What is the difference between potting and encapsulation
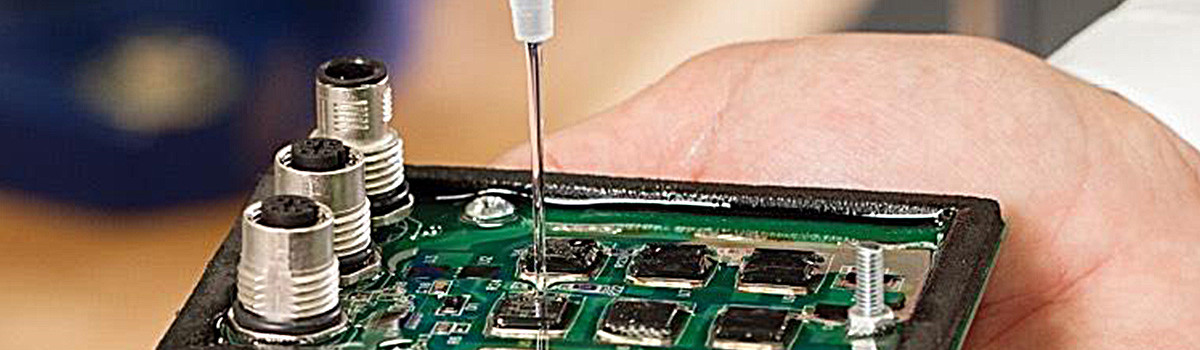
In various manufacturing and industrial processes, the terms “potting” and “encapsulation” are frequently used. While they both involve protecting components or assemblies, they serve distinct purposes and are applied differently. Understanding the disparities between potting and encapsulation is crucial for selecting the appropriate method for specific applications. This article delves into the nuances of potting and encapsulation, elucidating their disparities, applications, and benefits.
Table of Contents
TogglePotting vs. Encapsulation – FAQs
What is potting?
Potting is used in various industries, including electronics, gardening, and manufacturing, to encase or encapsulate a component or material within a protective substance, typically a resin or a polymer. The primary purpose of potting is to safeguard the enclosed object from environmental factors such as moisture, dust, vibration, and mechanical shock, thus extending its lifespan and ensuring reliable performance.
Potting is commonly employed in electronics to protect sensitive components like circuit boards, wires, and connectors from moisture, corrosion, and physical damage. The process involves placing the electronic assembly into a mold or container and filling the space around it with a liquid resin or polymer. Once cured, the resin forms a solid, protective barrier around the electronics, effectively sealing them from external elements. This method enhances the durability and reliability of electronic devices, making them suitable for use in harsh environments such as automotive, aerospace, marine, and industrial applications.
Potting refers to planting and growing plants in containers, such as pots or planters, rather than directly in the ground. This allows for greater control over soil composition, drainage, and mobility, making it particularly useful for urban gardening, indoor plants, and landscaping projects.
In manufacturing, potting is utilized to encapsulate delicate or fragile items, such as delicate artwork, electronic modules, or sensitive instruments, for transportation or display purposes. The potting material provides a protective shell, preventing damage during handling, shipping, or storage.
The choice of potting material depends on the application’s specific requirements, including temperature resistance, flexibility, chemical compatibility, and electrical insulation properties. Common materials used for potting include epoxy resins, silicone rubber, polyurethane, and acrylic compounds.
Potting is crucial in protecting and preserving various objects and components, ensuring their longevity and performance in diverse environments. Its applications span industries, offering a versatile solution for safeguarding valuable assets from external threats.
What is encapsulation?
Encapsulation is a fundamental concept in object-oriented programming (OOP) that refers to the bundling of data and methods that operate on that data into a single unit called a class. It enables the implementation details of a class to be hidden from the outside world, allowing for better control over data accessibility and modification.
At its core, encapsulation promotes the idea of data hiding, where the internal state of an object is kept private and can only be accessed through well-defined interfaces provided by the class. This means that the internal implementation details are not exposed directly to the outside world, which enhances security, maintains integrity, and facilitates more manageable maintenance and modification of code.
Encapsulation provides several key benefits:
- Data Protection: By restricting direct access to the internal state of an object, encapsulation prevents unintended or unauthorized modification of data, ensuring that it remains consistent and valid.
- Abstraction: Encapsulation allows developers to define clear and concise interfaces for interacting with objects. Users of the class need not concern themselves with the intricacies of how data is stored or manipulated internally; they only need to understand how to use the provided methods.
- Modularity: Encapsulation encourages modular design by grouping related data and behavior into coherent units. This improves code organization, readability, and reusability, as classes can be easily reused in different parts of a program or project.
- Maintenance and Evolution: Since encapsulation hides a class’s internal details, implementation changes can be made without affecting code that uses the class’s interface. This promotes code flexibility and makes evolving and extending software systems easier over time.
Encapsulation is a powerful concept in OOP that promotes data hiding, abstraction, modularity, and maintainability. Developers can create more robust, secure, and flexible software systems by encapsulating data and methods within classes and providing well-defined interfaces for interaction.
How does potting differ from encapsulation?
Potting and encapsulation are two common techniques used in electronics and manufacturing, particularly in protecting electronic components and assemblies. While both processes safeguard delicate electronics from environmental factors such as moisture, dust, and vibration, they differ in their approach and application.
