanence and the potential damage to underlying components. However, it is possible with the proper techniques and tools.
One method for removing potting compounds involves mechanical means such as scraping, grinding, or milling. This approach is labor-intensive and risks damaging delicate components. Another option is to use chemical solvents specifically formulated to dissolve the potting material without harming the components. Solvent-based removal requires careful consideration of compatibility with the potting compound and its encapsulated materials.
In some cases, localized heating can soften the potting compound, making it easier to remove. However, excessive heat can damage sensitive components or trigger chemical reactions in the potting material, leading to undesirable byproducts or fumes.
Reworking potting compounds often involves replacing damaged or faulty components without compromising the integrity of the encapsulation. This may require precise cutting or drilling to access the targeted area, followed by careful removal and replacement of the affected parts. After rework, the encapsulated assembly must be resealed effectively to maintain its protective properties.
The decision to remove or rework potting compounds should consider factors such as the extent of damage, the availability of alternative solutions, and the cost-effectiveness of the process. Additionally, safety precautions must be observed, mainly when dealing with chemical solvents or heat sources.
While potting compounds are designed for permanence, they can be removed or reworked using various techniques. However, these processes require careful planning, specialized equipment, and expertise to avoid damage to components and ensure the integrity of the encapsulated assembly.
Are there environmental concerns associated with potting compounds?
Potting compounds, commonly used in electronics and electrical applications to encapsulate or protect components, can indeed pose environmental concerns. These concerns typically revolve around the compounds’ materials, manufacturing processes, and end-of-life disposal.
One significant issue is the potential presence of hazardous chemicals in potting compounds. Some formulations may contain volatile organic compounds (VOCs), which can contribute to air pollution and have adverse health effects. Additionally, certain compounds may include plasticizers or flame retardants that can harm human health and the environment.
Another environmental concern is the energy and resources required for manufacturing potting compounds. The production process often involves using fossil fuels, electricity, and water, leading to greenhouse gas emissions and depletion of natural resources. Furthermore, extracting and processing raw materials used in these compounds can contribute to habitat destruction and ecosystem degradation.
Disposal of potting compounds at the end of their life cycle also poses challenges. Many potting compounds are not biodegradable and may persist in the environment for extended periods. Improper disposal methods, such as landfilling or incineration, can release toxic substances into soil, water, and air, further exacerbating environmental pollution.
To address these concerns, efforts are underway to develop more environmentally friendly alternatives to traditional potting compounds. This includes the use of bio-based or renewable materials, as well as formulations with reduced toxicity and improved biodegradability. Manufacturers also explore methods to optimize production processes to minimize energy consumption and waste generation.
Regulatory bodies and industry standards play a crucial role in mitigating the environmental impact of potting compounds. Regulations such as the Restriction of Hazardous Substances (RoHS) directive in the European Union restrict the use of certain hazardous substances in electronics, influencing the composition of potting compounds.
While potting compounds offer valuable protection for electronic components, they can pose environmental challenges due to their chemical composition, manufacturing processes, and disposal methods. Addressing these concerns requires collaboration among manufacturers, regulators, and other stakeholders to promote sustainable practices throughout the product life cycle.
How do potting compounds contribute to electrical insulation?
Potting compounds provide electrical insulation in various applications, particularly electronics and electrical systems. These compounds are specially formulated materials designed to encapsulate electronic components, providing mechanical support, environmental protection, and, most importantly, electrical insulation.
One primary way potting compounds contribute to electrical insulation is through their dielectric properties. Dielectric materials do not readily conduct electricity, making them ideal for insulating purposes. Potting compounds are formulated to have high dielectric strength, which means they can withstand high voltage without conducting electricity. This property is essential for preventing electrical current from flowing between conductive elements, thus insulating the system.
