What is the difference between potting and conformal coating
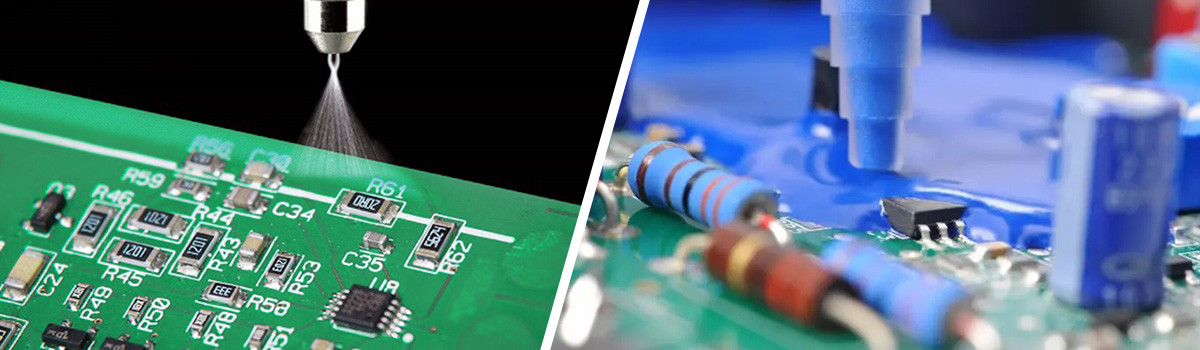
In the realm of electronics manufacturing and assembly, protective measures are paramount to ensure longevity and reliability of components. Two common methods employed for safeguarding electronic devices against environmental hazards are potting and conformal coating. While both techniques serve the purpose of protection, they differ significantly in their application, materials used, and effectiveness in various scenarios. Understanding the disparities between potting and conformal coating is crucial for selecting the most suitable method for a particular application. Let’s delve into the nuances of each technique through the following questions.
Table of Contents
Toggle20 Key Facts You Need to Grasp:
What are potting and conformal coating?
Potting and conformal coating are two standard methods used in electronic and electrical industries to protect components from environmental factors such as moisture, dust, chemicals, and physical damage. While both techniques safeguard sensitive electronic parts, they differ in their application methods and materials.
Potting involves encapsulating electronic components or circuitry in a protective compound, typically a liquid resin or gel-like material, to create a solid barrier around them. The process begins by placing the electronic assembly into a mold or container and pouring the potting compound over the assembly. The compound then cures and hardens, forming a robust protective layer that encases the components entirely. Potting provides excellent protection against moisture, vibration, and mechanical stress. It is ideal for applications where components are subjected to harsh conditions, such as automotive electronics, outdoor equipment, and industrial machinery.
Conversely, conformal coating involves applying a thin protective film over the surface of electronic assemblies. Unlike potting, the conformal coating does not completely encapsulate the components. Instead, it forms a conformal layer that adheres to the PCB (Printed Circuit Board) contours and components. Conformal coatings are typically applied using methods such as spraying, dipping, or brushing, and they come in various types, such as acrylics, silicones, polyurethanes, and epoxies. Each type offers specific properties suited to different environmental conditions and performance requirements. Conformal coatings protect against moisture, dust, corrosion, and chemical exposure while allowing for the inspection and repair of components when necessary. They are commonly used in consumer electronics, aerospace, military, and medical devices.
Potting involves completely encapsulating electronic components in a solid protective compound, whereas conformal coating entails applying a thin protective film over the surface of electronic assemblies. Both techniques play crucial roles in extending the lifespan and reliability of electronic devices by shielding them from environmental hazards. The choice between potting and conformal coating depends on factors such as the level of protection required, the application environment, and the accessibility of components for maintenance and repair.
How are potting and conformal coating used in electronic manufacturing?
Potting and conformal coating are two essential techniques in electronic manufacturing that protect electronic components and assemblies from environmental factors such as moisture, dust, chemicals, and mechanical stress.
Potting involves encapsulating electronic components or assemblies within a protective compound, typically a resin, to shield them from environmental hazards. This process begins by placing the electronic components into a mold or container and pouring the liquid resin around them. Once cured, the resin forms a solid protective barrier, sealing the components from external elements. Potting protects against moisture, vibration, and thermal shock, making it ideal for applications exposed to harsh environments, such as automotive electronics, outdoor equipment, and industrial machinery.
Conversely, conformal coating involves applying a thin protective layer of material, typically a polymer, directly onto the surface of printed circuit boards (PCBs) and electronic assemblies. Unlike potting, the conformal coating does not completely encapsulate the components. Instead, it forms a conformal layer that adheres to the contours of the PCB, providing a protective barrier while still allowing for inspection and maintenance. Conformal coatings offer resistance to moisture, chemicals, dust, and temperature fluctuations, enhancing the reliability and lifespan of electronic devices. They are commonly used in consumer electronics, aerospace, medical devices, and military applications.
Both potting and conformal coating enhance electronic products’ durability, reliability, and longevity, ensuring they can withstand the rigors of their intended environments. The choice between potting and conformal coating depends on factors such as the level of protection required, ease of application, access to components for maintenance, and cost considerations. Manufacturers often evaluate these factors alongside the specific requirements of their products to determine the most suitable protective solution. In some cases, a combination of potting and conformal coating may be employed to achieve optimal protection for critical electronic assemblies.
What are the primary purposes of potting and conformal coating?
Potting and conformal coating are two standard techniques in electronics manufacturing to protect electronic components and assemblies from various environmental factors and mechanical stresses. While they serve similar overarching purposes of safeguarding electronics, they have distinct applications and benefits.
Potting involves encapsulating electronic components or assemblies within a solid or semi-solid material, typically epoxy resin or silicone rubber. The primary purposes of potting include:
- Environmental Protection: Potting materials create a barrier against moisture, dust, chemicals, and other environmental contaminants that could degrade or damage electronic components.