Potting involves covering electronic components or assemblies with a liquid resin that solidifies into a protective shell. This resin is typically a two-part compound that, when mixed, undergoes a chemical reaction to form a solid, durable material. The potting material surrounds the components, filling all voids and gaps and providing excellent protection against moisture, chemicals, and mechanical stress. Potting is commonly used for applications where the electronics are subjected to harsh environmental conditions, such as outdoor equipment, automotive electronics, and marine electronics.
Encapsulation involves encapsulating electronic components within a protective material, often a thermoplastic or thermosetting polymer. Unlike potting, encapsulation does not surround the components but instead forms a protective layer around them. This layer acts as a barrier against environmental hazards while still allowing for some flexibility and accessibility to the components if maintenance or repair is required. Encapsulation is frequently used in applications where the electronics need protection but must remain accessible, such as in consumer electronics, circuit boards, and sensors.
While both potting and encapsulation protect electronic components, they differ in their approach and level of coverage. Potting completely surrounds the components with a solid resin, providing maximum protection but limiting accessibility, while encapsulation forms a protective layer around the components, allowing for some flexibility and accessibility while still providing adequate protection. The choice between potting and encapsulation depends on the specific requirements of the application, including the level of protection needed, accessibility of the components, and environmental conditions they will be subjected to.
What are the primary purposes of potting?
Potting serves various primary purposes across industries and applications, from electronics to horticulture. Its fundamental objectives include protection, insulation, and stabilization.
Protection: Potting involves encapsulating an object or material within a protective casing, typically made of resin or silicone. This casing shields the internal components from environmental factors such as moisture, dust, chemicals, and physical damage. In electronics, for instance, potting protects delicate circuitry from moisture ingress, corrosion, and mechanical stress, thereby enhancing the lifespan and reliability of electronic devices.
Insulation: Potting materials often possess insulating properties, crucial for preventing electrical conductivity or short circuits in electronic components. Potting eliminates the risk of electrical leakage or interference by encasing conductive parts in a non-conductive material. This insulation also helps maintain stable electrical performance, especially in harsh operating conditions where temperature fluctuations or exposure to contaminants could compromise the integrity of electrical systems.
Stabilization: Potting provides structural support and stabilization to fragile or delicate components, preventing them from shifting or vibrating within their housing. This is particularly important in applications subject to mechanical stress or vibration, such as automotive electronics or industrial machinery. By securely anchoring components in place, potting minimizes the risk of component failure due to movement or mechanical shock, ensuring optimal performance and reliability.
Thermal Management: Some potting materials offer thermal conductivity properties, allowing them to efficiently dissipate heat. This is advantageous in applications where heat dissipation is critical for maintaining the optimal operating temperature of electronic components. By transferring heat away from sensitive components, potting helps prevent overheating and thermal damage, thus improving electronic systems’ overall performance and longevity.
Chemical Resistance: Potting materials can resist various chemicals, including solvents, acids, and bases. This chemical resistance is essential in environments where exposure to corrosive substances is likely. By forming a protective barrier against chemical attack, potting ensures the durability and functionality of encapsulated components in chemically aggressive settings.
Potting is a versatile solution for protecting, insulating, stabilizing, managing heat, and enhancing the longevity and reliability of various components and systems across diverse industries. Its multifaceted benefits contribute to improved performance, durability, and safety in multiple applications.
What are the primary purposes of encapsulation?
Encapsulation is a fundamental concept in object-oriented programming (OOP) that involves bundling data and methods that operate on that data into a single unit, typically called a class. It serves several primary purposes, each contributing to a software system’s overall structure, organization, and security.
- Data Hiding: Encapsulation allows an object’s internal state to be hidden from the outside world. By marking certain attributes or methods as private or protected, they can only be accessed and modified by the object’s methods. This prevents external code from directly manipulating the object’s internal state, reducing the risk of unintended side effects or data corruption. This principle of data hiding enhances the security and integrity of the program.
- Abstraction: Encapsulation promotes abstraction by exposing only essential features of an object while hiding unnecessary details. External code interacts with the object through a well-defined interface provided by its public methods. This abstraction simplifies the usage of objects, allowing developers to focus on high-level functionality without worrying about the internal implementation details. It also facilitates modularity and code reusability by enabling objects to be treated as black boxes.
- Modularity: Encapsulation facilitates modular design by encapsulating related data and behavior within a single unit. Objects can be independently developed, tested, and maintained, promoting code organization and scalability. Modularity encourages code reuse, as encapsulated objects can be easily integrated into different system parts without affecting other components. This promotes maintainability, as changes to one module have a limited impact on other modules.
- Encapsulation as a Barrier: Encapsulation is a barrier between an object’s internal implementation and external code. This separation of concerns improves code maintainability and scalability by reducing dependencies between different system parts. Changes to an object’s internal implementation can be made without affecting external code that relies on its public interface, promoting code flexibility and adaptability to evolving requirements.
Encapsulation plays a crucial role in OOP by providing data hiding, abstraction, modularity, and code organization mechanisms. Encapsulating related data and behavior within objects and controlling access to them enhances the security, maintainability, and scalability of software systems.
What are the typical materials used for potting?
Potting materials protect electronic components from environmental factors such as moisture, dust, vibration, and thermal shock. The choice of materials depends on the specific requirements of the application. Some typical materials used for potting include:
- Epoxy Resins: Epoxy resins are widely used for potting due to their excellent adhesion, chemical resistance, and thermal properties. They provide strong protection against moisture and mechanical stress.