Potting compounds also provide a physical barrier between conductive components. Potting compounds prevent moisture, dust, and other contaminants from reaching sensitive electrical components by encapsulating electronic parts within a solid material. These contaminants can cause short circuits or degrade insulation over time, leading to electrical failures. By sealing off components, potting compounds enhance the reliability and longevity of electrical systems.
Furthermore, potting compounds offer excellent thermal insulation properties. Electronic components can generate heat during operation, and excessive heat can degrade insulation materials and affect performance. Potting compounds with high thermal resistance help dissipate heat efficiently, maintaining a stable operating temperature for electronic devices. This thermal insulation not only protects against overheating but also contributes to the overall insulation integrity of the system.
Another way potting compounds contribute to electrical insulation is by providing structural support. Encapsulating fragile electronic components in a sturdy material helps prevent mechanical damage due to vibrations, shocks, or impacts. This structural reinforcement ensures that electrical connections remain intact and insulated even under harsh operating conditions, enhancing the system’s overall reliability.
Potting compounds contribute to electrical insulation through their dielectric, physical, thermal, and structural properties. By encapsulating electronic components, these compounds prevent electrical current leakage, protect against environmental hazards, dissipate heat, and provide mechanical support, thereby ensuring the integrity and reliability of electrical systems in various applications.
Can potting compounds be used for outdoor applications?
Potting compounds are versatile materials commonly used in various industries to encapsulate and protect electronic components. While many potting compounds are suitable for indoor applications, there are formulations specifically designed to withstand outdoor conditions.
When selecting a potting compound for outdoor use, several factors need consideration:
- Weather Resistance: Outdoor environments expose materials to harsh conditions such as sunlight, moisture, temperature fluctuations, and pollutants. Potting compounds for outdoor applications are formulated to resist UV degradation, preventing the encapsulated components’ yellowing, cracking, or weakening over time.
- Waterproofing: Outdoor electronics are vulnerable to water ingress, which can lead to corrosion and malfunction. Potting compounds with high water resistance prevent moisture from penetrating the encapsulated components, ensuring long-term reliability.
- Temperature Stability: Outdoor temperatures vary widely, from extreme heat to cold. Potting compounds should maintain their physical and electrical properties across this range to protect the enclosed electronics effectively.
- Chemical Resistance: Exposure to chemicals present in outdoor environments, such as pollutants or cleaning agents, can degrade conventional potting materials. Outdoor-grade potting compounds are engineered to withstand these chemical exposures, ensuring the integrity of the encapsulated electronics.
- Mechanical Strength: Outdoor applications may subject encapsulated components to mechanical stresses, including vibrations and impacts. Potting compounds with high mechanical strength provide robust protection against such forces, preventing damage to the electronics.
- Longevity: Outdoor electronics often require extended service life. Potting compounds should be durable enough to maintain their protective properties for years, ensuring the reliability of the encapsulated components over the product’s lifespan.
Potting compounds are commonly used outdoors in LED lighting systems, solar panels, outdoor sensors, and automotive electronics. Manufacturers offer a variety of specialized formulations tailored to specific outdoor requirements, allowing designers to select the most suitable potting compound for their application.
Potting compounds can be used for outdoor applications when chosen appropriately for the specific environmental conditions and performance requirements. With the correct formulation, potting compounds provide reliable protection and ensure the longevity of outdoor electronic devices.
What advancements have been made in potting compound technology?
Potting compounds, used to encapsulate electronic components for protection against environmental factors, have seen significant advancements in recent years.
One key area of progress is in material formulation. Manufacturers are developing compounds with enhanced thermal conductivity to dissipate heat more effectively, thus improving the reliability and longevity of electronic devices. These advanced materials also offer better resistance to chemicals, moisture, and other environmental stressors, ensuring prolonged durability in harsh conditions.
Moreover, innovations in the curing process have introduced faster curing compounds that reduce production time and costs. Some formulations now feature UV or moisture cure mechanisms, enabling rapid solidification without high-temperature ovens.