- Mechanical Protection: Potting adds structural integrity to electronic assemblies, protecting them from physical shocks, vibrations, and mechanical stresses encountered during handling, shipping, or operation.
- Electrical Insulation: Potting materials often possess insulating properties, preventing electrical shorts and enhancing the electrical insulation of the encase components.
- Thermal Management: Some potting materials have thermal conductivity properties, helping dissipate heat generated by electronic components, thus enhancing their reliability and performance.
Conformal Coating: Conformal coating involves applying a thin protective film over electronic assemblies, typically acrylic, silicone, urethane, or epoxy. The primary purposes of conformal coating include:
- Environmental Protection: Similar to potting, conformal coating protects electronic components from moisture, dust, chemicals, and other environmental contaminants, albeit with a thinner layer.
- Electrical Insulation: Conformal coatings provide a dielectric barrier between conductive components and the surrounding environment, reducing the risk of electrical shorts and improving reliability.
- Corrosion Resistance: Many conformal coatings offer excellent corrosion resistance, which is crucial for electronics operating in harsh or corrosive environments.
- Improved Reliability: By shielding components from environmental stressors, conformal coatings can extend the operational lifespan of electronic assemblies and reduce the likelihood of premature failure.
While both potting and conformal coating protect electronic components, potting provides a more robust encapsulation suitable for harsh environments and mechanical stresses. In contrast, conformal coating offers a thinner, more flexible protection suitable for assemblies requiring easier maintenance or inspection access. Both techniques enhance electronic devices’ reliability, durability, and performance in various applications.
How do potting and conformal coating protect electronic components?
Potting and conformal coating are two common methods for protecting electronic components from environmental factors such as moisture, dust, chemicals, and mechanical stress.
Potting involves encapsulating the electronic component in a protective material, usually a resin or silicone compound. This material surrounds the component, forming a solid barrier that seals it from the external environment. The potting material provides physical protection against impact and vibration and insulation against electrical hazards. It also helps dissipate heat generated by the component, thus preventing overheating. Potting is commonly used in applications where the electronic device is exposed to harsh conditions, such as outdoor environments or industrial settings.
Conversely, conformal coating involves applying a thin layer of protective material directly onto the surface of the electronic component. This coating conforms to the contours of the element, covering it with a protective film. Conformal coatings are typically made from acrylics, silicones, or urethanes. They provide a barrier against moisture, dust, and chemical contaminants while allowing for flexibility and movement of the component. Conformal coatings are often used in electronics that require protection but must also maintain accessibility for repairs or modifications.
Both potting and conformal coating protect electronic components by creating barriers preventing harmful substances’ ingress. Sealing the components reduces the risk of corrosion, short circuits, and other damage when exposed to adverse environmental conditions. Additionally, they help improve the reliability and longevity of electronic devices, reducing the need for maintenance and repairs. However, selecting the appropriate method and materials based on the application’s specific requirements is essential to ensure adequate protection without compromising functionality or performance.
What types of materials are used for potting and conformal coating?
Potting and conformal coating are essential in electronics manufacturing and assembly, protecting against environmental factors such as moisture, dust, chemicals, and mechanical stress. Various materials are employed for these purposes, each with distinct properties and suitability for different applications.
- Epoxy Resins: Epoxy resins are widely used in potting and conformal coating due to their excellent adhesion, chemical resistance, and mechanical properties. They provide robust protection against moisture and vibration, making them suitable for harsh environments. To enhance thermal conductivity and mechanical strength, epoxy resins can be filled with additives such as silica or ceramics.
- Silicone: Silicone-based materials offer flexibility, high-temperature resistance, and excellent electrical insulation properties. Silicone conformal coatings help protect sensitive electronic components exposed to extreme temperatures or thermal cycling. They also provide good resistance to moisture and chemicals.
- Polyurethanes: Polyurethane potting compounds and conformal coatings offer a balance of properties, including flexibility, chemical resistance, and good adhesion to various substrates. They are often chosen for applications requiring moderate protection, and some flexibility is desired to accommodate mechanical stresses.
- Acrylics: Acrylic-based materials are known for their transparency, UV resistance, and ease of application. Acrylic conformal coatings provide good moisture resistance and electrical insulation. They are commonly used in consumer electronics and applications where transparency is essential, such as LED displays.
- Parylene: Parylene coatings are deposited as thin, uniform layers through vapor deposition. Parylene offers excellent protection against moisture, chemicals, and electrical insulation while maintaining optical clarity without adding significant weight or bulk to the coated components. It is often used in medical devices and aerospace applications.
- Fluoropolymers: Fluoropolymer coatings, such as PTFE (Teflon), offer exceptional chemical resistance and low friction properties. While less common in potting applications due to their low adhesion, they are used in conformal coatings for specialized applications where extreme chemical resistance or non-stick properties are required.
The appropriate material for potting and conformal coating depends on environmental conditions, desired performance characteristics, regulatory requirements, and cost considerations. Each material type has its advantages and limitations, and manufacturers must carefully evaluate these factors to ensure the reliability and longevity of electronic assemblies.
What are the differences in application methods between potting and conformal coating?
Potting and conformal coating are two standard methods used in electronic manufacturing for protection against environmental factors such as moisture, dust, chemicals, and mechanical stress. While both techniques safeguard electronic components, they differ significantly in their application methods and the level of protection they offer.
Potting involves encapsulating electronic components entirely within a protective compound or resin. This compound, typically a thermosetting plastic or epoxy, is poured or injected around the components, completely encasing them. Potting provides robust protection by forming a solid barrier against moisture, dust, and other contaminants. It also enhances mechanical strength, vibration resistance, and thermal conductivity. However, due to the permanent encapsulation of components, potting can be challenging to rework or repair.