- Silicone: Silicone potting compounds offer flexibility and high-temperature resistance, making them suitable for applications where thermal cycling is a concern. They also provide good electrical insulation properties.
- Polyurethane: Polyurethane potting compounds offer a balance of flexibility and rigidity, making them suitable for applications with some degree of shock absorption. They provide good resistance to moisture and chemicals.
- Acrylics: Acrylic potting compounds are known for their fast curing times and excellent adhesion to various substrates. They offer good resistance to UV radiation and are often used in outdoor applications.
- Thermoplastics: Thermoplastic materials such as polyethylene and polypropylene are used for potting in applications where reworkability or recyclability is essential. They can be melted and reshaped, making repairs or component replacement easier.
- Casting Resins: Casting resins, such as polyester and polyurethane casting resins, are used for potting in applications where optical clarity or specific aesthetic properties are desired. They are commonly used in applications such as LED encapsulation.
- Ceramics: In high-temperature applications or where extreme mechanical strength is required, ceramic potting materials may be used. These materials offer excellent thermal conductivity and resistance to harsh environments.
- Gel Encapsulation: Gel encapsulants are used for potting applications where vibration damping and stress relief are critical. They provide excellent protection against moisture and mechanical shock.
Each of these materials has advantages and disadvantages, and the selection process involves considering factors such as temperature range, chemical compatibility, mechanical strength, and cost. Factors like curing time, viscosity, and ease of application also play a role in determining the most suitable potting material for a given application.
What are the typical materials used for encapsulation?
Encapsulation is a process commonly used in various industries such as pharmaceuticals, food, electronics, and cosmetics to protect active ingredients, enhance stability, control release, and improve the overall performance of products. The choice of materials for encapsulation depends on the specific application requirements, desired properties, and compatibility with the encapsulated substance. Several typical materials are utilized for encapsulation:
- Polymers: Polymers are widely employed for encapsulation due to their versatility, tunable properties, and compatibility with different substances. Examples include natural polymers like gelatin, alginate, and chitosan, as well as synthetic polymers such as poly(lactic-co-glycolic acid) (PLGA), polyvinyl alcohol (PVA), and polyethylene glycol (PEG).
- Lipids: Lipid-based materials are often used in encapsulation, especially for applications involving bioactive compounds, drugs, or nutraceuticals. Liposomes, lipid nanoparticles, and solid lipid nanoparticles are some examples. Lipid-based encapsulation offers advantages like biocompatibility, stability, and controlled release.
- Ceramics: In specific applications, ceramic materials like silica, alumina, and titania are employed for encapsulation, particularly for high-temperature or harsh environments. Ceramic encapsulation provides excellent thermal stability, chemical resistance, and mechanical strength.
- Metallic Materials: Metals such as gold, silver, and iron oxide nanoparticles are utilized for encapsulation, particularly in biomedical and electronic applications. Metallic encapsulation offers unique properties like conductivity, magnetism, and optical characteristics.
- Hydrogels: Hydrogels, composed of cross-linked hydrophilic polymers, are encapsulated in applications requiring water absorption and retention. Hydrogel encapsulation finds applications in drug delivery, tissue engineering, and wound healing.
- Microcapsules: Microcapsules are small spherical particles composed of a shell material encapsulating a core substance. Various materials like polymers, lipids, and proteins can be used for microcapsule fabrication, offering controlled release and protection of encapsulated substances.
- Nanocomposites: Nanocomposite materials, which combine nanoparticles with a matrix material, are increasingly utilized for encapsulation due to their enhanced properties, such as mechanical strength, barrier properties, and functionality.
Overall, the selection of encapsulation materials depends on factors such as desired release kinetics, stability requirements, biocompatibility, scalability, and cost-effectiveness. Each material offers distinct advantages suited to specific applications.
How does the application process of potting differ from encapsulation?
Potting and encapsulation are two standard methods used in electronics manufacturing and assembly to protect sensitive components from environmental factors such as moisture, vibration, and shock. While both techniques serve similar purposes, they differ in their application processes and the level of protection they offer.
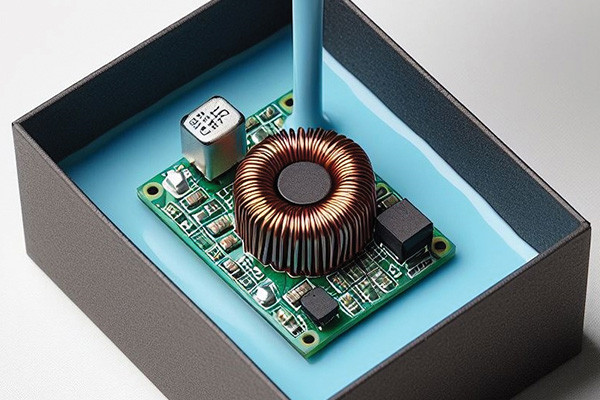
Potting involves completely encasing electronic components or assemblies in a liquid resin or compound, typically a thermosetting polymer like epoxy. The process begins by preparing the electronic assembly and placing it within a mold or container. The liquid resin is poured or injected into the mold to surround the components. Once the resin cures and hardens, it forms a solid, protective enclosure around the electronics, sealing them from the external environment. Potting is particularly suitable for applications where the components must be fully sealed and protected from moisture, dust, and mechanical stress.