Furthermore, advancements in nanotechnology have led to the development of nano-filled potting compounds. These nanocomposites offer superior mechanical strength and electrical insulation properties while maintaining flexibility, making them ideal for demanding aerospace, automotive, and military applications.
In terms of application techniques, automated dispensing systems have become more precise and efficient, allowing for consistent and uniform coverage of components with minimal material waste. Additionally, manufacturers are exploring additive manufacturing techniques to customize potting solutions for complex geometries, further expanding their applicability across diverse industries.
Overall, these advancements in potting compound technology are driving improvements in electronic device reliability, performance, and miniaturization, paving the way for more robust and resilient products in an increasingly interconnected world.
Are there alternatives to potting compounds for encapsulating electronic components?
Yes, there are several alternatives to traditional potting compounds for encapsulating electronic components, each with its advantages and applications:
- Conformal Coatings: These are thin protective coatings applied directly onto the surface of electronic assemblies. They provide excellent protection against moisture, dust, chemicals, and temperature extremes while still allowing for inspection and repair of components. Common materials include acrylics, silicones, urethanes, and epoxies.
- Encapsulation by Moldinginvolves encapsulating electronic components within a solid plastic material using injection molding or transfer molding techniques. The encapsulation material can be selected based on desired properties such as flexibility, thermal conductivity, or resistance to specific environmental conditions.
- Gel Encapsulation: Gel encapsulants are soft, flexible materials with excellent shock absorption and vibration-dampening properties. They are often used in applications where mechanical stress or movement is a concern, such as automotive electronics or ruggedized devices.
- Potting Gels: These are similar to traditional potting compounds but are formulated as soft, flexible gels rather than hard, rigid resins. Potting gels offer the advantage of being reworkable, allowing for easier removal and replacement of components if needed.
- Encapsulation with Foam-in-Place Materials: Foam-in-place materials expand to fill voids and conform to the shape of electronic assemblies, providing excellent protection against shock and vibration. They can be applied manually or using automated dispensing equipment, offering good thermal insulation properties.
- Encapsulation with Encapsulant Films: Thin films of encapsulant material can be laminated onto electronic assemblies to protect against moisture, dust, and mechanical damage. Encapsulant films offer the advantage of being lightweight and flexible, making them suitable for applications where space and weight are critical considerations.
Each of these alternatives offers unique benefits depending on the specific requirements of the electronic application, such as environmental conditions, mechanical stresses, reworkability, and cost constraints. By carefully selecting the appropriate encapsulation method and material, engineers can ensure electronic assemblies’ long-term reliability and performance in a wide range of operating environments.
Conclusion:
Potting compounds are indispensable in safeguarding electronic components against various environmental challenges, ensuring the reliability and longevity of devices across numerous industries. From enhancing mechanical stability to providing electrical insulation, these compounds continue to evolve, meeting the demands of modern electronics while contributing to advancements in technology and innovation.
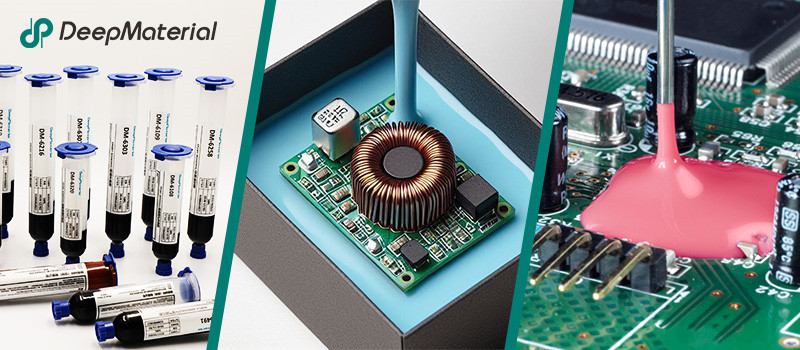
About DeepMaterial
DeepMaterial is a trusted supplier of encapsulant materials that are used in electronics manufacturing worldwide. From chip on board encapsulants such as glob top material to conformal coatings, underfills, low pressure molding, and potting solutions, DeepMaterial offers a full range of circuit board protection materials that effectively protect circuit boards while help reduce costs. More…Deepmaterial is a the manufacturer of epoxy adhesives including hardeners, metalbond, and metal filled resins. Structural, toughened medium viscosity, and non-sag adhesives are also offered. Some adhesives are resistant to thermal shock, chemical, vibration dampening, and impact. Suitable for metals, plastics, wood, and ceramics. Serves electronics, aerospace, automotive, tooling, marine, and construction industries. REACH and RoHS compliant. FDA approved. UL listed. Meets military specifications. We are the one of best adhesive manufacturers in China.