Conversely, conformal coating involves applying a thin protective layer of material onto the surface of printed circuit boards (PCBs) and electronic assemblies. This coating material, which could be silicone, acrylic, epoxy, or polyurethane, conforms to the contours of the PCB, covering components and traces without encapsulating them fully. Conformal coating offers excellent protection against moisture, dust, and chemical exposure while allowing for easy inspection and rework if necessary. It provides flexibility and is suitable for periodic maintenance or component replacement assemblies.
In terms of application methods, potting typically involves mixing the potting compound and then pouring or injecting it around the components, followed by curing to form a solid encapsulation. Conformal coating can be applied using various techniques such as spraying, dipping, brushing, or selective coating. Spraying and dipping are the most common methods, where the coating material is sprayed onto or fallen into the assembly, forming a uniform layer after curing.
While both potting and conformal coating offer protection for electronic components, they differ in their application methods and the level of encapsulation. Potting provides complete encapsulation but can be difficult to rework, whereas conformal coating offers a thinner layer of protection that is easier to inspect and repair. The choice between the two methods depends on factors such as the level of security required, reworkability, and the specific application needs.
Which industries commonly utilize potting and conformal coating techniques?
Potting and conformal coating are essential techniques employed across various industries to protect electronic components and devices from environmental factors such as moisture, dust, chemicals, and mechanical stress. These techniques are crucial for ensuring electronic products’ reliability, durability, and longevity in harsh operating conditions.
The electronics industry is one prominent industry that extensively utilizes potting and conformal coating techniques. This sector’s applications range from consumer electronics like smartphones and tablets to industrial equipment such as control systems and sensors. Potting involves encapsulating electronic assemblies in a resin or gel-like material to shield them from moisture and other contaminants. This technique is commonly used in manufacturing power supplies, printed circuit boards (PCBs), and LED lighting fixtures.
Conversely, conformal coating entails applying a thin protective layer of polymer material over electronic components. This coating conforms to the contours of the PCB, providing a barrier against moisture, dust, and chemical exposure while offering electrical insulation. The automotive industry extensively employs conformal coatings to safeguard electronic control units (ECUs), sensors, and wiring harnesses from the harsh conditions encountered in vehicles, including temperature fluctuations, vibrations, and exposure to fluids.
Aerospace and defense industries also heavily rely on potting and conformal coating techniques to ensure the reliability of electronic systems in aircraft, satellites, missiles, and military equipment. These applications demand robust protection against extreme temperatures, high altitudes, and radiation exposure. Potting and conformal coating help prevent corrosion, mitigate the effects of thermal cycling and maintain signal integrity in critical electronic components.
In the medical device industry, potting and conformal coating enhance the reliability and safety of electronic medical devices such as pacemakers, defibrillators, and monitoring equipment. These coatings protect sensitive electronics from bodily fluids, sterilization processes, and mechanical stress, ensuring the proper functioning of medical devices in clinical environments.
Potting and conformal coating techniques play a vital role in various industries, safeguarding electronic components and devices from environmental hazards and contributing to electronic systems’ overall reliability and performance in diverse applications.
How do potting and conformal coating affect the physical appearance of electronic devices?
Potting and conformal coating are two common techniques used in the electronics industry to protect electronic devices from environmental factors such as moisture, dust, chemicals, and mechanical stress. While both methods safeguard electronic components, they differ in their application and the resulting physical appearance of the devices.
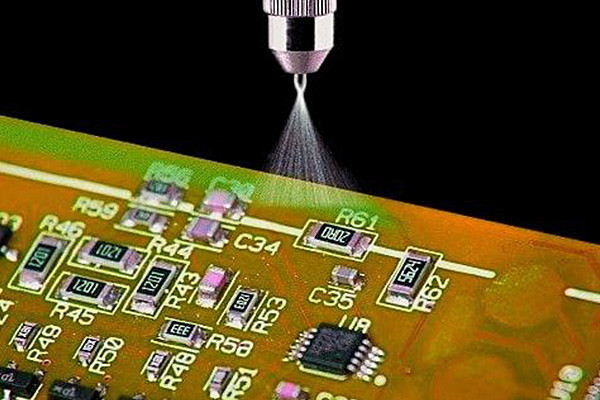
Potting involves encapsulating electronic components within a solid material, typically a resin or silicone compound, to create a protective barrier around them. This process shields the components from external elements and provides structural support and insulation. As a result, potted devices often have a robust and uniform appearance, with all components encased in a solid mass. The surface of a potted device is smooth and generally devoid of visible electronic components, giving it a clean and streamlined look. However, the overall shape and size of the device may be slightly altered due to the added layer of potting material.
On the other hand, conformal coating entails applying a thin protective layer of material, such as acrylic, silicone, or urethane, directly onto the surface of electronic components. Unlike potting, conformal coating does not encapsulate the entire device but instead forms a conformal layer that adheres to its contours. This method allows for greater flexibility and versatility in protecting the device while preserving its original form. Conformal coatings can be applied via spraying, dipping, or brushing, resulting in various finishes ranging from glossy to matte.
Regarding physical appearance, conformal-coated devices retain their original shape and size, with electronic components still visible beneath the thin protective layer. The coating itself may add a slight sheen or texture to the surface, depending on the type of material used and the application method. Conformal coatings can come in different colors, allowing for customization and aesthetic appeal.
Potting and conformal coating effectively protect electronic devices against environmental hazards, but their approach and resulting physical appearance differ. Potting results in a solid, uniform appearance with components completely encased, while conformal coating preserves the device’s original form while providing a thin protective layer. Ultimately, the choice between potting and conformal coating depends on factors such as the level of protection required, desired aesthetics, and manufacturing constraints.
What are the key factors when choosing between potting and conformal coating?
When deciding between potting and conformal coating for electronic components, several key factors must be carefully considered to ensure optimal performance, protection, and cost-effectiveness.
- Environmental Conditions: Assess the operating environment of the electronic device. Potting protects against harsh environments, including moisture, dust, chemicals, and vibration. Conformal coatings are suitable for less extreme conditions where protection against moisture, corrosion, and dust is the primary concern.