On the other hand, encapsulation involves applying a protective coating or layer over the electronic components without completely enclosing them. This coating can be made of epoxy resins, silicones, or urethanes. Encapsulation is typically applied using techniques such as spray, dip, or selective coating. Unlike potting, encapsulation leaves some parts of the electronic assembly exposed, allowing easier access to components for repair or maintenance. Encapsulation protects against environmental factors while allowing for some degree of flexibility and accessibility.
the main difference between potting and encapsulation lies in the extent to which the electronic components are enclosed and the application process involved. Potting completely encases the elements in a solid resin, offering maximum protection but limiting accessibility. At the same time, encapsulation applies a protective coating over the components, providing moderate protection and easier access. The choice between potting and encapsulation depends on the specific application requirements, including the level of security needed, accessibility requirements, and cost considerations.
What factors influence the choice between potting and encapsulation?
Potting and encapsulation are methods used in electronics manufacturing to protect sensitive components and circuits from environmental factors such as moisture, dust, and vibration. The choice between potting and encapsulation depends on various factors, including the specific application requirements, cost considerations, and the desired level of protection.
One crucial factor influencing the decision is the complexity and size of the electronic assembly. Potting typically involves filling an entire enclosure or casing with a liquid or semi-solid material such as epoxy resin. This method suits larger assemblies or components with irregular shapes where complete coverage is necessary. Encapsulation, on the other hand, involves applying a protective coating directly onto the electronic components. It is more suitable for smaller, more intricate assemblies where precision is essential.
Another consideration is the environmental conditions the electronic device will be exposed to during its lifespan. Potting is generally more robust and protects against harsh environments, including exposure to chemicals, extreme temperatures, and high moisture levels. Encapsulation, while offering good protection, may be less effective in highly demanding conditions.
Cost is also a significant factor in the decision-making process. Potting can be more expensive due to the more substantial material required and the additional labor filling the enclosure. Encapsulation, however, often requires less material and can be more cost-effective, especially for mass-produced electronic devices.
The desired level of repairability or reworkability is another factor to consider. Potting creates a permanent seal around the components, making it difficult to repair or replace individual parts without damaging the entire assembly. In contrast, encapsulation allows for easier access to the components, facilitating repair or replacement if necessary.
Furthermore, considerations such as electrical insulation properties, thermal conductivity, and compatibility with other materials used in the assembly process may also influence the choice between potting and encapsulation.
The decision to use potting or encapsulation depends on a combination of factors, including the complexity of the assembly, environmental conditions, cost considerations, repairability, and specific application requirements. By carefully evaluating these factors, manufacturers can determine the most appropriate method to ensure the reliability and longevity of their electronic products.
Which method offers better protection against moisture and environmental factors?
When considering protection against moisture and environmental factors, various methods can be employed, each with its advantages and limitations. Two commonly used methods are sealing and encapsulation.
Sealing involves applying a protective barrier to prevent moisture ingress and environmental exposure. This can be achieved through sealants, coatings, or membranes. Sealants are often applied to joints, seams, or gaps to create a tight barrier against moisture penetration. Coatings, such as paints or epoxies, can be used on surfaces to form a protective layer that shields against water and environmental elements. Membranes, typically made of rubber or PVC, cover larger areas and provide a durable barrier against moisture.
Encapsulation, on the other hand, involves completely enclosing an object or material within a protective barrier. This can be done using materials like plastics, resins, or polymers, which form a physical barrier around the item. Encapsulation effectively isolates the enclosed object from its surroundings, shielding it from moisture, humidity, and other environmental factors.
Both sealing and encapsulation offer advantages in protecting against moisture and environmental factors. Sealing is often more versatile and can be applied to various surfaces and structures. It suits small-scale applications like sealing electronic components and more significant projects like waterproofing buildings. It allows for targeted protection of specific areas prone to moisture intrusion.
On the other hand, encapsulation provides comprehensive protection by completely enclosing the protected item. This method is particularly effective for delicate or sensitive components that require complete isolation from moisture and environmental contaminants. Encapsulation can also offer superior durability and longevity than sealants or coatings, as the encapsulated object is fully protected from external wear and tear.
Both sealing and encapsulation offer effective protection against moisture and environmental factors, each with strengths and applications. The choice between the two methods depends on factors such as the nature of the object or structure being protected, the level of protection required, and the specific environmental conditions it will be exposed to.
Are there specific industries where potting is preferred over encapsulation, or vice versa?
Potting and encapsulation are techniques used in various industries to protect electronic components, circuitry, and assemblies from environmental factors such as moisture, dust, vibration, and shock. While they serve similar purposes, the two processes differ, and each may be preferred in different industries based on specific requirements.
Potting involves filling an electronic assembly or component with a liquid compound that hardens into a solid material, encasing the device entirely. This method provides excellent protection against environmental elements and mechanical stresses. Potting is often preferred in industries where robust protection is critical, such as aerospace, automotive, marine, and industrial equipment. These industries frequently deal with harsh operating conditions and require components that withstand extreme temperatures, moisture, and physical impact. Potting compounds offer high chemical resistance and can be tailored to meet specific performance criteria, making them suitable for demanding applications.
On the other hand, encapsulation involves applying a protective coating or molding material around the electronic component or assembly, leaving certain areas exposed for connections or ventilation. Encapsulation provides a barrier against moisture and contaminants while allowing for accessibility to the encapsulated device. This method is commonly used in industries such as consumer electronics, telecommunications, and medical devices, where the focus may be more on compactness, ease of maintenance, and cost-effectiveness. Encapsulation materials offer good protection while maintaining flexibility and electrical insulation properties, making them suitable for applications where space and weight considerations are essential.