Blogs & News
Potting compounds are at the frontline of electronics assembly, delivering effective protection in challenging environmental conditions while improving mechanical strength and offering high electric insulation. Used within a variety of industries, electrical potting compounds are found within a broad range of consumer electronics, as well as used in applications across the automotive, aerospace, and other industries where electronic assemblies are prevalent.
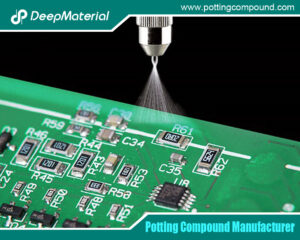
The Ultimate Guide to Electrical Potting Compound and Market Application
The Ultimate Guide to Electrical Potting Compound and Market Application In the modern world of electronics, where devices are increasingly compact and exposed to harsh
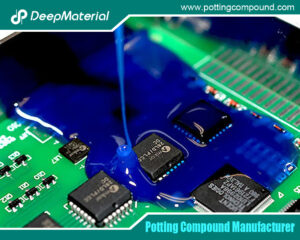
The Top Polyurethane Potting Compound
The Top Polyurethane Potting Compound In the fast-evolving world of electronics and industrial manufacturing, protecting sensitive components from environmental hazards is critical to ensuring reliability
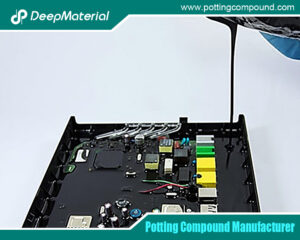
Advanced Epoxy Potting Compound for Superior Electronic Protection
Advanced Epoxy Potting Compound for Superior Electronic Protection In the realm of electronics and industrial manufacturing, protecting sensitive components from environmental hazards is critical to
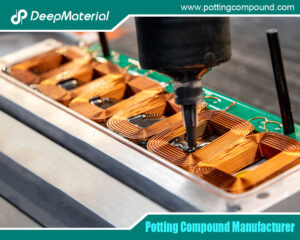
Waterproof Potting Compound: A Comprehensive Guide
Waterproof Potting Compound: A Comprehensive Guide In today’s technology-driven world, protecting sensitive electronic components from environmental hazards is paramount. One of the most effective solutions
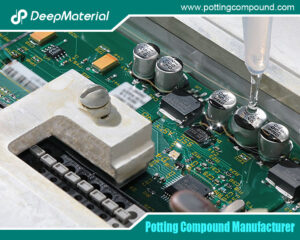
Silicone Potting Compound for Electronics
Silicone Potting Compound for Electronics In the rapidly evolving world of electronics, ensuring the reliability, durability, and performance of electronic components is paramount. One critical
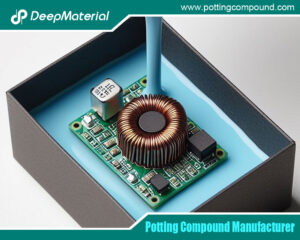
Potting Compound vs. Epoxy: A Comprehensive Comparison
Potting Compound vs. Epoxy: A Comprehensive Comparison In the world of electronics, manufacturing, and material encapsulation, two terms frequently come up: potting compounds and epoxy.