- Component Accessibility: Consider the need for component accessibility and potential repairs or modifications. Potting encapsulates the entire assembly, making it challenging to access individual components. Conformal coatings provide a thin, protective layer, allowing more accessible access to components when necessary.
- Mechanical Stability: Evaluate the mechanical stability requirements of the application. Potting provides superior mechanical support, which can enhance shock and vibration resistance. Conformal coatings offer limited mechanical reinforcement but can provide sufficient protection for less demanding applications.
- Heat Dissipation: Analyze the heat dissipation requirements of the components. Potting materials with high thermal conductivity can help dissipate heat effectively, which is crucial for electronic devices prone to overheating. Conformal coatings provide minimal impact on heat dissipation and may even insulate components, leading to potential overheating issues.
- Cost and Complexity: Consider the cost implications and complexity of the potting or coating process. Potting typically requires more material and labor, making it a costlier option, especially for high-volume production. Conformal coating processes are generally less complex and more cost-effective, particularly for large-scale manufacturing.
- Weight and Size Constraints: Evaluate any weight or size constraints the application imposes. Potting adds bulk and weight to the electronic assembly, which may not be suitable for weight-sensitive or compact designs. Conformal coatings provide a thin, lightweight layer that maintains the device’s overall dimensions.
- Electrical Insulation: Determine the need for electrical insulation. Potting materials can provide excellent electrical insulation properties, preventing short circuits and improving reliability. Conformal coatings also offer electrical insulation but may be less effective than potting in extreme conditions.
By carefully considering these factors, manufacturers can make an informed decision between potting and conformal coating to ensure their electronic products’ reliability, longevity, and performance.
How do potting and conformal coating techniques vary in terms of cost-effectiveness?
Potting and conformal coating are two standard methods used in electronic manufacturing to protect components from environmental factors such as moisture, dust, chemicals, and physical damage. While both techniques safeguard electronic assemblies, they differ significantly in terms of cost-effectiveness, depending on the application’s specific requirements.
Potting involves encapsulating electronic components or assemblies within a protective compound, typically a resin or epoxy. This method protects against mechanical stresses, vibration, and moisture ingress. However, potting can be relatively expensive due to the materials used, labor costs associated with the encapsulation process, and the need for specialized equipment such as molds and curing ovens. Additionally, potting may increase the weight and size of the assembly, impacting transportation costs and space requirements.
Conformal coating, on the other hand, involves applying a thin protective layer of material, such as silicone, acrylic, or polyurethane, directly onto the surface of the electronic assembly. This method protects against moisture, dust, and chemical exposure while maintaining flexibility and allowing easy inspection and rework. Conformal coating is generally more cost-effective than potting since it requires fewer materials and less labor-intensive processes. The equipment needed for conformal coatings, such as spray guns or dip tanks, is also less specialized and more readily available, reducing capital investment costs.
The choice between potting and conformal coating depends on various factors, including the level of protection required, environmental conditions, size and weight constraints, and budget considerations. Potting may be the preferred option for applications where extreme environmental protection and ruggedness are paramount despite its higher cost. Conversely, conformal coating offers a more economical solution without compromising performance for applications where cost efficiency, flexibility, and ease of maintenance are critical.
While both potting and conformal coating techniques effectively protect electronic assemblies, conformal coating tends to be more cost-effective due to lower material and labor costs, as well as greater flexibility and ease of application. However, the optimal choice depends on each application’s specific requirements and constraints.
What are the typical curing processes for potting and conformal coating materials?
Potting and conformal coating are essential in electronics manufacturing to protect electronic components from environmental factors such as moisture, dust, and vibration. The curing processes for potting and conformal coating materials vary depending on the type of material used, but they generally involve similar principles.
- Thermal Curing: Many potting and conformal coating materials require thermal curing, where the coated or potted components are subjected to elevated temperatures to initiate and complete the curing process. Typically, the components are placed in an oven or a curing chamber where temperatures are carefully controlled. The duration of curing and the temperature levels vary based on the specific material being used. For instance, epoxy resins often require temperatures ranging from 50°C to 150°C, with curing times ranging from a few hours to several days.
- UV Curing: Some conformal coating materials utilize UV curing, exposing the coating to ultraviolet light to initiate polymerization and curing. UV-curable coatings offer rapid curing times, which can be completed within seconds to minutes. However, UV curing requires specialized equipment such as UV lamps or LED arrays.
- Moisture Curing: Certain conformal coating materials employ moisture curing mechanisms, where exposure to ambient moisture triggers the curing process. These coatings typically contain moisture-sensitive functional groups that react with water vapor in the environment to initiate curing. Moisture-curable coatings offer convenience as they do not require additional curing equipment, but curing times may vary depending on ambient humidity levels.
- Chemical Curing: Some potting compounds and conformal coatings undergo chemical curing reactions, mixing two or more components to initiate polymerization. This type of curing often involves mixing a resin and a hardener or catalyst. Once mixed, the chemical reaction begins, leading to the formation of a cured polymer network. The curing time and conditions depend on the specific chemical composition of the material.
Depending on the material composition and desired properties, the curing processes for potting and conformal coating materials can involve thermal, UV, moisture, or chemical. Manufacturers must carefully select the appropriate curing method to ensure proper protection and performance of electronic components.
Can potting and conformal coating be applied to sensitive electronic components?
Potting and conformal coating are standard techniques to protect sensitive electronic components from environmental factors such as moisture, dust, vibration, and temperature variations. Both methods can be applied to sensitive electronic components but have different properties and applications.
Potting involves encapsulating the entire electronic assembly in a solid or gel-like material such as epoxy resin or silicone. This technique provides excellent protection against physical damage, moisture, and vibration. Potting compounds also offer good thermal conductivity, which helps dissipate heat generated by the electronic components. However, potting can be challenging for sensitive components as it involves completely enclosing them, which may affect their performance if not done correctly. Care must be taken to ensure the potting material does not interfere with sensitive areas or components, such as sensors or connectors.