While both potting and encapsulation offer protection for electronic components, their suitability depends on the industry’s specific requirements and application. Potting is favored in industries where maximum protection and durability are paramount, such as aerospace and industrial equipment. At the same time, encapsulation may be preferred in applications where space, accessibility, and cost-effectiveness are vital considerations, such as consumer electronics and medical devices. Ultimately, the choice between potting and encapsulation is determined by environmental conditions, mechanical stresses, accessibility needs, and budget constraints.
How does potting affect the heat dissipation of components compared to encapsulation?
Potting and encapsulation are methods used in electronics manufacturing to protect components from environmental factors such as moisture, dust, and mechanical stress. However, they have different effects on heat dissipation.
Potting involves filling a component’s entire housing or casing with a thermally conductive material, typically epoxy or silicone. This material surrounds the component, providing excellent protection against environmental factors. However, the potting material surrounding the component can impede heat dissipation. The encapsulated component becomes insulated within the potting material, making it difficult for the element’s heat to escape into the surrounding environment. This can lead to higher operating temperatures, potentially affecting the performance and reliability of the component, especially in high-power applications.
On the other hand, encapsulation involves coating only the component’s surface with a protective material, exposing the rest of the element. This allows for better heat dissipation than potting because it doesn’t wholly encase the component. Encapsulation materials are often chosen for their thermal conductivity properties, allowing the heat the element generates to be efficiently transferred to the surrounding environment. This helps maintain operating temperatures and preserve performance, particularly in applications where heat dissipation is critical.
While both potting and encapsulation offer protection for electronic components, potting tends to impede heat dissipation more significantly than encapsulation. Encapsulation allows for better thermal management by enabling heat to dissipate more effectively from the component’s surface. Therefore, when considering the choice between potting and encapsulation, the thermal requirements of the application should be carefully evaluated to ensure proper heat dissipation and optimal performance of the components.
Which method is more cost-effective: potting or encapsulation?
Potting and encapsulation are widely used techniques in electronics and engineering to protect sensitive components from environmental factors such as moisture, dust, vibrations, and shocks. Each method has its advantages and considerations in terms of cost-effectiveness.
Potting involves completely submerging the electronic component or assembly in a liquid resin or compound, which then hardens to form a protective shell around the device. This method protects against various environmental hazards and can be particularly effective for components exposed to harsh conditions. However, potting can be more labor-intensive and may require specialized equipment for mixing and dispensing the potting material. Additionally, the cost of the potting material itself can vary depending on factors such as volume, type of resin used, and desired properties (e.g., thermal conductivity).
Encapsulation, however, involves applying a protective coating or layer directly onto the surface of the electronic component or assembly. This method offers good protection against moisture and dust ingress and can be more cost-effective than potting in specific scenarios. Encapsulation materials such as conformal coatings are often applied using spray, dip, or brush methods, which can be less labor-intensive than potting. Furthermore, encapsulation materials generally require less volume than potting compounds, potentially lowering material costs.
When considering cost-effectiveness, several factors need to be considered beyond material and labor costs. These include the complexity of the component or assembly, desired level of protection, production volume, and potential rework or repair costs. For example, potting may be more cost-effective for high-value components or assemblies that require maximum security. At the same time, encapsulation may be sufficient and more economical for simpler or lower-cost devices.
The choice between potting and encapsulation depends on various factors, and there is no one-size-fits-all answer in terms of cost-effectiveness. Both methods have advantages and limitations, and the optimal solution will depend on the specific requirements and constraints of the application.
Can potting or encapsulation affect the performance of electronic components?
Potting or encapsulation is commonly used in electronic manufacturing to protect components from environmental factors such as moisture, dust, vibration, and temperature fluctuations. While potting can provide significant benefits in terms of durability and reliability, it can also affect the performance of electronic components in several ways.
Firstly, the choice of potting material is critical. Different materials have varying thermal conductivity properties, which can affect heat dissipation from the components. Improper selection of potting material with low thermal conductivity may result in heat buildup within the enclosure, leading to thermal stress on the components and potentially causing performance degradation or failure over time.
Additionally, the potting process can introduce mechanical stresses on delicate electronic components. The curing process of potting materials involves thermal and chemical reactions that may exert pressure on the components, mainly if carried out with little precision. This mechanical stress can damage sensitive components or alter their electrical characteristics, leading to deviations in performance.
Furthermore, potting materials may have dielectric properties that can affect the electrical behavior of components. High dielectric constants of certain potting materials can lead to capacitance effects, affecting signal integrity and introducing parasitic capacitance in high-frequency circuits. This can result in signal attenuation, distortion, or interference, impacting the overall performance of the electronic system.
Moreover, potting materials may also introduce issues related to outgassing. Some potting materials may release volatile compounds during the curing process or when subjected to elevated temperatures. These compounds can contaminate sensitive components, such as optical surfaces or sensor elements, affecting their performance or longevity.
While potting or encapsulation is essential for protecting electronic components from environmental hazards, it can impact their performance if not executed carefully. Proper material selection, precise application techniques, and thorough testing are crucial to mitigate any adverse effects and ensure optimal performance and reliability of electronic systems.
What are some common challenges associated with potting?