Conversely, conformal coating involves applying a thin protective layer of material (such as silicone, acrylic, or urethane) directly onto the surface of the electronic assembly. Conformal coatings protect against moisture, dust, and mild mechanical stress while allowing for some flexibility and accessibility to the components. They are handy for sensitive components that require periodic maintenance or adjustment since they can be easily removed and reapplied. However, conformal coatings may not provide as robust protection against physical damage or extreme environmental conditions as potting.
When applying potting or conformal coating to sensitive electronic components, several factors must be considered:
- The compatibility of the coating material with the components and the surrounding environment must be ensured. Some coatings may contain chemicals that could degrade or interfere with sensitive materials.
- The application process must be carefully controlled to prevent air bubbles, uneven coverage, or excess material buildup, which could affect the components’ performance.
- Post-application testing and inspection are essential to verify that the coating has been applied correctly and does not adversely affect the functionality of the electronic assembly.
Both potting and conformal coating can be applied to sensitive electronic components to protect against environmental factors. Still, the choice between the two depends on the application’s specific requirements, including the level of security needed, the components’ accessibility, and the potential impact on performance.
How do potting and conformal coating techniques impact the thermal management of electronic devices?
Potting and conformal coating techniques play crucial roles in the thermal management of electronic devices by influencing heat dissipation, thermal conductivity, and temperature regulation.
Potting involves encapsulating the entire electronic assembly in a solid or gel-like material, such as epoxy resin or silicone. While potting protects against environmental factors, it can also impact thermal management. The choice of potting material and its thermal conductivity properties significantly affect heat dissipation. Some potting compounds offer good thermal conductivity, helping to transfer heat away from sensitive components and distribute it across the encapsulated assembly. However, the thermal conductivity of the potting material is poor. In that case, heat may become trapped within the enclosure, leading to elevated temperatures and potentially affecting the performance and reliability of the electronic device.
Conversely, conformal coating involves applying a thin protective layer of material directly onto the surface of the electronic assembly. While conformal coatings provide less robust protection than potting, they can have a minimal impact on thermal management. Thin conformal coatings typically have little effect on heat dissipation since they do not significantly impede heat transfer from the electronic components to the surrounding environment. Some conformal coating materials also offer good thermal conductivity properties, further aiding in heat dissipation and thermal management.
Both potting and conformal coating techniques can also influence the ability of electronic devices to withstand temperature variations. Properly selected and applied materials can provide insulation against extreme temperatures or thermal shock, helping maintain the electronic components’ integrity and reliability.
While potting and conformal coating techniques are primarily employed for environmental protection, their impact on thermal management should be noticed. Careful selection of materials and application methods is essential to ensure optimal heat dissipation, temperature regulation, and overall reliability of electronic devices.
Are there any limitations or drawbacks associated with potting and conformal coating?
Potting and conformal coating are widely used in electronics manufacturing to protect electronic components and circuitry from environmental factors such as moisture, dust, chemicals, and mechanical stress. While these methods offer significant benefits, they also come with limitations and drawbacks that need to be considered:
- Rigidity: Potting involves encapsulating electronic components in a solid compound, which can make them rigid. This rigidity can be a limitation in applications where flexibility or movement is required, as it may increase the risk of damage to the components.
- Difficulty of Repair: Once electronic components are potted or conformally coated, accessing and repairing them becomes challenging. If a component fails or needs replacement, it often requires completely removing the potting material or coating, which can be time-consuming and costly.
- Thermal Management: Potting compounds and conformal coatings can inhibit heat dissipation from electronic components, potentially leading to overheating issues. Proper thermal management considerations are essential to prevent the components’ performance degradation or premature failure.
- Incomplete Coverage: Achieving uniform coverage of all components with potting or conformal coating can be challenging, especially for complex assemblies with intricate geometries. Gaps or voids in coverage may leave components vulnerable to environmental damage, reducing the effectiveness of the protection.
- Compatibility Issues: Some potting compounds and conformal coatings may not be compatible with specific components or materials used in electronic assemblies. Chemical compatibility testing is necessary to ensure that the potting or coating material does not react adversely with the components it is intended to protect.
- Cost: Potting and conformal coating processes add additional costs to the manufacturing process regarding materials, equipment, and labor. Depending on the scale of production and the complexity of the assembly, these costs can become significant factors in the overall manufacturing budget.
- Weight and Size Increase: Potting compounds and conformal coatings add weight and volume to electronic assemblies, which can be undesirable in applications where space and weight are critical factors, such as aerospace or portable electronics.
Despite these limitations, potting and conformal coating remain indispensable for protecting electronic assemblies in many industries. Careful consideration of each application’s specific requirements and constraints is essential to determine the most suitable protection method while minimizing drawbacks.
What are some common challenges encountered during the potting and conformal coating process?
Potting and conformal coating are essential in electronics manufacturing to protect electronic components from environmental factors such as moisture, dust, chemicals, and mechanical stress. However, several challenges can arise during these processes, hindering their effectiveness and impacting product quality. Some common challenges include:
- Material Selection: Choosing the suitable potting compound or conformal coating material is crucial. Factors such as compatibility with components, environmental conditions, and application methods must be considered. Using incompatible materials can lead to poor adhesion, cracking, or delamination.
- Surface Preparation: Proper surface preparation is essential for ensuring adhesion and effectiveness of the coating. Contaminants such as oils, residues, and oxides can inhibit adhesion, leading to coating defects. Achieving a clean, dry surface often requires thorough cleaning and sometimes surface treatment like plasma or corona.
- Uniformity of Coating: Achieving uniform coverage of the potting compound or conformal coating is critical for providing consistent protection to electronic components. Inadequate coverage can leave areas vulnerable to environmental damage, while excessive coating thickness can lead to overheating or interference with component functionality.