Potting and encapsulating electronic components or assemblies in a protective compound or potting material can present various challenges. Some common challenges associated with potting include:
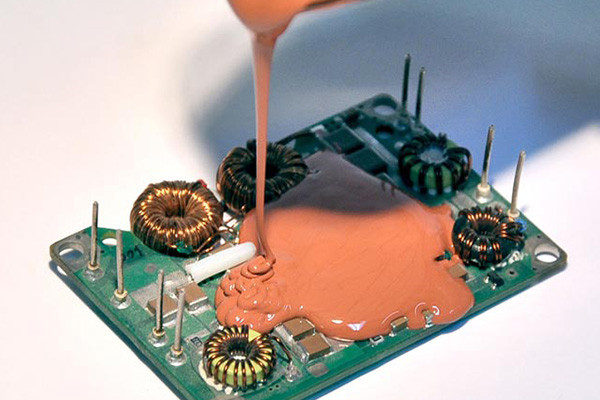
- Material Selection: Choosing the suitable potting material is crucial for achieving desired performance characteristics such as thermal conductivity, electrical insulation, adhesion properties, and resistance to environmental factors like moisture, chemicals, and temperature extremes.
- Adhesion: Ensuring proper adhesion between the potting material and the substrate is essential for preventing delamination or separation, which can compromise the protection offered by the potting compound.
- Void Formation: The formation of voids or air pockets within the potted assembly can occur due to improper mixing, inadequate degassing, or insufficient flow properties of the potting material. Voids can lead to reduced mechanical strength and compromised protection against environmental factors.
- Curing Time and Conditions: Potting materials typically require specific curing times and conditions (temperature, humidity, etc.) for proper polymerization and curing. Adherence to these parameters can result in complete curing, reduced mechanical properties, or long-term degradation of the potting material.
- Thermal Management: In applications where heat dissipation is critical, improper potting can impede thermal conductivity, leading to overheating electronic components and degradation of performance or reliability.
- Component Compatibility: Some potting materials may be incompatible with specific electronic components or substrates, leading to issues such as corrosion, chemical reactions, or dimensional changes that can affect the performance or reliability of the assembly.
- Encapsulation Uniformity: Achieving uniform components encapsulation within the potting material is essential for ensuring consistent protection and mechanical stability. Inadequate encapsulation can leave certain areas vulnerable to damage or environmental factors.
- Cost and Process Efficiency: Potting can add cost and complexity to manufacturing processes. Finding a balance between adequate protection and cost efficiency, as excessive potting material usage or complex application processes can increase production costs.
- Repairability and Rework: Once components are potted, access for repair or rework becomes challenging. Planning for future maintenance or repairs is essential, especially in applications where components may need to be replaced or upgraded periodically.
- Environmental Considerations: Potting materials should be selected considering ecological regulations and requirements, particularly regarding hazardous substances or disposal methods.
Addressing these challenges often involves careful planning, thorough testing, and collaboration between material suppliers, manufacturers, and engineers to ensure the successful potting of electronic assemblies.
What are some common challenges associated with encapsulation?
Encapsulation is a fundamental principle in object-oriented programming (OOP) that involves bundling data and methods that operate on that data into a single unit, typically referred to as a class. While encapsulation offers numerous benefits such as data hiding, abstraction, and modularity, it also introduces certain challenges that developers need to address:
- Maintaining Consistency: Ensuring that the internal state of an object remains consistent can be challenging, especially in complex systems where multiple methods might be modifying the object’s state concurrently. Synchronization mechanisms such as locks or semaphores may be required to prevent race conditions and maintain data integrity.
- Access Control: Determining the appropriate level of access control for class members can be tricky. Making data members private ensures encapsulation but might restrict flexibility in certain scenarios where derived classes or external components require access. Striking a balance between encapsulation and accessibility is crucial.
- Performance Overhead: Encapsulation often involves method invocations and indirection, which can introduce a performance overhead compared to direct access to data. While modern compilers and runtime environments optimize method calls, excessive encapsulation layers or frequent access to encapsulated data can impact performance.
- Testing and Debugging: Encapsulated code can be challenging to test and debug, particularly when dealing with private members or complex interactions between objects. Unit testing frameworks and debugging tools need to be employed effectively to ensure that encapsulated components behave as expected and can be diagnosed easily.
- Dependency Management: Tight coupling between classes can hinder code maintainability and reusability. Changes to the implementation of one class might necessitate modifications in dependent classes, leading to cascading changes throughout the codebase. Employing design patterns such as Dependency Injection can help mitigate these issues by decoupling dependencies.
- Serialization and Persistence: Objects encapsulate their state, which can pose challenges when serializing objects for storage or transmission. Ensuring that encapsulated data can be serialized and deserialized efficiently without compromising encapsulation requires careful consideration of serialization mechanisms and object lifecycle management.
Addressing these challenges requires a deep understanding of encapsulation principles, coupled with sound software design practices. By carefully managing access control, minimizing performance overhead, and mitigating dependencies, developers can harness the benefits of encapsulation while effectively managing its associated challenges.
Can potting or encapsulation be applied to sensitive electronic components?
Potting or encapsulation is a common technique used in electronics manufacturing to protect sensitive electronic components from environmental factors such as moisture, dust, vibration, and shock. It involves covering the components with a protective material, typically a resin or polymer, to create a barrier that shields them from external elements.