- Curing and Drying: Proper curing or drying of the potting compound or conformal coating is essential for achieving desired properties such as hardness, adhesion, and chemical resistance. Inadequate curing time or conditions can result in incomplete polymerization, leading to reduced performance or premature failure of the coating.
- Air Entrapment and Void Formation: During potting, air trapped within the encapsulant can form voids, compromising the protection provided to the electronic components. Proper degassing techniques and avoiding high-viscosity materials can help mitigate this issue.
- Thermal Management: Potting compounds and conformal coatings can affect thermal conductivity, potentially leading to heat buildup and decreased performance or reliability of sensitive components. Proper consideration of thermal properties and design for heat dissipation is essential.
- Compatibility with Components: Some electronic components may be sensitive to the chemicals or solvents in potting compounds or conformal coatings. Compatibility testing is necessary to ensure that the materials used will not degrade or damage the components over time.
Addressing these challenges requires careful planning, selection of appropriate materials, adherence to best practices, and sometimes specialized equipment or expertise. Effective potting and conformal coating processes are crucial for ensuring electronic devices’ long-term reliability and performance in various environments.
How do potting and conformal coating techniques contribute to the longevity of electronic devices?
Potting and conformal coating techniques play a crucial role in enhancing the longevity and reliability of electronic devices by protecting various environmental factors and mechanical stresses. These techniques offer several key benefits that contribute to the extended lifespan of electronic devices:
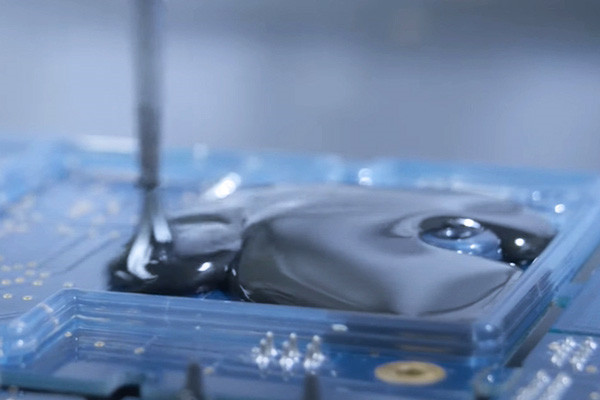
- Environmental Protection: Potting and conformal coatings create a barrier between sensitive electronic components and harsh environmental conditions such as moisture, dust, chemicals, and temperature fluctuations. By preventing these environmental factors from reaching the components, potting and coating techniques help mitigate corrosion, oxidation, and other forms of degradation that can lead to device failure over time.
- Mechanical Stability: Electronic devices are often subjected to mechanical stresses during operation, transportation, and handling. Potting compounds encapsulate delicate components, providing structural support and damping vibrations, thus reducing the risk of damage from shocks and vibrations. Similarly, conformal coatings offer a protective layer that helps prevent mechanical damage, such as scratches and abrasions, to the circuit board and its components.
- Improved Thermal Management: Potting compounds with appropriate thermal conductivity properties can facilitate efficient heat dissipation from electronic components, helping to maintain optimal operating temperatures. By dissipating heat effectively, potting compounds prevent overheating, thermal cycling stresses, and the associated degradation of component performance and reliability.
- Electrical Insulation: Potting compounds and conformal coatings provide electrical insulation, reducing the risk of short circuits and electrical malfunctions caused by moisture ingress or contamination. This insulation helps maintain proper electrical performance and prevents electrical breakdowns, particularly in high-voltage or high-frequency applications.
- Prevention of Contamination: Potting and conformal coating techniques seal electronic components and circuitry, avoiding contamination from foreign particles, oils, or chemicals. Contamination can lead to electrical leakage, corrosion, or insulation breakdown, all of which can compromise the functionality and reliability of electronic devices.
Overall, potting and conformal coating techniques contribute significantly to the longevity of electronic devices by safeguarding them against a wide range of environmental, mechanical, thermal, and electrical hazards. By providing robust protection and insulation, these techniques help ensure the reliable operation of electronic devices over extended periods, reducing maintenance costs and enhancing user satisfaction.
What are the environmental considerations related to potting and conformal coating materials?
Potting and conformal coating materials protect electronic components and assemblies from environmental factors such as moisture, dust, chemicals, and mechanical stress. However, these materials themselves can have ecological considerations that need to be taken into account:
- Chemical Composition: Many potting and conformal coating materials contain chemicals that can be hazardous to the environment if improperly handled. For instance, some formulations may include volatile organic compounds (VOCs), heavy metals, or other toxic substances. Improper disposal or leaching of these chemicals into the environment can lead to soil or water contamination, posing risks to ecosystems and human health.
- Life Cycle Analysis: Understanding the entire lifecycle of potting and conformal coating materials is essential for assessing their environmental impact. This includes consideration of raw material extraction, manufacturing processes, transportation, application, use, and end-of-life disposal or recycling. Materials with high energy consumption or emissions during production, or those that are difficult to recycle or dispose of responsibly, can have significant environmental footprints.
- Energy Consumption: The energy required for manufacturing and applying potting and conformal coating materials can impact their ecological impact. Processes such as curing or drying may involve energy-intensive methods like heating or UV radiation. Opting for materials and application methods that minimize energy consumption can reduce environmental burdens.
- Waste Management: Proper disposal of unused or expired potting and conformal coating materials is crucial to prevent ecological harm. Materials that cannot be easily recycled or treated may end up in landfills or incinerators, potentially releasing harmful substances into the air, soil, or water. Manufacturers and users should prioritize materials that can be recycled or disposed of safely.
- Eco-Friendly Alternatives: Increasingly, there is a push towards developing and using environmentally friendly alternatives to traditional potting and conformal coating materials. These may include bio-based or renewable formulations, water-based coatings, or materials with reduced toxicity and environmental impact. Manufacturers can minimize their ecological footprint and contribute to sustainability efforts by choosing greener options.
While potting and conformal coating materials are essential for protecting electronics, their environmental impact should be noticed. By considering factors such as chemical composition, life cycle analysis, energy consumption, waste management, and eco-friendly alternatives, manufacturers and users can make informed decisions to minimize environmental harm.
Can potting and conformal coating be applied to electronic assemblies with complex geometries?
Potting and conformal coating are widely used techniques in electronic assembly to protect components from environmental factors such as moisture, dust, and vibration. While these methods are typically applied to electronic assemblies with relatively simple geometries, they can also be adapted for use with assemblies featuring complex shapes and configurations.
Potting involves encapsulating electronic components in a solid or semi-solid material, such as epoxy resin or silicone, to provide mechanical support and environmental protection. It’s commonly used for transformers, sensors, and circuit boards. While potting is straightforward for assemblies with flat or regular shapes, it becomes more challenging with complex geometries. However, by employing specialized techniques such as vacuum potting or flexible potting materials, it’s possible to fill voids and cover irregular shapes effectively. Engineers may use molds or fixtures to contain the potting material during curing, ensuring it conforms to the assembly’s contours.
Conversely, conformal coating involves applying a thin layer of protective material, such as acrylic, silicone, or urethane, directly onto the surface of printed circuit boards (PCBs) and other electronic assemblies. It forms a protective barrier while allowing access to components for repair or modification. Conformal coating can be challenging to apply uniformly to assemblies with intricate shapes or densely packed components. However, selective coating, robotic spraying, or dip coating can ensure complete coverage, even in hard-to-reach areas. Some conformal coatings are also available in sprayable or brush-on formulations, allowing for more precise application on complex geometries.
Despite the challenges, potting and conformal coating can be successfully applied to electronic assemblies with complex geometries with careful planning, specialized equipment, and expertise. When implementing these protective measures, engineers must consider factors such as material compatibility, curing processes, and access to critical components. By leveraging innovative techniques and adapting existing processes, manufacturers can ensure the reliability and longevity of electronic assemblies in diverse applications and environments.
How do potting and conformal coating techniques differ in terms of workability?
Potting and conformal coating are two standard techniques used in electronics manufacturing to protect components and assemblies from environmental factors such as moisture, dust, and temperature extremes. While both methods enhance the durability and reliability of electronic devices, they differ significantly in terms of their application, workability, and effectiveness.
Potting involves encapsulating electronic components or assemblies in a protective compound, typically a resin or silicone-based material. The potting process provides robust protection by surrounding the components, forming a solid, monolithic barrier. This technique benefits applications where the electronics are exposed to harsh environments or mechanical stress. Potting materials are available in various viscosities, allowing for customization based on the application’s specific requirements. However, potting can be relatively labor-intensive and requires careful consideration of factors such as curing time, thermal expansion coefficients, and compatibility with other materials.
Conversely, conformal coating involves applying a thin layer of protective material over the surface of electronic assemblies. This coating conforms to the contours of the components, providing a barrier against moisture, dust, and other contaminants. Conformal coatings are typically applied using spraying, dipping, or brushing methods. Unlike potting, conformal coating allows for easier inspection and rework of individual components, as the coating can be selectively applied or removed as needed. However, conformal coatings may not provide as robust protection as potting, particularly when components are subjected to extreme conditions or mechanical stress.
Regarding workability, potting can be more challenging due to the need for precise mixing and application of the potting compound. Additionally, potting may require specialized equipment, such as vacuum chambers or pressure vessels, to remove air bubbles and ensure proper encapsulation. Conversely, conformal coating is generally more straightforward and can be applied using conventional spraying or dipping equipment. However, both techniques require careful attention to detail to ensure proper coverage and adhesion of the protective material.
While potting offers superior protection and durability, conformal coating provides greater flexibility and ease of application. The choice between the two techniques depends on factors such as the specific requirements of the application, the level of protection needed, and considerations of cost and manufacturability.
What future trends are anticipated in potting and conformal coating for electronic manufacturing?
In the field of potting and conformal coating for electronic manufacturing, several trends are anticipated to shape the future landscape:
- Miniaturization and Increased Complexity: As electronic devices continue to shrink in size and increase in complexity, there will be a growing demand for potting and conformal coating materials that can protect densely packed components without compromising performance. This trend will drive the development of thinner coatings with enhanced protective properties.
- High-Performance Materials: Manufacturers will increasingly seek potting and conformal coating materials that offer superior protection against various environmental factors, including moisture, chemicals, and temperature extremes. Advanced formulations with high thermal conductivity, flame resistance, and chemical inertness will be in high demand.
- Flexible and Stretchable Coatings: With the rise of flexible and stretchable electronics, there will be a need for potting and conformal coating materials that can conform to irregular shapes and withstand repeated bending and stretching without cracking or delamination. Innovations in flexible coating materials based on elastomers and polymers will cater to this demand.
- Environmentally Friendly Solutions: As sustainability becomes increasingly important, there will be a shift towards environmentally friendly potting and conformal coating materials that minimize the use of hazardous substances and reduce environmental impact throughout the product lifecycle. Bio-based and recyclable materials will gain traction in the market.
- Integration of Smart Features: Future coatings may incorporate intelligent functionalities such as self-healing properties to repair minor damage, self-cleaning capabilities to repel contaminants, or sensing capabilities to monitor the condition of the coated components in real time. These intelligent features will enhance the reliability and longevity of electronic devices.
- Automation and Digitalization: Adopting automation and digitalization technologies will streamline the potting and conformal coating process, improving efficiency, consistency, and quality control. Robotic dispensing systems, inline inspection techniques, and data analytics tools will be integrated into manufacturing lines to optimize production processes.