Sensitive electronic components, such as integrated circuits (ICs), microprocessors, sensors, and other semiconductor devices, can greatly benefit from potting or encapsulation. These components are often vulnerable to damage or malfunction when exposed to harsh conditions, which can decrease their reliability and performance.
The potting or encapsulation process begins with selecting a suitable material that provides the desired level of protection while maintaining compatibility with the encapsulated components. Epoxy resins are commonly used due to their excellent electrical insulation properties, chemical resistance, and ability to adhere to various substrates. Silicone-based materials are also popular because of their flexibility, thermal stability, and resistance to moisture and extreme temperatures.
Once the material is chosen, the sensitive components are placed in a mold or fixture, and the liquid resin is poured or injected to completely cover them. The resin is then allowed to cure or harden, forming a solid protective layer around the components. Depending on the application requirements, the encapsulated components may undergo additional curing processes, such as heat or UV exposure, to ensure proper adhesion and stability of the encapsulant.
Potting or encapsulation provides several benefits for sensitive electronic components:
- Environmental protection:The encapsulating material forms a barrier that shields the components from moisture, dust, chemicals, and other contaminants in the surrounding environment.
- Mechanical stability:Encapsulation helps to reinforce the structural integrity of the components, reducing the risk of damage from vibration, shock, or mechanical stress.
- Electrical insulation:The encapsulant provides electrical insulation, preventing short circuits and leakage currents that could compromise the performance of the electronic devices.
- Enhanced reliability:By protecting sensitive components from environmental factors and mechanical stress, potting or encapsulation can improve the reliability and longevity of electronic devices, especially those used in demanding applications such as automotive, aerospace, and industrial systems.
Potting or encapsulation is a highly effective method for safeguarding sensitive electronic components, ensuring their continued functionality and performance in challenging operating environments.
Are there any special considerations for potting or encapsulation in high-vibration environments?
Potting or encapsulation in high-vibration environments requires careful consideration to ensure the integrity and reliability of the electronic components or devices. Here are some key considerations:
- Material Selection: Choosing the right potting or encapsulation material is crucial. It should have excellent vibration damping properties to absorb mechanical shocks and vibrations. Silicones, polyurethanes, and epoxy resins are commonly used due to their flexibility and ability to adhere to various surfaces.
- Compliance with Standards: Ensure that the potting material complies with relevant industry standards for vibration resistance, such as MIL-STD-810 for military applications or IEC 60068 for general environmental testing.
- Proper Encapsulation Technique: The potting process must be carried out carefully to eliminate voids or air bubbles within the encapsulant. Vacuum potting or pressure potting techniques can help ensure complete coverage and minimize the risk of delamination or cracking under vibration.
- Mechanical Reinforcement: In some cases, reinforcing agents such as fiberglass or microspheres can be added to the potting material to enhance its mechanical strength and resistance to vibration-induced stress.
- Thermal Management: Consideration should be given to the thermal properties of the potting material to ensure efficient heat dissipation from enclosed components, as excessive heat buildup can weaken the encapsulant and compromise its vibration resistance over time.
- Compatibility with Components: Verify that the potting material is compatible with the components being encapsulated, including sensitive electronic circuits, connectors, and conductive traces. Some materials may interact chemically with certain components, leading to corrosion or electrical malfunctions.
- Testing and Validation: Conduct rigorous testing and validation procedures to assess the performance of the encapsulated devices under simulated high-vibration conditions. Accelerated life testing and vibration testing can help identify potential weaknesses and optimize the potting process.
By addressing these considerations, engineers can effectively pot or encapsulate electronic components for use in high-vibration environments, ensuring reliability and longevity in demanding applications such as automotive, aerospace, and industrial machinery.
How do potting and encapsulation contribute to the overall reliability of electronic systems?
Potting and encapsulation are essential processes in electronic systems manufacturing, contributing significantly to their overall reliability. These techniques involve encasing electronic components or assemblies in a protective material, typically a resin or polymer. Here’s how potting and encapsulation enhance reliability:
- Environmental Protection: One of the primary functions of potting and encapsulation is to shield electronic components from environmental factors such as moisture, dust, dirt, and chemical exposure. Potting and encapsulation prevent these external elements from corroding or damaging sensitive electronic parts by sealing the components within a protective barrier. This protection is crucial for electronic systems deployed in harsh environments, such as automotive, aerospace, or industrial applications.
- Mechanical Stability: Potting and encapsulation support delicate electronic components, preventing them from experiencing mechanical stresses due to vibrations, shocks, or physical impacts. The encapsulating material reinforces the assembly’s structural integrity, reducing the risk of component displacement or damage during handling, transportation, or operation. This mechanical stability enhances the overall robustness of electronic systems, especially in rugged or high-vibration environments.
- Electrical Insulation: Potting and encapsulation materials are often electrically insulating, preventing electrical current flow. By encapsulating electronic components, these materials insulate them from each other and external conductive elements, reducing the risk of short circuits or electrical interference. This insulation is crucial for maintaining the integrity and functionality of electronic circuits, particularly in densely populated assemblies where components are nearby.
- Thermal Management: Some potting and encapsulation materials possess excellent thermal conductivity properties, effectively dissipating heat generated by electronic components. By encapsulating heat-generating components such as power semiconductors or integrated circuits, these materials help maintain optimal operating temperatures, prolonging the lifespan and reliability of the electronic system. Efficient thermal management also reduces the risk of overheating-induced failures and ensures consistent performance over time.