- Customization and Tailored Solutions: With the diversification of electronic applications, there will be a growing demand for customized potting and conformal coating solutions tailored to specific requirements such as operating conditions, substrate materials, and application methods. Manufacturers will offer various customizable options to meet the needs of multiple industries and applications.
The future of potting and conformal coating in electronic manufacturing will be characterized by advancements in materials, processes, and functionalities to address the evolving demands of miniaturization, flexibility, sustainability, and intelligent integration, supported by automation and customization capabilities.
Conclusion:
In conclusion, while both potting and conformal coating serve as vital protective measures in electronics manufacturing, they exhibit distinct characteristics and applications. Potting involves encapsulating entire electronic assemblies in a protective material, offering robust protection against mechanical stress, moisture, and other environmental factors. On the other hand, conformal coating entails applying a thin layer of protective material over electronic components, providing resistance against humidity, dust, and chemical exposure while maintaining flexibility. The choice between potting and conformal coating depends on factors such as the level of protection required, the specific environment of use, and the characteristics of the electronic components. As technology advances, innovations in materials and application techniques continue to enhance the effectiveness and versatility of both potting and conformal coating methods in safeguarding electronic devices.
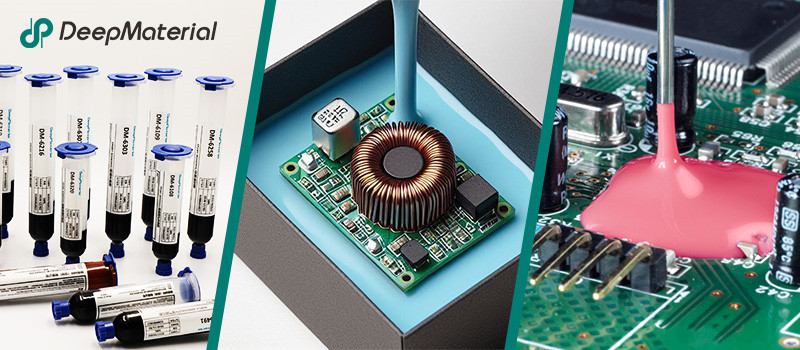
About DeepMaterial
DeepMaterial is a trusted supplier of encapsulant materials that are used in electronics manufacturing worldwide. From chip on board encapsulants such as glob top material to conformal coatings, underfills, low pressure molding, and potting solutions, DeepMaterial offers a full range of circuit board protection materials that effectively protect circuit boards while help reduce costs. More…Deepmaterial is a the manufacturer of epoxy adhesives including hardeners, metalbond, and metal filled resins. Structural, toughened medium viscosity, and non-sag adhesives are also offered. Some adhesives are resistant to thermal shock, chemical, vibration dampening, and impact. Suitable for metals, plastics, wood, and ceramics. Serves electronics, aerospace, automotive, tooling, marine, and construction industries. REACH and RoHS compliant. FDA approved. UL listed. Meets military specifications. We are the one of best adhesive manufacturers in China.
Blogs & News
Potting compounds are at the frontline of electronics assembly, delivering effective protection in challenging environmental conditions while improving mechanical strength and offering high electric insulation. Used within a variety of industries, electrical potting compounds are found within a broad range of consumer electronics, as well as used in applications across the automotive, aerospace, and other industries where electronic assemblies are prevalent.
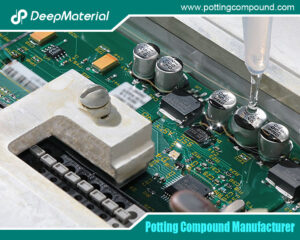
Silicone Potting Compound for Electronics
Silicone Potting Compound for Electronics In the rapidly evolving world of electronics, ensuring the reliability, durability, and performance of electronic components is paramount. One critical
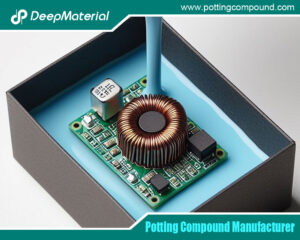
Potting Compound vs. Epoxy: A Comprehensive Comparison
Potting Compound vs. Epoxy: A Comprehensive Comparison In the world of electronics, manufacturing, and material encapsulation, two terms frequently come up: potting compounds and epoxy.
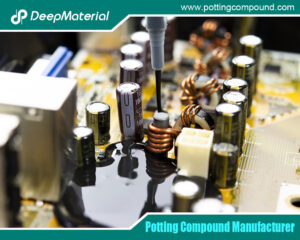
Potting Compound for PCB
Potting Compound for PCB A potting compound is a liquid or semi-liquid material that is poured or injected over a PCB or electronic assembly, then
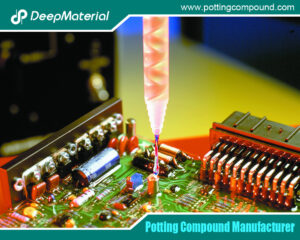
In – depth Analysis of the Curing Characteristics of Electronic Potting Compounds
In – depth Analysis of the Curing Characteristics of Electronic Potting Compounds Electronic potting compounds play a vital role in the electronics industry. They can
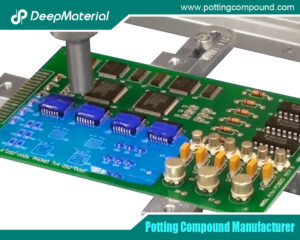
A Comprehensive Analysis of the Environmental Performance of Encapsulating Materials: From Regulations to Practices
A Comprehensive Analysis of the Environmental Performance of Encapsulating Materials: From Regulations to Practices In modern industrial manufacturing, encapsulating materials are widely used in numerous

A Comprehensive Analysis of PCB Encapsulation Quality Inspection: Innovative Application of Non-Destructive Testing Technologies
A Comprehensive Analysis of PCB Encapsulation Quality Inspection: Innovative Application of Non-Destructive Testing Technologies In the field of electronic manufacturing, the encapsulation process of printed