Potting and encapsulation significantly enhance the reliability of electronic systems by providing environmental protection, mechanical stability, electrical insulation, and thermal management. These techniques are essential for ensuring electronic devices’ longevity, functionality, and performance, particularly in demanding operating conditions.
Conclusion:
In conclusion, while potting and encapsulation safeguard electronic components or assemblies, they differ significantly in their application methods, materials used, and intended purposes. Potting entails completely immersing components in a protective material to shield them from environmental factors, while encapsulation involves enclosing components within a protective shell or coating. By grasping the disparities between these techniques, manufacturers can make informed decisions to ensure the longevity and reliability of their products in diverse applications.
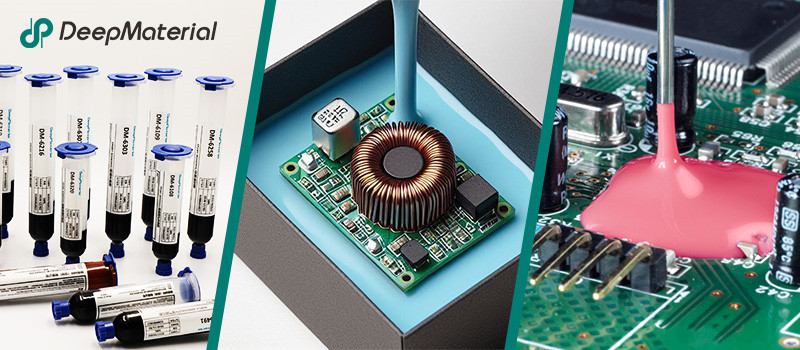
About DeepMaterial
DeepMaterial is a trusted supplier of encapsulant materials that are used in electronics manufacturing worldwide. From chip on board encapsulants such as glob top material to conformal coatings, underfills, low pressure molding, and potting solutions, DeepMaterial offers a full range of circuit board protection materials that effectively protect circuit boards while help reduce costs. More…Deepmaterial is a the manufacturer of epoxy adhesives including hardeners, metalbond, and metal filled resins. Structural, toughened medium viscosity, and non-sag adhesives are also offered. Some adhesives are resistant to thermal shock, chemical, vibration dampening, and impact. Suitable for metals, plastics, wood, and ceramics. Serves electronics, aerospace, automotive, tooling, marine, and construction industries. REACH and RoHS compliant. FDA approved. UL listed. Meets military specifications. We are the one of best adhesive manufacturers in China.
Blogs & News
Potting compounds are at the frontline of electronics assembly, delivering effective protection in challenging environmental conditions while improving mechanical strength and offering high electric insulation. Used within a variety of industries, electrical potting compounds are found within a broad range of consumer electronics, as well as used in applications across the automotive, aerospace, and other industries where electronic assemblies are prevalent.
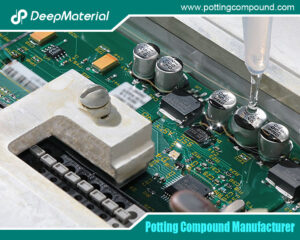
Silicone Potting Compound for Electronics
Silicone Potting Compound for Electronics In the rapidly evolving world of electronics, ensuring the reliability, durability, and performance of electronic components is paramount. One critical
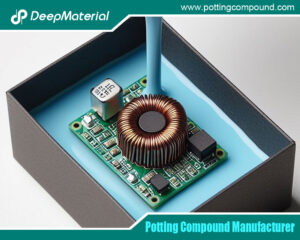
Potting Compound vs. Epoxy: A Comprehensive Comparison
Potting Compound vs. Epoxy: A Comprehensive Comparison In the world of electronics, manufacturing, and material encapsulation, two terms frequently come up: potting compounds and epoxy.
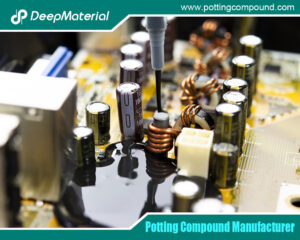
Potting Compound for PCB
Potting Compound for PCB A potting compound is a liquid or semi-liquid material that is poured or injected over a PCB or electronic assembly, then
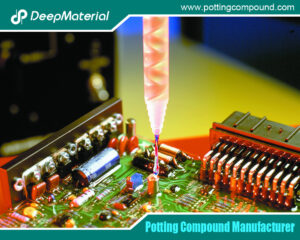
In – depth Analysis of the Curing Characteristics of Electronic Potting Compounds
In – depth Analysis of the Curing Characteristics of Electronic Potting Compounds Electronic potting compounds play a vital role in the electronics industry. They can
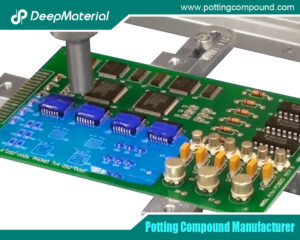
A Comprehensive Analysis of the Environmental Performance of Encapsulating Materials: From Regulations to Practices
A Comprehensive Analysis of the Environmental Performance of Encapsulating Materials: From Regulations to Practices In modern industrial manufacturing, encapsulating materials are widely used in numerous

A Comprehensive Analysis of PCB Encapsulation Quality Inspection: Innovative Application of Non-Destructive Testing Technologies
A Comprehensive Analysis of PCB Encapsulation Quality Inspection: Innovative Application of Non-Destructive Testing Technologies In the field of electronic manufacturing, the encapsulation process of printed